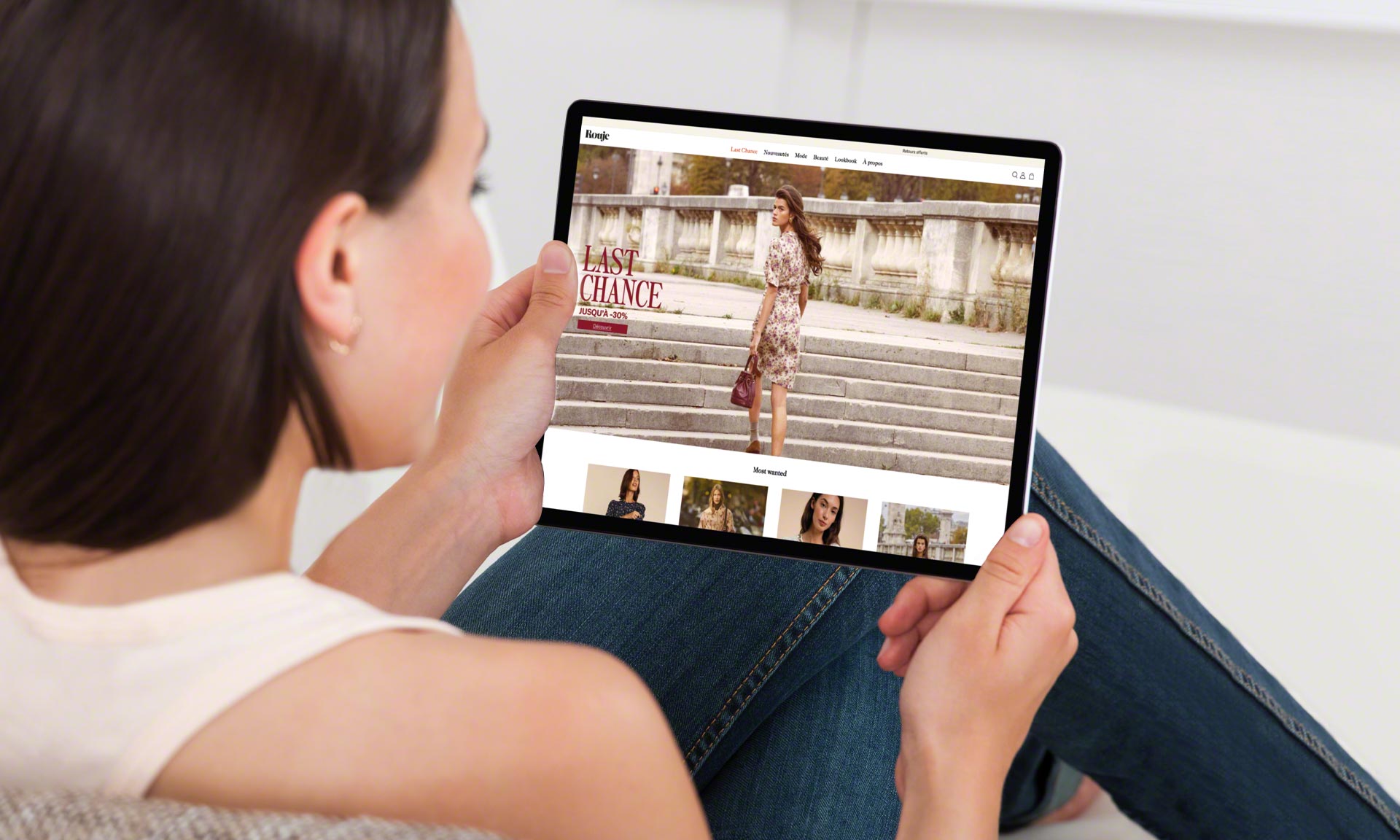
Fashion brand Rouje boosts productivity in its Paris warehouse
Feminine fashion brand Rouje streamlines and optimizes omnichannel order picking with Easy WMS.
