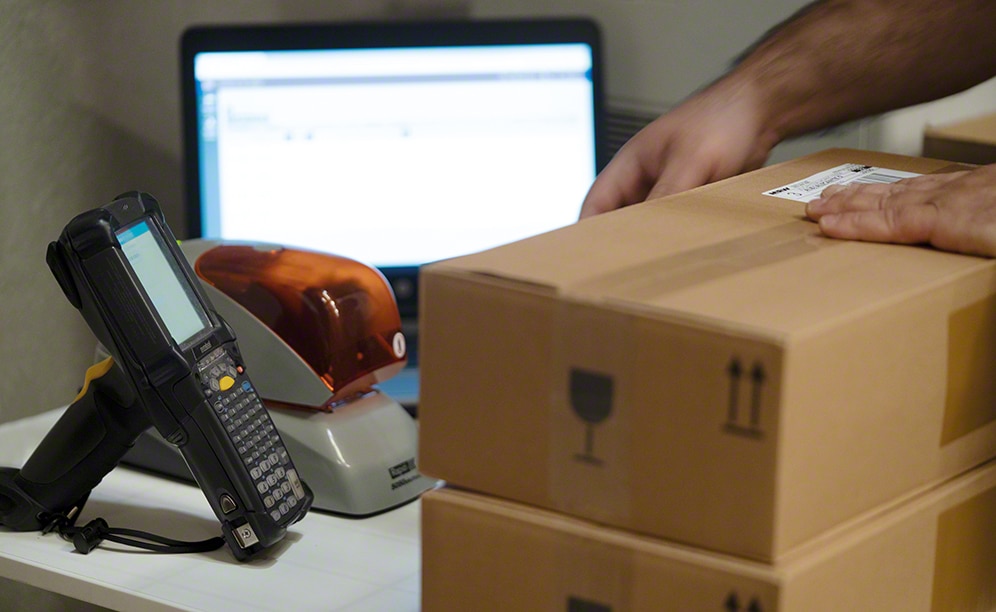
Danone’s warehouse for the infant and medical nutrition product line in Madrid
Danone’s warehouse for medical and infant nutritional products with the Mecalux Easy WMS management system
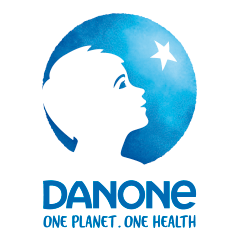
Danone’s distribution center in Valdemoro (Spain) must cope with a very high-paced daily work rhythm: managing between 500 and 600 SKUs and preparing up to 700 orders. It is an all-in-one omnichannel warehouse, i.e. orders are sent to retailers, wholesalers and customers who have purchased the products via the website. Mecalux has installed the Easy WMS warehouse management software, capable of controlling stock and optimizing pick tasks all to maximize the center's output and provide a more efficient service. It has also introduced two modules to enable Danone to control all its supply chain operations: Multi Carrier Shipping, which communicates with the shipping agencies that distribute online orders, and Supply Chain Analytics, used to analyze the data and achieve a more streamlined, modern and intelligent logistics.
A company with a global presence
Founded in 1919 and headquartered in Paris (France), Danone is a food and beverage multinational present in more than 130 countries on five continents. Through food and nutrition, the company strives to improve the well-being of people of all ages, regardless of their social or cultural background.
Danone has four distinct business lines: fresh dairy products, water, early life nutrition and advanced medical nutrition.
Omnichannel warehouse with speciality nutrition products
In operation since 1978, Danone has a 43,055 ft2 distribution center in Valdemoro (just 15.5 miles from Madrid) set aside to house specialized children’s and medical nutritional products. It is divided into three areas, each with different functions: a rack-supported warehouse with a trilateral forklift, a picking area and a zone for special and sensitive products.
According to Eduardo Puerto, Iberia Supply Chain Director at Danone, “Although it is not a very large warehouse, its operation is complex because we are involved in virtually all sales channels: we send products to retailers, wholesalers and customers who have bought products off our website.”
As an omnichannel warehouse, picking is one of the central operations. This work is very demanding because, every day, between 500 and 700 orders are processed, which then must be distributed as swiftly as possible. The warehouse is designed to help operators cope with this workload.
On top of that, between 500 and 600 different SKUs coexist in the same installation, including baby food and dietetic products to treat various diseases (Alzheimer’s, oncology, diabetes, cerebral palsy, epilepsy, etc.). Such products require meticulous monitoring and tracking throughout the logistics chain and must be stored in optimal conditions to preserve their properties and ensure they are adequately effective.
Danone needed the help of a warehouse management system (WMS) to organize and streamline movements to control such a large number of SKUs and supply all the sales channels in which it operates. “This tool had to be flexible enough to fit the ins and outs of our business,” points out Eduardo Puerto.
Intelligent warehouse with Easy WMS
Previously, Danone did not have an in-house WMS to manage operations. And, when it decided to deploy one, it got in touch with Mecalux. “We felt that the Easy WMS fit our budget and the turnaround time was reasonable. Moreover, the fact that Mecalux is a well-established, market-recognized company helped us to reach our decision,” mentions Eduardo Puerto.
