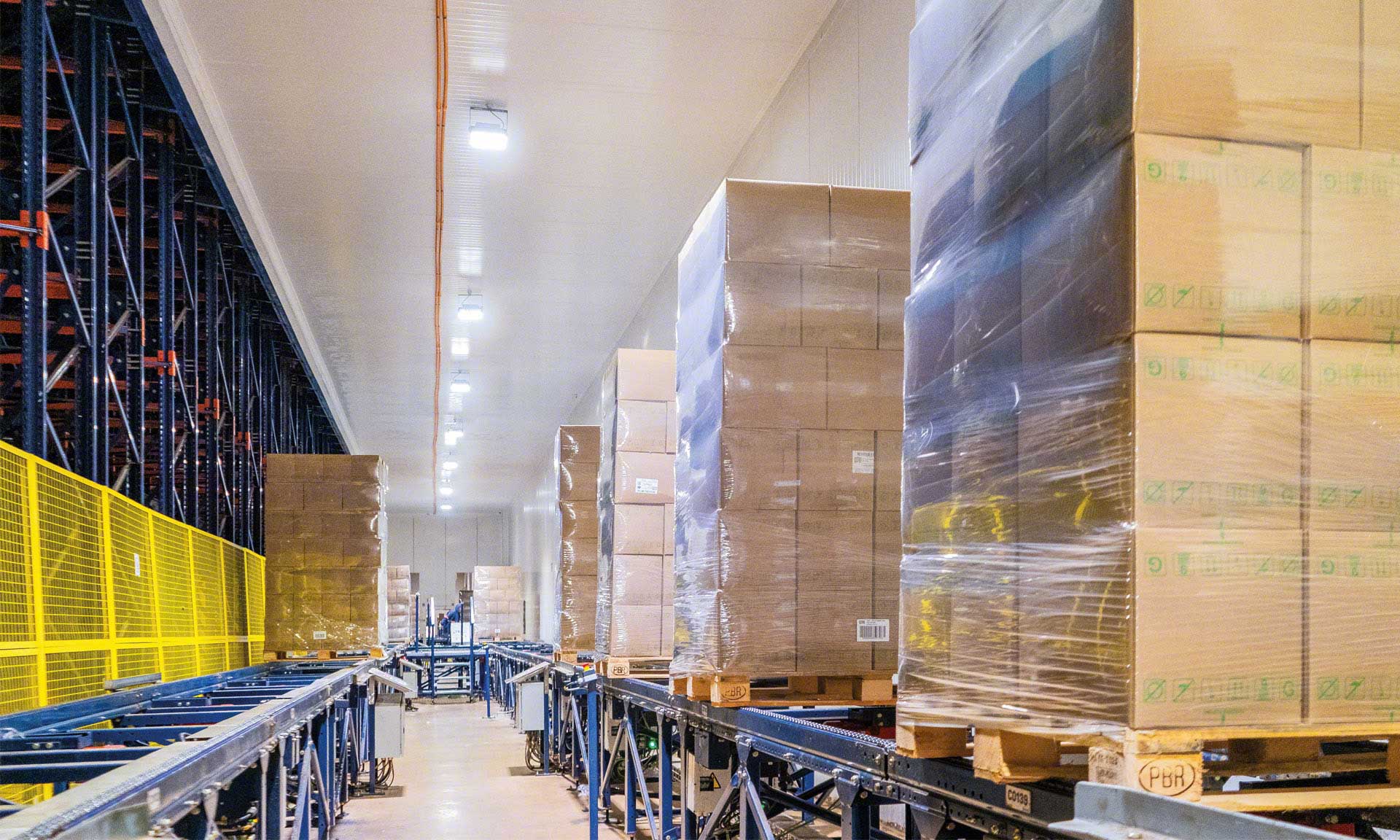
Bem Brasil manages 551,000-plus tons of frozen food with the Automated Pallet Shuttle
The company doubles its frozen food production capacity with a high-density automated storage system and Easy WMS software.
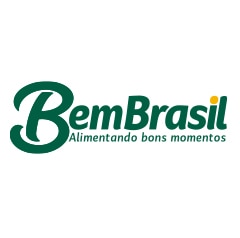
Bem Brasil automates its logistics operations with a rack-supported building and the Automated Pallet Shuttle. The Mecalux solution has improved traceability, inventory control, and efficiency in shipping goods at -13 °F in the company’s Perdizes plant.
