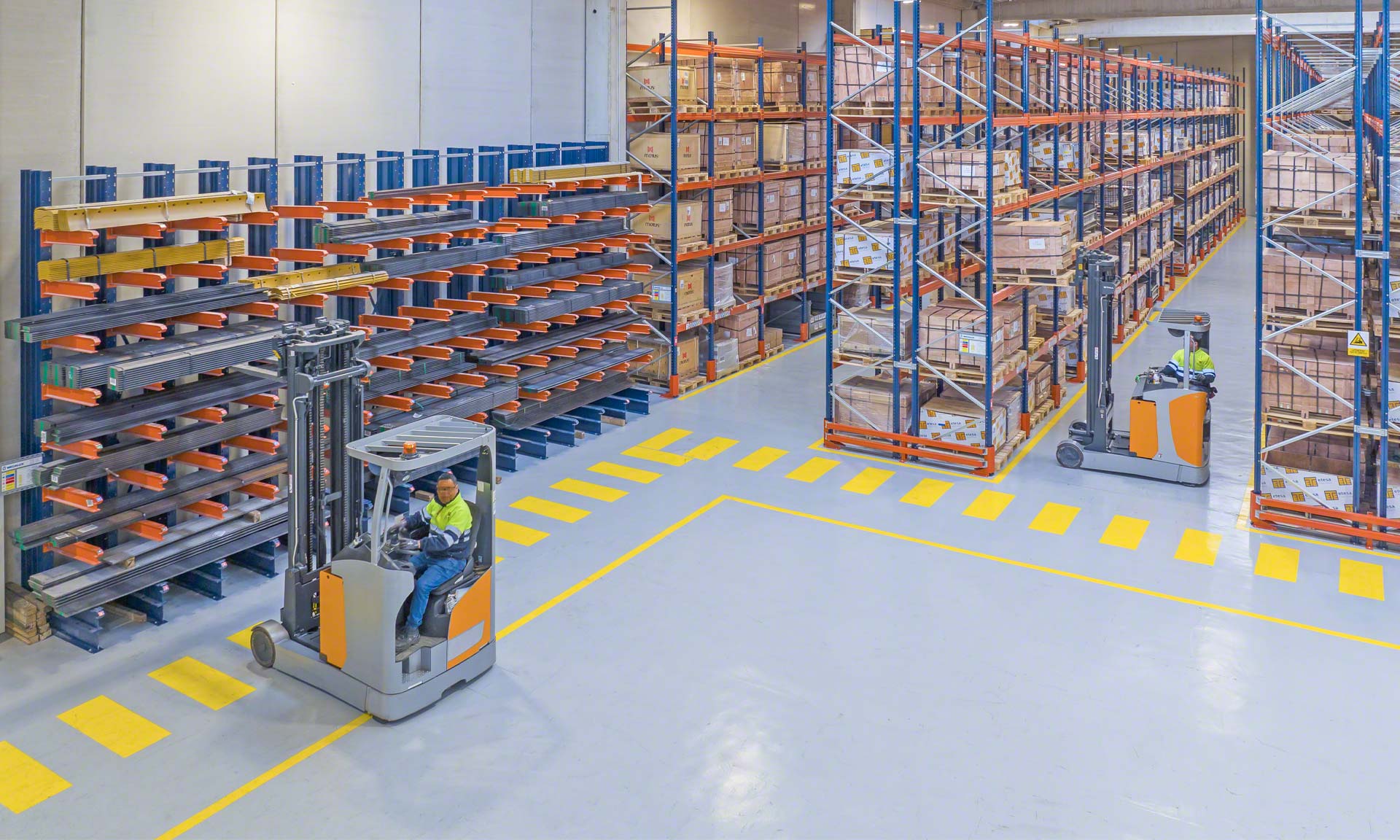
ETESA digitizes its warehouse management with Mecalux's Easy WMS
ETESA, a distributor of spare parts for public works machines, controls 2,000 SKUs with Easy WMS.
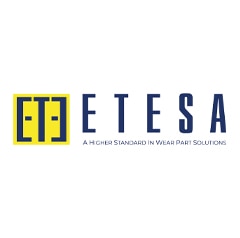
ETESA, a distributor of spare parts for public works machines, has digitized its warehouse near Madrid, Spain, with Easy WMS. The software controls all products and organizes operations to speed up the preparation and dispatch of all daily orders.
ETESA: more than 50 years of innovation
In business since 1968, ETESA is a Spanish company that distributes spare parts for earth-moving equipment employed in mining, public works, and construction. The spare parts are made from high quality steel — with an optimum ratio between hardness and toughness — for use in demanding working conditions.
- Founded in: 1968
- No. of employees: 16
CHALLENGES
|
SOLUTIONS
|
BENEFITS
|
---|
Change and transformation are part of ETESA’s makeup. The company began doing business in 1968 as a manufacturer of high-quality steel. In recent years, it has specialized in the sale of spare parts and anti-wear material for public works machines. The organization’s ability to adapt to new market requirements has driven its expansion: “In 2022, we’ve grown 15% more compared to last year,” says ETESA’s Juan Puertas.
To respond to market changes, ETESA’s supply chain has had to evolve constantly. One of the most recent business changes the company underwent was the opening of a 1-acre warehouse in Meco (near Madrid, Spain). “Our former distribution center didn’t have enough space for us to operate. We struggled to manage all our products — we even had to hire external logistics providers. The lack of capacity was limiting our future growth prospects,” says Puertas.