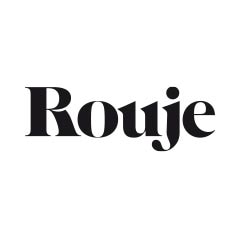
Fashion brand Rouje has digitalized its facility with Mecalux’s Easy WMS warehouse management software. The company has installed three additional Easy WMS modules: Supply Chain Analytics Software, Multi Carrier Shipping Software, and VAS.
Rouje: women designing for women
Rouje is a fashion brand created in 2016 by French influencer Jeanne Damas and Jérôme Basselier. Developed by and for women, the company features accessories to bring out each woman’s personal style. Rouje encourages women to express their femininity with complete freedom through thoughtfully curated prêt-à-porter collections and accessories.
- Founded in: 2016
- Presence: Europe and international
CHALLENGES
|
SOLUTIONS
|
BENEFITS
|
---|
Since it was founded in 2016, French women’s fashion retailer Rouje has created an aesthetic universe that has taken the world by storm, achieving significant international recognition.
So, how has a brand like Rouje managed to go so far? Through a distinctive style inspired by Jeanne Damas, meticulous and timeless design, the creation of a unique universe, and the marketing of a diverse range of beauty products, including makeup and cosmetics. Rouje is also strongly committed to environmentally friendly practices: since 2021, it has used recycled paper packaging to save over 2 tons of plastics a year.
Rouje’s supply chain contributes to its success. In the town of Palaiseau (just outside Paris), the company has an omnichannel warehouse. The facility distributes 300 orders a day — up to 900 in peak season — to online customers, physical Rouje stores, and stores-within-stores (small commercial spaces located within larger retail establishments).
To cope with such a high level of activity, Rouje launched a project to modernize and optimize its logistics operations. This began with the move to a larger facility to expand storage capacity. “Our former warehouse was becoming too small for our business. We’ve gone from a 9,688 ft² building to a 40,903 ft² facility,” says Marc Joly, Logistics Manager at Rouje. While most of the floor space is allocated to the storage of clothing and accessories, there is also an area reserved for fashion jewelry and beauty products.
Logistics processes designed for growth
When relocating to a new facility, Rouje decided to install Mecalux’s Easy WMS warehouse management software to monitor operations and product movements in real time.
“We’ve digitalized our logistics processes to support Rouje’s business expansion and bolster its rapid growth. We needed to be able to absorb high demand peaks in specific periods — during launches of new collections, for instance. But most importantly, it was essential to make order picking and shipping more reliable,” says Project Manager Caroline de Jaham.
The move to the new facility motivated the fashion brand to modernize all logistics processes in its supply chain. “Operations in our former warehouse — including goods management and order picking and shipping — weren’t 100% optimized,” says Joly.
“When we considered digitalizing our logistics processes, we contacted a consulting company for support, and they confirmed the need for us to install WMS software. Mecalux stood out as the perfect candidate to help us, being an expert in logistics with software tailored to our needs. We’re very happy because thanks to Easy WMS, our operations have improved. And this is just the beginning!” says Jaham.
Easy WMS has increased Rouje’s throughput. “Since we installed the Mecalux software, our productivity has gone up by 20%,” says Joly. The program distributes the work among the various employees who carry out logistics operations.
These workers use RF or wearable ring scanners to capture and read barcodes quickly and accurately. With this technology, the mobile terminals are attached to the operators’ finger and arm so that they can easily consult Easy WMS’s instructions.
Accurate, orderly goods receipts
Every day, the warehouse receives around 1,700 items from suppliers. “Before working with Easy WMS, our logistics processes were manual, so they were prone to a higher risk of mistakes,” says Joly.
Process digitalization has made operations simpler as well as safer. Operators scan each item for Easy WMS to log them all in the database. This enables Rouje to monitor product traceability more rigorously and know the exact location of its items in real time. The Mecalux WMS software applies advanced algorithms to facilitate a smart storage strategy. By organizing locations intelligently, Rouje makes the most of its warehouse space. In addition, replenishment is done automatically and at the appropriate time.
Proper product management has sped up storage and order picking tasks. Moreover, Easy WMS has made goods monitoring more reliable.
The Rouje facility also manages product returns. “Returns arrive in the morning. Easy WMS allows products to be restocked so that they’re available for sale again over the course of the day.”