Thanks to Interlake Mecalux’s Easy WMS, the company has improved its logistics and, in the words of Eduardo Puerto, “the change has been tremendous because it has given us a strict, controlled way of handling products and orders.” The WMS has a hand in all operations: goods reception, slot allocation, order prep and dispatch. In addition, it guarantees product tracking, from the moment they arrive at the warehouse until they are delivered to the customers.
The system has optimized product distribution and the goods are placed in the best location based on their turnover rate, expiration date and weight. “When we unload a truck, the WMS tells us where to locate each product. This allocation is designed to run with the minimum possible movements, something that we hadn’t even considered before,” admits Eduardo Puerto.
Another special feature and advantage of Easy WMS is the improved order picking and prep. Before this, each operator had his or her own criteria to get the job done. “Now, the system means we have very well-organized operations. Operators can prepare any order (for retailers, e-commerce, hospitals, etc.) because the WMS tells them how to do it in a very clear, accurate way. In this sense, we’ve hit the jackpot,” he notes.
Operators use radiofrequency devices to communicate with the WMS in real-time. These handheld devices receive orders and operators use them to confirm which orders are completed. It is a very swift system that facilitates the work of the operators and, as a result, warehouse performance is much higher.
A cloud-based, SaaS (Software as a Service) version of Easy WMS has been deployed. Unlike the On-premise modality, SaaS is based on a dynamic high-performance server infrastructure in the cloud, which always ensures optimal behavior adapted to the volume of business operations.
In the Danone roll out, the WMS has three different environments:
- Production: the environment used for day-to-day warehouse work.
- Test: here, WMS enhancements and new functionalities are tested before being implemented.
- Backup: it involves copying all the information managed by Easy WMS to make sure that the information can be reloaded if an incident occurs.
Eduardo Puerto - Iberia Supply Chain Director at Danone
“Mecalux’s Easy WMS is a flexible tool, set up to absorb our workload. Now that it’s up and running and fully adapted to operations, we’re starting to reap the benefits of the system.”
Strict control of goods
Identifying each product from the moment it arrives at the warehouse is the key to solid product tracking. For this reason, the receipt of goods is a fundamental operation when it comes to guaranteeing a smooth running logistics chain for Danone.
Every day, the warehouse receives 165 pallets from the different plants that the company has spread throughout Europe. For this reason, a large area has been set up right in front of the loading docks where operators log each item using handheld radio frequency devices.
There are two types of receptions:
- Planned. Danone’s SAP ERP notifies Easy WMS when goods arrive at the warehouse. Once received, operators verify that no error has occurred.
- Unplanned. Some of the SKUs (mainly consumer products) arrive at the warehouse without prior notification from the ERP. Operators then identify them one by one and feed them into the system.
When receptions have taken place, the operators store the goods according to the WMS’s instructions. “Distribution is based on rotation. The products with the highest demand are placed directly in the picking area, while the others will be placed on the racks managed by a trilateral forklift. This decision was made because that area is less accessible despite offering more capacity,” says Eduardo Puerto.
Easy WMS has all products pin pointed and knows their stock status in real-time. From this information, one can make any necessary decision when it comes to improving processes. One of Danone’s plants may, for whatever reason, decide to quarantine part of its production, i.e. request that certain products not be distributed to its customers. If the Valdemoro warehouse has some of these products, Easy WMS blocks and prevents them from being distributed until it receives the go-ahead.
How to prepare 500 to 700 orders per day
The warehouse operators prepare a high number of orders for all its customers: retailers, wholesalers, online shoppers, etc. To do so, a well-organized work approach is essential.
Easy WMS has optimized picking in different ways. First, it instructs operators at every turn, telling them which products to collect from the shelves and in what quantity. The system also designs a pick route, which optimizes operator collection rounds. Plus, not only is the operators’ work important, but also having the right goods available at all times. The WMS is permanently synchronized with the ERP to prevent stockouts.
Once the list of pending orders has been received, the WMS calculates the number of boxes that make up each order and generates a label for each of them. An order may consist of one, two, three or as many boxes as necessary and, in turn, each box includes a limited number of products. Identifying them ahead of time helps plan work for the pickers. Furthermore, the order can be checked for completeness with this system.“The software also allows us to prioritize and follow a coherent structure when preparing orders,” adds Eduardo Puerto.
Some customers, especially hospitals and pharmacies, require an order to bear a very detailed blue label from the Ministry of Health specifying the products’ composition. In these cases, Easy WMS orders these labels to be printed so that they can be put on the corresponding boxes. Overseeing the WMS is vital to running this work efficiently and quickly.
Only a select number of properly trained operators can access the special and sensitive products area. The WMS sends orders directly to these workers who go to the in-warehouse area where these products are stored to assemble the orders that require these items.