Additionally, in the previous facility, all operations were carried out manually. “We used our enterprise resource management (ERP) system and Excel files to track our merchandise and organize operations such as order fulfillment. It was a very primitive way of working,” says Puertas. The Sage 200c ERP system would monitor goods receipt and order dispatch operations. “Sometimes, the stock we had in the warehouse didn’t match what was recorded in the ERP. Consequently, we couldn’t prepare certain orders because we were short of those items,” says Puertas.
As the pace of work picked up, the company decided to implement a more sophisticated system capable of managing its logistics processes and boosting productivity in the facility. “We installed Easy WMS warehouse management software from Mecalux to eliminate any possibility of error in our operations and avoid stock imbalances. We also wanted to control our goods more accurately and gain traceability of our 2,000 SKUs in real time,” says Puertas.
Three storage systems
ETESA knew exactly what it was looking for: “When moving to this new facility, our priority was to obtain more storage capacity to house all our products of different sizes and turnovers,” says Puertas.
Before, the company had difficulty in organizing its goods, which had an impact on operational performance. “For example, operators would waste time preparing orders because they had to move a number of boxes before they found the ones they needed,” says Puertas.
The new ETESA warehouse is equipped with three Mecalux storage systems that facilitate the correct organization of the products: pallet racks, wide span shelving, and cantilever racks.
“The SKUs are sorted much better,” says Puertas. Large profiles, for example, are deposited on the cantilever racks, while small items are placed in the wide span shelving.
Housing each product in the right storage system gives the company another advantage: operators can locate the goods they need more easily.
Advanced warehouse management
Mecalux’s Easy WMS software program intervenes in all processes in the facility, from the receipt of products sent by suppliers to dispatches of orders to customers.
Easy WMS sends operators instructions via their RF scanners on how to perform their tasks. For instance, it shows them where to find the items they need and how many to remove from the locations. Following the software’s instructions step by step has brought ETESA numerous benefits: “Digitizing warehouse management has helped our operators become faster. We also make far fewer mistakes than we did in the past,” says Puertas.
The program monitors product movements in the facility and controls their status in real time. “Before, when supervising the goods manually, we had inventory discrepancies. There were times when we thought we had an item in stock, but when we needed it, we discovered that it wasn’t actually there,” says Puertas.
With Mecalux’s Easy WMS, ETESA has improved its inventory management. This operation consists of counting the products in the warehouse one by one to know the stock levels and identify mismatches. This program sends instructions to the operators on which items to locate, making the overall calculation more effective.
“It used to take us two weeks to do inventory. But with the software, we’ve cut that time in half,” says Puertas. Moreover, Easy WMS takes perpetual inventory: it knows the movements the products make in real time.
Order fulfillment is a key operation in the ETESA warehouse. Every day, operators process orders that are distributed worldwide. “Thanks to Easy WMS, we prepare and dispatch 25% more orders daily,” says Puertas. Proper organization of the goods results in more agile operations.
Workers are assigned to a specific work zone in the warehouse. As directed by the Mecalux software, pickers walk up and down the aisles, removing from the racks the items they need to fill orders. “Easy WMS is extremely user-friendly. Our operators have adapted well to the technology, and it’s improved the way they work,” says Puertas.
Ever-changing logistics landscape
ETESA’s logistics operations change continuously to adapt to market changes. Business expansion has led to an increased workload, which can only be managed through well-organized processes and tight stock control.
Mecalux’s Easy WMS is the cornerstone that fosters ETESA’s growth. The software ensures flexibility to adapt operations to new business demands. The program will support the company in any future project it undertakes.
By automating our warehouse management processes with Mecalux’s Easy WMS software, we make far fewer mistakes than we did in the past. Now, we prepare and ship 25% more orders a day and can access items more easily.
Gallery
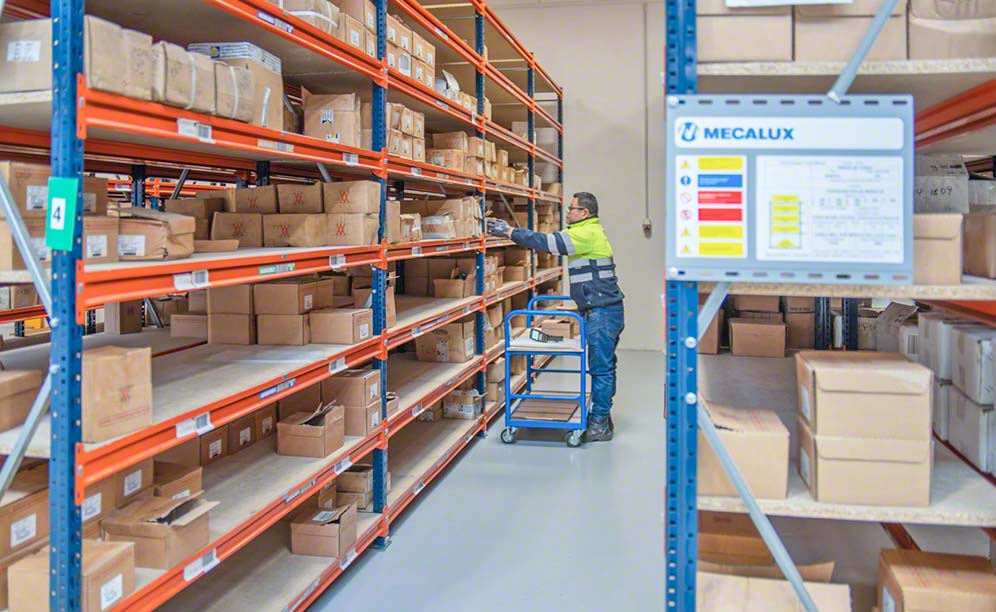
Warehouse of ETESA, a spare parts company for public works machines
Ask an expert