Order picking for fast delivery
“With Easy WMS, we can process and dispatch orders quickly to ship them the same day. If it’s an order for the US placed before 2:00 p.m. French time, the customer will receive the product the next day due to the time difference. We begin order picking in the morning, and at the same time, the Multi Carrier Shipping Software module begins organizing dispatches,” says Joly.
Order picking is one of the most demanding operations in the Rouje warehouse. Operators pick all orders in batches, filling several orders at once. They travel around the facility using carts, where they place the items as they remove them from the shelves.
Easy WMS accompanies the pickers throughout the order picking process, eliminating any chance of error. “There’s no longer any confusion about which items to pick from the shelves. Before, the operators had to check whether they’d chosen the correct model, size, and color. With Easy WMS, this is no longer an issue, and errors are a thing of the past,” says Jaham.
Cosmetics and fashion jewelry are stored in a separate, restricted area of the facility. Orders that include these products are prepared the same as the others, i.e., by batch, but independently.
Once all merchandise for the orders has been grouped, it is separated in the consolidation zone. The product separation process has been simplified with the installation of picking shelves equipped with a put-to-light system. A light indicates which tote to place the goods in, with each tote corresponding to an order.
Before, operators had a printed list of the items they had to find in the warehouse. With Easy WMS, on the other hand, they merely follow instructions from the software, making them much faster. “We’ve cut our order picking times by 22%. Operators have gone from being able to fill around 70 orders a day to over 90,” says Joly.
Rouje has also optimized management of orders for its stores and stores-within-stores, slashing picking times in half through cross-docking. With this order processing practice, goods that arrive at the warehouse are distributed directly without having to be stored first.
Organized consolidation and shipping
Rouje’s merchandise is sold via several channels (website, brick-and-mortar stores, and stores-within-stores) and dispatched to many locations and countries.
As the customer experience is extremely important for the company, Rouje personalizes certain shipments. To control this process more strictly and avoid mistakes, the business has implemented Mecalux’s Value-Added Services (VAS) module. This extension of Easy WMS is integrated with the functionalities operators need to customize orders.
The VAS module sends operators instructions to ensure that each order is delivered correctly. For example, if an order should include a tote bag, during the packaging process, Easy WMS tells the operator to place it in the parcel.
Rouje has also installed the Multi Carrier Shipping Software module to generate shipping labels and communicate relevant information for customs documents.
In the shipping area, all processes managed with this module have a common goal: to distribute goods at the right time and in the agreed-upon conditions. “If, for some reason, one of the parcels couldn’t be dispatched, the module would set it aside to avoid interrupting delivery of the rest of the orders,” says Jaham.
Logistics operations under control
For Rouje, it was crucial to be able to analyze data such as the location, size, weight, and contents of the orders, among other information.
“Before digitalizing our warehouse, it was really difficult to analyze our logistics data,” says Joly. The company has also incorporated Mecalux’s Supply Chain Analytics Software module. This program provides valuable data on the main activities performed in the facility to improve decision-making.
At a glance, logistics managers can check different KPIs such as task processing time, available capacity, and orders shipped and received. “By knowing our picking productivity, we can predict the number of workers we need for warehouse operations and thus optimize our resources,” says Jaham.
Supply Chain Analytics Software provides numeric KPIs that show the throughput of a wide range of processes: goods receipt, storage, order picking, inventory control, shipping, delivery, transportation and returns management. “With Supply Chain Analytics Software’s data analysis, we’ve put in place measures to enhance and ensure the highest customer satisfaction,” says Jaham.
Digitalization for a thriving business
Mecalux’s Easy WMS software has been a game-changer in the Rouje warehouse: now, the fashion brand is ready to take its business to new heights while adapting to changing needs.
“With Easy WMS, we’ve overhauled all our logistics processes and fine-tuned day-to-day operations. This will enable us to support Rouje’s growth in addition to running new projects for the brand,” says Jaham.
Easy WMS has brought us many advantages: we’ve shortened our order picking times and now have more reliable control over our logistics processes. With detailed information on our operational performance, we can apply strategic measures to enhance and ensure the highest customer satisfaction.
Ask an expert