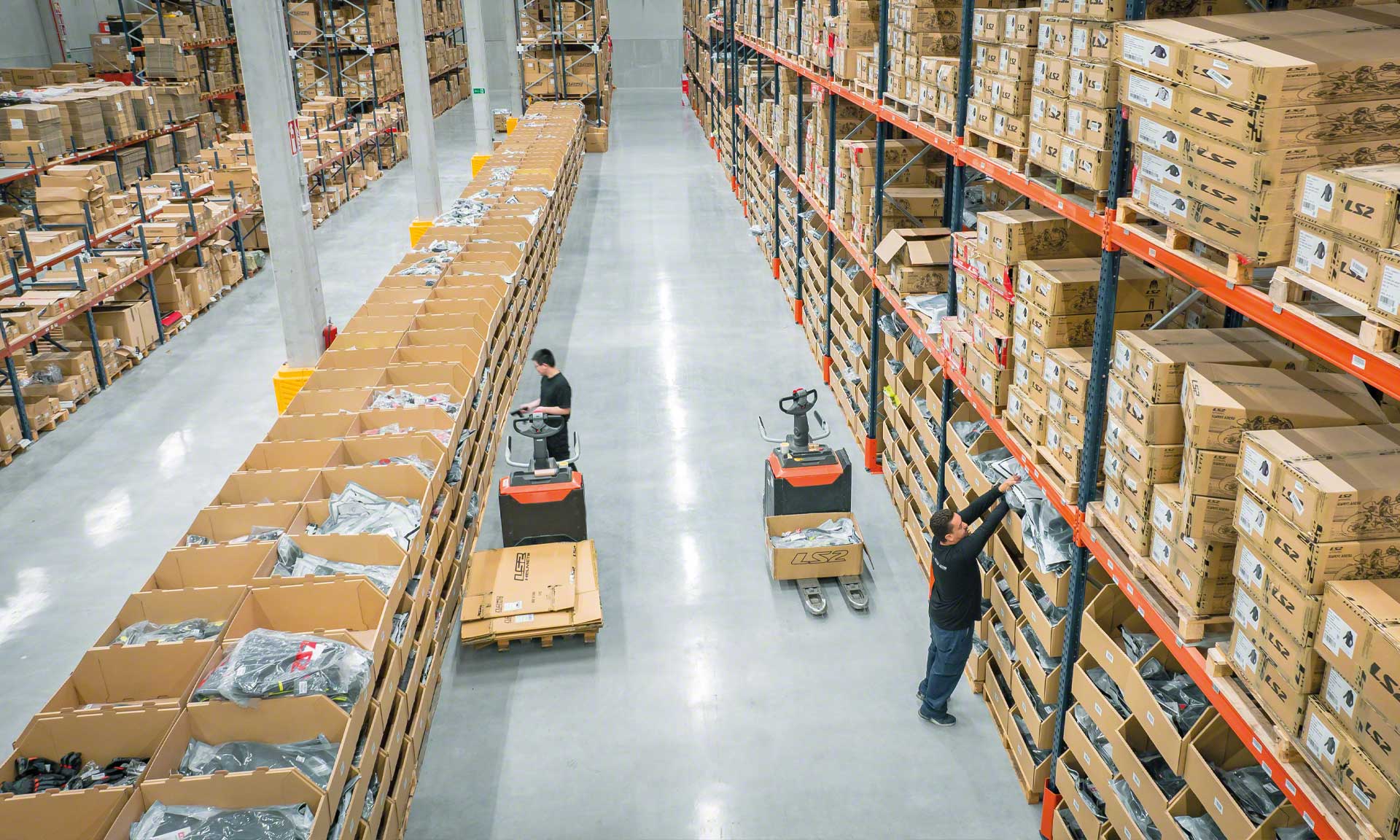
LS2 Helmets digitizes its warehouse operations with Easy WMS
Motorcycle helmet and apparel company LS2 Helmets tackles the distribution of 4,500 helmets a day with Easy WMS.
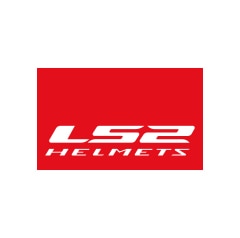
Motorcycle helmet and apparel company LS2 Helmets has digitized its warehouse in Terrassa (Barcelona, Spain) to streamline order picking. With this system, the company can prepare around 400 orders a day — i.e., 4,500 helmets — which are distributed throughout Europe.
LS2 Helmets: heading the motorcycling market
LS2 Helmets is a motorcycle gear and clothing company with a worldwide presence. From its production center in China, the business distributes its goods to Australia, Asia, and South America. It also markets its products in the US and Canada through four logistics providers. LS2 Helmets supplies the European market from its facility in Terrassa (Barcelona, Spain) and the UK market from its warehouse in England.
