
IKEA Components automates its warehouse in Malacky without disrupting operations
IKEA Components modernizes its logistics operations with automated Mecalux systems, allowing a successful order picking rate of 99%.
IKEA Components, a company specializing in the packaging and delivery of furniture accessories and parts, has automated its warehouse in Malacky, Slovakia. Mecalux has installed trilateral stacker cranes and pallet conveyors in each of the 12 aisles of its warehouse, in addition to Easy WMS.
IKEA Components: packaging and delivery of furniture accessories
Founded in Sweden in 1943, IKEA started out as a small business devoted to selling furniture by catalog. Today, it is one of the world’s most recognized multinational companies, marketing contemporary furniture, home goods, and decorative items in 62 markets. IKEA Components, an IKEA subsidiary, is responsible for packaging and delivering accessories and components for furniture.
- Founded in: 1943
- International presence: 62 markets
- No. of stores: 460
CHALLENGES
|
SOLUTIONS
|
BENEFITS
|
---|
Automating a conventional warehouse without halting operations is a priority for companies and a challenge for storage system suppliers. IKEA Components, a business dedicated to packaging and distributing furniture accessories, needed to modernize its facility in Malacky, Slovakia, to remain competitive.
Frantisek Stora, Managing Director of IKEA Components Slovakia, says: “We had experience in warehouse automation but primarily in greenfield projects — started from scratch. With Mecalux’s help, we’ve transformed an existing facility, leveraging the building structure and the racks. The project was more challenging than others we’d done in the past. But now that it’s finished, I can confidently say that it’s been a complete success.”
Prior to its automation, the IKEA Components warehouse had 12 aisles of pallet racking managed by trilateral forklifts. As the production rate increased, the organization knew the time had come to invest in automated systems. “In the past, our priority was to automate our manufacturing processes. But a few years ago, we decided to overhaul our internal logistics operations as well,” says Stora.
IKEA Components’ warehouse automation project was carried out in four stages. It concluded with the installation of 12 stacker cranes and conveyors that connect the storage area with the input/output stations for goods arriving from production. Trilateral stacker cranes are ideal for automating conventional racking systems easily and economically, without changing their structure or stopping warehouse operations.
At the project’s halfway point, order picking tasks were eliminated because the company started receiving and distributing full pallets without the need to be broken down. This modification, tested using the Easy M software program, made it necessary to improve the facility’s organization and layout. Consequently, Mecalux changed the direction of operation of the stacker cranes and conveyors to move pallets to the dispatch zone automatically.
This logistics automation project has boosted the business’s efficiency: “With this automated solution, we now fulfill 99% of our orders on time and in full. Our aim is to supply IKEA with all the accessories required to manufacture its products. It’s extremely important for us to have solid internal logistics processes to meet our deadlines,” says Stora.
Easy M warehouse simulation software
During the second and third phases of the project, Mecalux used simulation software to create a virtual representation of all the elements inside the IKEA Components facility: the goods, storage systems, and handling equipment, among others.
This technology runs a number of tests to predict the warehouse performance. It checks, for example, whether the incorporation of new storage systems and logistics processes will affect productivity or whether bottlenecks could occur.
The simulation was done to verify that the design of the facility could absorb the flows required in Phases 1 and 2. These included storage and retrieval and pallet entries/exits to and from the conveyor lines. The simulation confirmed that the design of the warehouse and the stacker cranes were ready to perform the required cycles: 85 combined pallet movements/hour for Phase 2 and 125 combined movements for Phase 3.
At the end of the simulation, Easy M generated a report specifying all possible flows of movements in the IKEA Components facility, the workloads, and downtime. The analysis was supplemented by an animated 3D rendering of the entire designed warehouse, where the unit loads can be seen in motion.
Our main requirement was to design and equip the warehouse with automated systems. We used to manage our facility manually. Now that it’s automated, we no longer have to concern ourselves with pallet movements — the automatic equipment does this for us.
AS/RS connected to production
“Today, 90% of pallet locations are managed with trilateral stacker cranes. Automation allows us to cope with fluctuations in the number of orders. During the pandemic, the volume of activity rose and fell constantly, so automation helped us match our resources to the needs of the market. Thanks to automation, we’ve also optimized our logistics and operating costs,” says Stora.
The IKEA Components facility is made up of 12 aisles with 46-foot-tall racking on each side to accommodate the pallets from the manufacturing area. The automated storage and retrieval system (AS/RS), which stands out for its versatility, has been personalized to hold goods of five different heights.
The trilateral stacker cranes are designed to execute three types of movements: longitudinal (along the length of the aisle), vertical (to raise and lower the cradle containing the goods), and in depth (to insert and extract pallets from the racks).