Bem Brasil: Healthy, balanced, and sustainable food
Founded in 2006 in Araxá, Bem Brasil specializes in producing frozen pre-cooked french fries and dehydrated potato flakes. Over 20 years, it has become the national leader in its sector, with 2 factories and more than 1,300 employees, and one of Brazil’s most popular household brands.
CHALLENGES
|
SOLUTIONS
|
BENEFITS
|
---|
Bem Brasil is the leading producer of frozen pre-cooked french fries in Brazil. The company recently shored up its logistics capacity with the construction of two automated rack-supported buildings in its plant in Perdizes (Minas Gerais). Both facilities are equipped with Mecalux’s Automated Pallet Shuttle system with a stacker crane. They operate at -13 °F to ensure the efficient storage and shipment of frozen products.
“Our production capacity is over 550,000 tons of goods per year. This allows us to cover up to 55% of national demand with a catalog of more than 20 items aimed at both the foodservice and retail markets,” says Célio Zero, Operations Manager at Bem Brasil. The company also exports to several South American countries, as well as Taiwan, Singapore, the US, and Mexico, where it holds a commercial partnership with Walmart.
Over the past year, the business has increased production by 10% and revenues by 30%. One key driver of this growth was product diversification. The Perdizes plant, equipped with advanced technology, manufactures specialties such as onion rings and smiley fries (carinhas), among others.
According to Zero, Covid-19 changed Bem Brasil’s customer profile: “Before the pandemic, 70% of our production was for the hospitality channel and 30% for retail. But since then, the split has shifted to 50/50.”
A scalable solution to support Bem Brasil’s growth
Bem Brasil’s logistics project was carried out in two stages. In the first phase, the company built a freezer warehouse with Mecalux to meet its immediate storage needs. As production and demand continued to grow, a second facility was added, doubling the logistics capacity to 66,000 pallets.
From the start, the solution was designed with a long-term vision; it had to be scalable and adaptable to the company’s growth pace. This strategy has enabled Bem Brasil to expand its infrastructure without operational disruptions, strengthening its commitment to efficient, automated, and future-ready logistics.
Innovation in subzero automated storage
“Mecalux’s Automated Pallet Shuttle system brings us multiple logistical benefits: faster shipping processes, improved food handling safety, online inventory control, and energy savings,” says Zero.
The two freezer warehouses store nearly 66,000 pallets of raw materials and finished goods. They consist of five aisles, each 469' long, and 82-foot-high racking blocks. The facilities are clad-rack, meaning the racks themselves support the building.
Inside, the Automated Pallet Shuttle system stores and retrieves goods autonomously, speeding up pallet putaway and dispatch operations. Conveyors automatically connect the automated warehouses with the production and shipping areas.
Bem Brasil’s shipping zone features a large staging area. There, a transfer car distributes finished goods into one of 20 flow channels, each capable of holding seven pallets. Vertical doors separate this space from the rest of the warehouse, maintaining temperature control and preventing cold air loss.
The mastermind behind logistics automation
At the Perdizes plant, automated logistics operations are complemented by Mecalux’s warehouse management system. This software coordinates and streamlines all in-house processes.
Easy WMS oversees the receipt, storage, and shipment of frozen products in real time, ensuring full traceability and optimal inventory control. With this tool, Bem Brasil maximizes the productivity of its warehouses.
During order shipping, the logistics software applies the FEFO (first expired, first out) strategy. Prioritizing items with the earliest best-by date optimizes inventory turnover, minimizes waste, and preserves product quality through delivery.
“Easy WMS gives us complete control over all stored goods. That translates into faster, safer, and more cost-effective logistics operations,” says Zero.
A logistics solution built for growth
Bem Brasil’s warehouse automation project in Perdizes underscores the company’s commitment to tailoring its logistics processes to food industry demands. With the Automated Pallet Shuttle system and Easy WMS, the company guarantees a continuous supply to both domestic and international customers. This logistics infrastructure supports Bem Brasil’s sustained growth and dedication to quality and innovation.
Mecalux’s Automated Pallet Shuttle system brings us multiple logistical benefits: faster shipping processes, improved food handling safety, online inventory control, and energy savings.
Gallery

Bem Brasil’s automated rack-supported buildings in Perdizes (Brazil)
Ask an expert