- Founded in: 2007
- No. of employees: 40+
- Turnover (2021): $61.5 million
- No. of SKUs: 5,000+
CHALLENGES
|
SOLUTIONS
|
BENEFITS
|
---|
If there is one thing that characterizes LS2 Helmets, it is its growth. To cope with burgeoning demand, the motorcycle helmet and apparel company has had to adapt its logistics processes over its 15-plus years on the market. The figures speak for themselves: “In recent years, we’ve grown by over 20%, bringing in $61.5 million in 2021,” says Lluís Azorín, Warehouse Manager at LS2 Helmets.
The company has moved from one facility to another numerous times to increase its storage capacity and accommodate a growing number of items. “Our future strategy consists of scaling up our product catalog with new solutions for riders,” says Azorín.
The steady rise in the number of items to be stored in the facility, however, made operations much more complicated. Thus, the company opted to outsource the storage and management of part of its products to logistics providers.
“In 2017, we dispatched around 1,800 helmets a day. In 2022, we can ship 4,500 in a single day,” says Azorín. With not enough space in its warehouse, the business found it difficult to cope with such a high work rate. “We decided to buy a new, 2.5-acre facility in Terrassa to store all our products and to bring everything we’d outsourced back in-house. This serves as our operations hub: from here, we distribute orders to all our European customers, mainly Germany, France, Spain, and Italy,” says Azorín.
In its new center, LS2 Helmets manages over 5,000 SKUs spanning the brand’s entire product family: helmets, apparel, accessories, gloves, eyewear, and boots. With such a large amount of stock, the risk of error is very high. Therefore, the company needed a system that would coordinate processes and keep comprehensive control over its items.
“In our former facility, we used Mecalux’s Easy WMS warehouse management software to control the goods and organize operations. When we moved to the new center, we knew we wanted to continue relying on Easy WMS since we were so happy with the results the first time around,” says Azorín.
Flexible logistics to keep pace with changes
To efficiently respond to climbing demand, LS2 Helmets required smooth supply chain operations. “With Easy WMS, we were looking to streamline our warehouse processes and facilitate the work of our operators,” says Azorín.
The software from Mecalux tells these employees which aisles to go to and which locations to pick products from. Following step-by-step instructions from Easy WMS on their RF scanners, the center’s 20 operators are much more diligent and have minimized mistakes in goods management.
“Easy WMS is an intuitive, user-friendly software program. Staff turnover is very high in our business, and new employees who join the team learn how to use Easy WMS in no time,” says Azorín.
The Easy WMS software orchestrates and intervenes in all operations in the LS2 Helmets facility, from location management to order picking and dispatch. The system is designed to streamline all processes, ensuring that operators travel the minimum distances through the building to be more efficient.
Goods receipt and storage
Every day, the warehouse receives two containers with around 4,600 product units from the LS2 Helmets production center in China.
The operators identify all the goods by reading their barcodes. This way, the items are recorded in the Easy WMS database, and the software assigns them a location in line with, e.g., the type of product or its demand level.
The correct distribution of the goods has a direct impact on all other tasks in the facility. It makes it easier for operators to find the locations they have to deposit products in or the items they need to complete orders.
“The main criterion for goods distribution in our center is turnover. We classify products as A, B, or C according to sales and then assign each type of turnover to a specific zone. For instance, our top sellers — type A items — are placed on racks near the loading docks to expedite their entry and exit,” says Azorín.
Order processing
Order picking is one of the most demanding operations in the LS2 Helmets warehouse. Every day, around 400 orders — i.e., 4,500 helmets — are prepared and distributed throughout Europe.
To handle such a substantial volume of orders, picking tasks have to be organized to a T. “The work is divided among the operators, into large orders containing many items, and small orders,” says Azorín.
Four types of orders are filled in the LS2 Helmets facility:
- Large orders (more than 36 product units). Each operator is assigned to a single order. This worker travels around the center, removing items from the racks and subsequently packing them.
- Medium-sized orders (fewer than 36 product units and over six helmets). Operators perform batch picking: they walk around the warehouse, collecting goods and placing them in a cart that they then move to the consolidation area. Once there, they sort the items into a putwall with 10 cubbies, each corresponding to an order.
- Small orders (two to six product units). Operators perform batch picking (as described with medium-sized orders). Once at the consolidation zone, they sort the items into a putwall with 25 cubbies, each corresponding to an order.
- Single-unit orders. Operators locate the item requested, remove it from the racks, and directly pack it and take it to the loading docks.
Once the orders have been picked, they are moved to the consolidation area, where they are packed.
Order dispatch
LS2 Helmets has equipped its facility with the Multi Carrier Shipping Software module. This extension of Easy WMS includes functionalities that make order packing, labeling, and shipping more efficient.
The program guides operators at every turn. It tells them which items to pack and whether to group them in single- or multi-unit loads depending on their sizes.
Then, Multi Carrier Shipping Software ensures that the packages and pallets are properly labeled. Each label features the tracking number with which customers can monitor their orders in real time.