Pavol Masarovič, Operations Manager at IKEA Components Slovakia, describes processes in the facility: “All the pallets in the AS/RS come from our production area via automated guided vehicles (AGVs). They arrive at the pallet checkpoint, which is connected directly to the warehouse by conveyor. At the checkpoint, the WMS designates an exact racking position in one of the 12 aisles to store each pallet. Subsequently, when the WMS creates a shipping order, the entire dispatch process is also carried out automatically until the pallet reaches the loading area.”
Advantages of trilateral stacker cranes
- Adaptability and easy implementation: the solution is adaptable to any warehouse with conventional racking served by trilateral forklifts.
- Increased productivity: stacker cranes can work 24/7 and greatly streamline operations by performing combined storage and retrieval cycles.
- Integration with other systems: trilateral stacker cranes can be integrated with other automatic handling equipment, e.g., conveyors, and with Easy WMS warehouse management software.
- Error reduction: automated pallet storage and retrieval eliminates errors resulting from manual product handling.
- Maximum space utilization: unlike other stacker crane models, trilateral stacker cranes can operate from ground level and do not require an upper guide rail.
- Safety: replacing forklifts with stacker cranes makes the facility safer and minimizes any risk arising from manual handling of goods.
Real-time component traceability
“With the warehouse management software, we can see our material flows and how much stock we have in the facility,” says Masarovič.
To control inventory in real time, the pallet checkpoints automatically read the label of each unit load moved from production by the AGVs. This is done to verify that the pallet corresponds to the one previously indicated by IKEA Components’ ERP system. At the pallet checkpoints, placed along the conveyor line, the dimensions and condition of the pallets are also checked to ensure they meet the requirements for storage.
To assign each pallet a location on the racks, the WMS makes a series of calculations. These take into account empty slots, the product’s SKU, and its demand level. As soon as the slotting strategy has been implemented, automation takes over. Conveyors and stacker cranes transport the pallets automatically to their corresponding locations. Once the goods are stored, the WMS controls their status in real time, tracking any movement made.
Commitment to Logistics 4.0
“Automation brings us flexibility, efficiency, and the storage capacity we need. Plus, the AS/RS gives us real-time inventory visibility,” says Masarovič.
IKEA Components has boosted its growth rate through technology, integrating manufacturing and logistics automatically. Thanks to the company's moved into Industry 4.0, it can control its processes more rigorously, provide more efficient service, and take on future challenges with autonomy.
Our relationship with Mecalux has always been very professional. We’d already worked together prior to this ambitious project. But after automating our facility, we could say we’re more impressed by Mecalux’s effectiveness — if that’s even possible.
Gallery
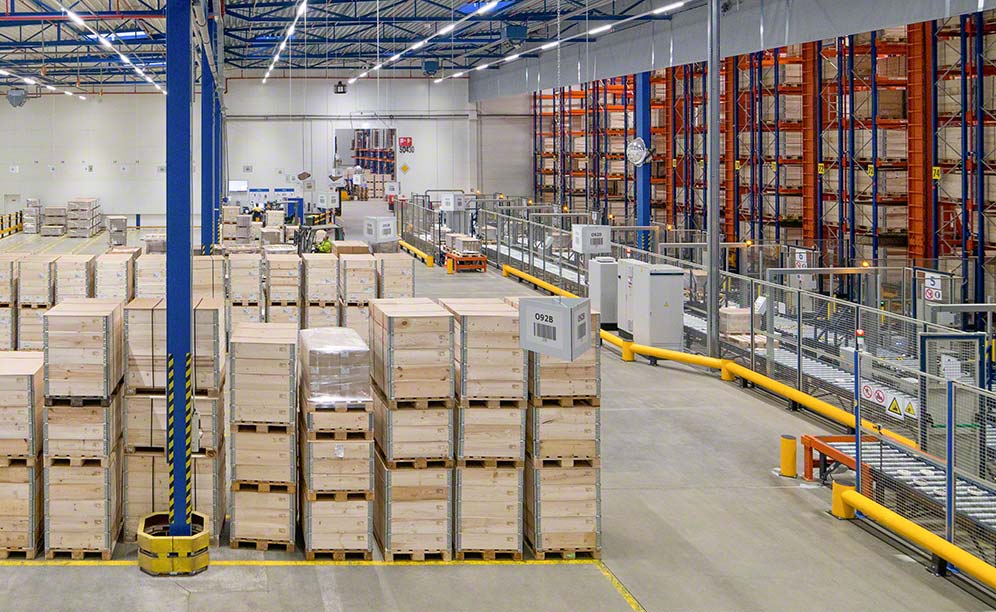
IKEA Components warehouse with trilateral stacker cranes in Malacky, Slovakia
Ask an expert