Multi Carrier Shipping: solution for e-commerce orders
“We have an e-commerce product line and each day we put together around 150 orders bought through our website,” explains Eduardo Puerto. The company has the Multi Carrier Shipping, a module developed by Mecalux, which allows the WMS to communicate with MRW, the carrier agency that distributes these orders.
Thanks to the Multi Carrier Shipping Software module, Easy WMS communicates with the shipping agency automatically to:
- Control the number of packages. The carrier knows in advance the number of boxes that are in the shipment.
- Print labels for the carrier. The system generates and prints the labels required by the forwarding agent.
- Confirmation of the tracking number. The WMS generates and verifies the shipment’s tracking code.
Operations are straightforward. According to Eduardo Puerto, “when MRW arrives at the warehouse, its carriers only must pick up ready orders, because they have all the information in their system automatically. Efficiency has been our big win in this case.”
Supply Chain Analytics: the power of data
Mecalux has deployed the Supply Chain Analytics module, which is used to consult and analyze all the data generated by Easy WMS. Danone manages a huge volume of information, such as product characteristics, types of orders, number of orders prepared per day or the customers it supplies.
Another feature of this center is that it uses rented pallets, so the company tracks all their movements (for example, how long they have been stored or where these pallets have been shipped). Easy WMS can report the status of each pallet at any time, since each pallet is identified. “We must report huge amounts of information every day and, for that, we need easy access to those data,” explains Eduardo Puerto. Supply Chain Analytics converts the data into useful information to interpret what happens in the warehouse, make strategic decisions for improvement and anticipate any sort of incident.
This system contains comparative control panels and comparative graphics with clear information about warehouse operations. Panels contain most functionalities that must be considered in a warehouse: incoming goods, warehousing, order preparation and dispatch.
Continuous process improvement
Thanks to Easy WMS, Danone’s warehouse in Madrid is ready to face the omnichannel challenge. It is an indispensable tool to simplify and speed up the processing of a large volume of daily orders.
“Now that the software is well-established in our warehouse, the next step will be for us to leverage all this information and apply logic to reshape processes and make them more efficient,” states Eduardo Puerto. The WMS’s roll-out will help Danone integrate a flexible, responsive and capable supply chain that can adjust to changes and operate efficiently in today’s competitive marketplace.
Advantages for Danone
- Efficient warehouse management: Danone has a complex distribution center, where it handles between 500 and 600 SKUs and up to 700 daily orders. Easy WMS directs all operations to achieve maximum efficiency and minimize errors.
- Omnichannel warehouse: Easy WMS of Mecalux simplifies order preparation for all channels: wholesalers, retailers, e-commerce customers, etc.
- Flexible supply chain: when analyzing data, Danone can react quickly to fluid situations, which is a competitive advantage.
Omnichannel warehouse | |
---|---|
Storage capacity: | 4,200 pallets |
No. of SKUs: | 500 - 600 |
No. orders/day: | 500 - 700 |
Management software: | Easy WMS, Multi Carrier Shipping and Supply Chain Analytics |
Gallery
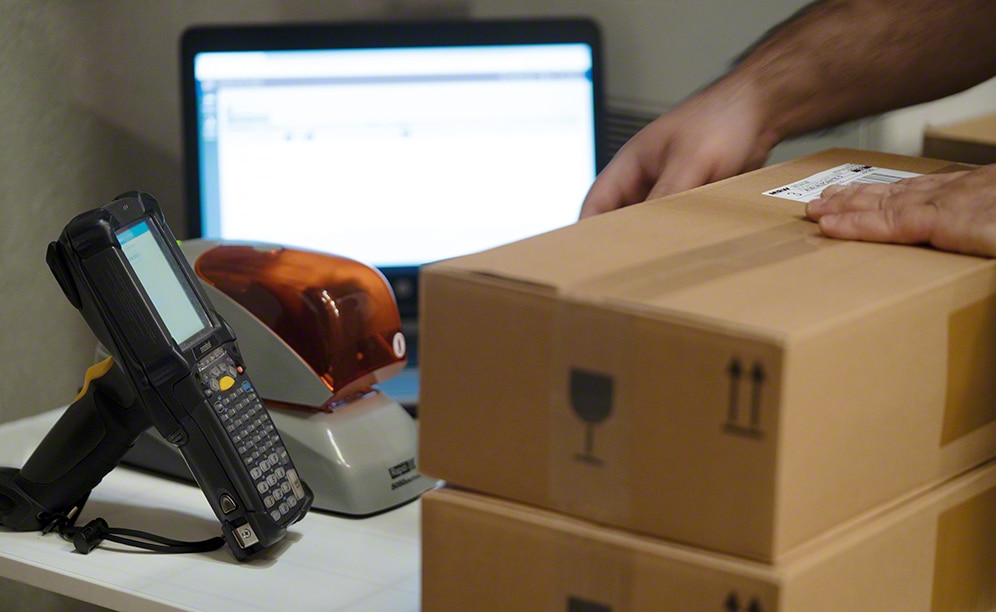
Easy WMS guides operators in preparing Danone’s orders
Ask an expert