“One of the things we most like about Multi Carrier Shipping Software is that it integrates with carriers,” says Azorín. Thanks to this communication, the module sends the shipping companies the relevant documentation (e.g., the number of packages to be delivered). In turn, these agencies send LS2 Helmets the data to create the labels and tracking numbers. When the carriers arrive at the facility, they merely need to pick up the prepared orders because they have all the information in their system automatically.
Future prospects
“We plan to keep growing with the addition of new products to our portfolio,” says Azorín. To house more stock without error, the company needs to organize all its goods effectively in addition to its warehouse processes. The order and control provided by Easy WMS help drive the business’s supply chain.
Digitized management is essential for monitoring everything that happens in the center and making strategic improvements based on objective data. With Easy WMS, LS2 Helmets has an optimized facility. Operations are performed in the shortest possible time to guarantee fast order distribution.
Easy WMS has become a key tool for global player LS2 Helmets: its more than 5,000 SKUs in stock are under tight control to ensure that orders are prepared and distributed on time.
For the past few years, we’ve seen year-on-year growth of over 20%. With Easy WMS, we intend to boost our supply chain, which will help us bolster our future expansion prospects.
Gallery
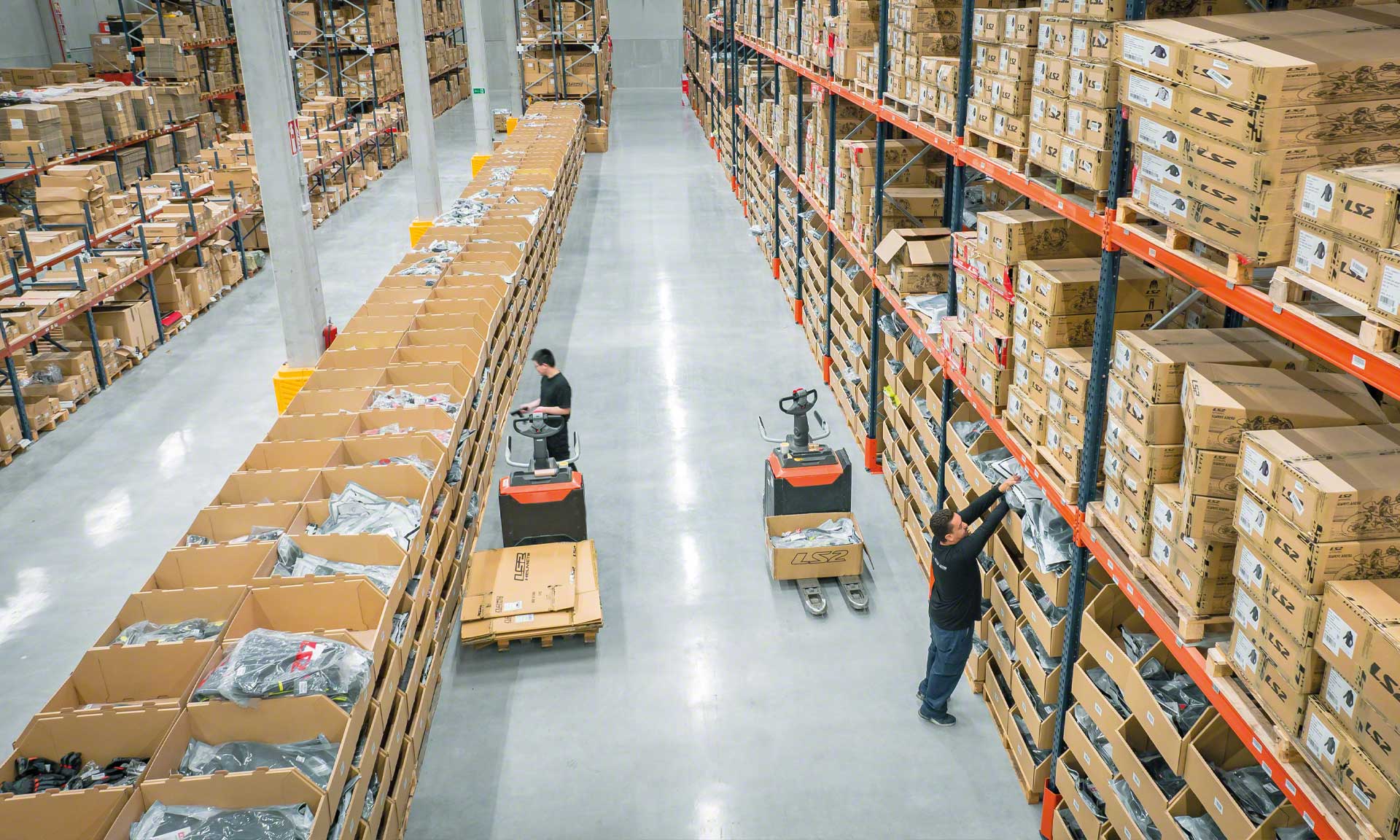
Pallet racks in the LS2 Helmets warehouse in Terrassa, Spain
Ask an expert