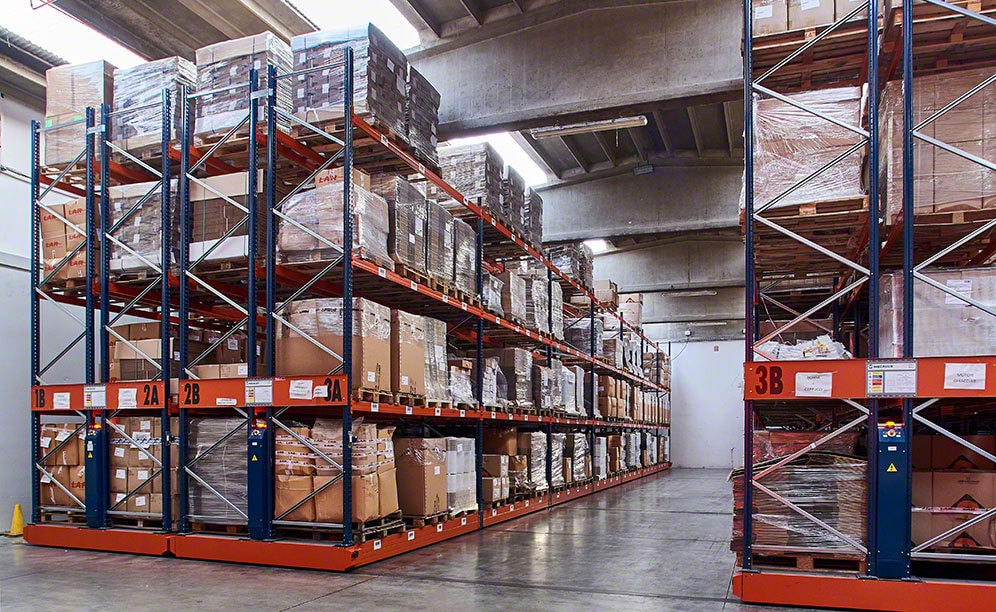
LAR: increased speed and capacity with three compact systems
The combination of solutions has cut the time spent loading and unloading products on and from the racks by 50%
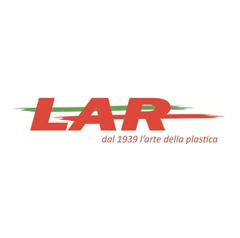
Thermoplastic resins company LAR is continually expanding, and, for that reason, it needed to enlarge and renovate its production plant in Campogalliano, Italy. This facility has multiple storage areas where 108 SKUs of semi-finished and finished products are managed. To organize the goods based on their characteristics and turnover, Interlake Mecalux has installed three storage systems: drive-in, pallet flow storage and Movirack pallet racking. The combination of these three solutions has helped to optimize the available surface area and reduce the time it takes to load and unload items on and from the racks by 50%.
Transformation and growth
With over 70 years of experience, LAR is a leading Italian firm in the field of thermoplastic resin processing. These resins are mainly used in the manufacture of bottles and containers for storing and handling chemical, food and cleaning products.
As a company committed to the environment, it constantly researches how to develop biodegradable products — made from renewable resources — more efficiently and affordably.
In the small town of Campogalliano (northern Italy), LAR boasts a 9.88 acre production plant that has been expanded on numerous occasions to cope with the business’s continuous growth. It has various storage areas where it manages 108 SKUs (of both semi-finished and finished goods). Operators have to bring the semi-finished products to the production lines at just the right time and, once there, pick and store the finished merchandise.
LAR Plant Manager Riccardo Monari explains, “Given the significant expansion of the plant in Campogalliano, we needed new storage structures.”
Semi-finished goods
According to Riccardo Monari, “Our priority was to maximize the storage space to accommodate as many pallets as possible.” Taking this into account, Interlake Mecalux has installed a Movirack mobile racking unit with capacity for 1,040 pallets with semi-finished products.
The racks, which stand 22 feet high and have four levels, are placed on mobile bases that move both laterally and independently. They comprise a high-density storage system that provides direct access to the merchandise. By opening one working aisle, operators gain access to the locations where they need to deposit or remove the goods. This optimizes the storage area.
As the racking is fitted with sliders and electronic equipment, its movements are completely safe. The racks are equipped with devices that stop them from moving in the event of an incident (for example, the presence of objects in the aisle, which would prevent the system from functioning properly).
Finished products
Two differentiated areas have been set up, and Interlake Mecalux has fitted them out with both drive-in and pallet flow racking to store finished goods. These racks hold 2,125 pallets that are subsequently distributed to LAR’s customers all over the globe. The drive-in racks comprise three-level-high lanes. This solution reduces the number of aisles in the interest of maximizing space and, as a result, increases storage space.
The racks are extremely easy to use. Aided by reach trucks, operators enter the storage lanes with the merchandise raised above the level where it will be placed. Guide rails have been installed in the floor to ensure that these trucks travel safely inside the lanes.
The flow racking, on the other hand, is made up of a set of slightly sloped channels that facilitate the proper movement of the pallets from the highest part (entry point) to the lowest part (exit point). “We wanted a solution that would allow us to manage products according to the FIFO (first in, first out) method quickly and without needing to spend a lot of time loading and unloading,” notes Riccardo Monari.
The racks are 24.6’ high and have six levels. They consist of 99 channels measuring 39’ deep that hold 10 pallets. This solution streamlines the loading and unloading of goods while guaranteeing continuous product flows. Operator maneuvers are minimal, as workers merely need to insert or remove the pallets in or from their corresponding locations.
Controlled merchandise
“With Mecalux’s storage systems, we’ve leveraged the entire space,” stresses LAR’s Plant Manager. The combination of three high-density storage systems has helped the company to make the best use of its surface area and efficiently manage its goods. Each racking solution has been designated to store a specific product based on its characteristics and demand level.
“We have also slashed the time spent inserting and extracting pallets to and from their locations by 50%,” highlights Monari. The Movirack, pallet flow and drive-in racks not only provide the largest possible storage capacity, but are also designed to facilitate warehousing tasks. Consequently, the firm can distribute 250 pallets a day without delay.
“Last, but not least, I have to point out that Mecalux met the deadlines set for the assembly of the warehouse. The process was quick and precise,” adds Riccardo Monari. Mecalux’s priority was for LAR to be able to provide its clients with service as soon as possible.
The combination of three different storage solutions has helped us to make the most of our space. Plus, the pallet flow racking has cut the time taken moving pallets to and from their locations by 50%.
Advantages for LAR
- Three systems in one warehouse: by combining three storage solutions, goods are sorted based on their characteristics (semi-finished or finished products) and turnover rate.
- Boosted storage capacity: the drive-in, pallet flow storage, and Movirack racking solutions account for a total storage capacity of 3,165 pallets.
- Agility in handling: LAR has shortened the time taken to insert and extract pallets in and from the racks by 50%.
Movirack mobile racking | |
---|---|
Storage capacity: | 1,040 pallets |
Pallet sizes: | 32” x 47” |
Max. pallet weight: | 1,000 lb |
Racking height: | 22’ |
Racking length: | 85’ |
Gallery
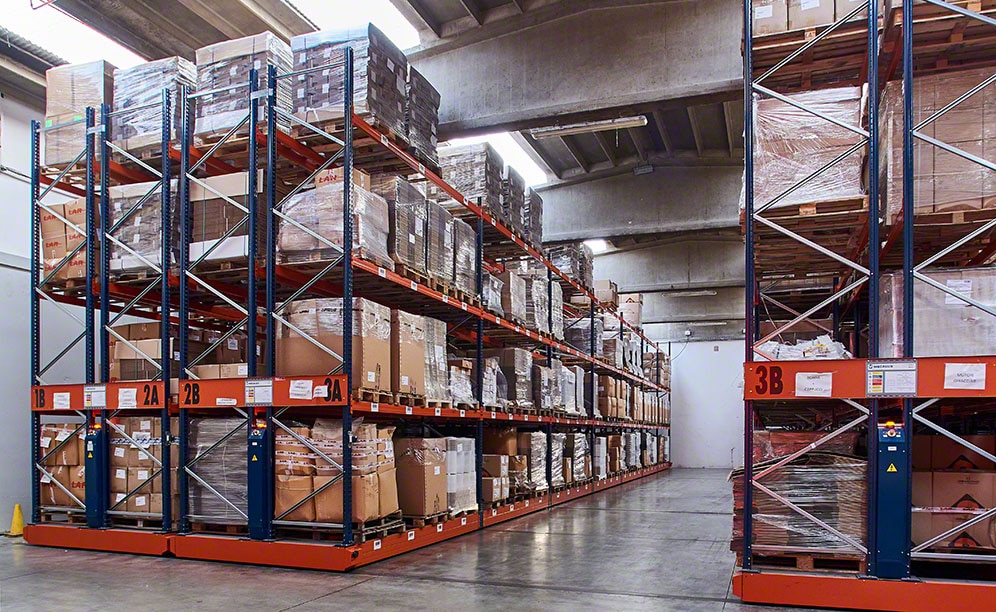
LAR's warehouse for thermoplastic resins in Campogalliano, Italy
Ask an expert