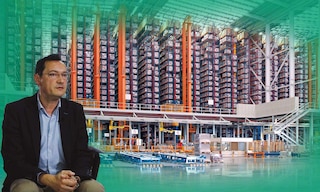
Interview w/Rafael Salinas, Head of Operations for International Subsidiaries, Porcelanosa Group
“Easy WMS is the digital brain of the five automated warehouses”
About Porcelanosa Group
Porcelanosa’s supply chain is synonymous with success. Located in Vila-real, Spain, the five logistics centers were built progressively over a period of 10 years and take up a large tract of land. Mecalux first set up the Porcelanosa AS/RS, followed by that of Xtone, the L’Antic and Noken warehouses, and, lastly, a second center for Porcelanosa. We spoke with Rafael Salinas, Head of Operations for International Subsidiaries of Porcelanosa Group, about how the company has benefited from the advantages of warehouse automation and increased productivity to meet the challenges of the global market.
Mecalux interviews Rafael Salinas, Porcelanosa Group's Head of Operations for International Subsidiaries, to explain how the company has automated its five logistics centers in Vila-real, Spain.
-
How would you describe the logistics operations of a ceramic floor and wall tile manufacturer such as Porcelanosa Group?
As a manufacturer of different components, i.e., ceramic tiles, kitchens, bathrooms, and faucets, we need our entire supply chain to be perfectly synchronized. This calls for all stakeholders to be organized in order to carry out just-in-time logistics operations in a VUCA (volatility, uncertainty, complexity, and ambiguity) environment. Additionally, taking into account the Group’s international expansion and the rise in orders in recent years, our supply chain has become more complex every year. Against this backdrop, automation and digitization are key for syncing our supply chain. With the automation of our logistics facilities and the automated connection with our production centers, we’re prepared to meet customer demand — even in the face of an increase in the number of orders.
-
Why was it necessary to build five automated warehouses?
At the start of the project, Porcelanosa Group’s production was diversified among five separate plants: the two Porcelanosa centers, L’Antic Colonial, Noken, and Xtone. For that reason, we commissioned five automated facilities in the Vila-real logistics complex, with a total capacity of over 275,000 pallets. When building the automated warehouses, our main aim was to be able to cope with the growth of the business, which translated into a substantial increase in the number of products managed and orders prepared. On a strictly logistics level, we had two objectives: to ensure that products were stored in the best possible conditions and to meet customer demand, in step with the upturn in sales and the seasonality of each market.
Easy WMS monitors stock to prepare thousands of orders a week without errors and to control the traceability of each product in real time
-
Turning to Porcelanosa Group’s day-to-day, what logistics challenges did you aim to meet with these warehouses?
We wanted to sync the activity in the production area with that in the logistics complex, since we manufacture over three shifts, 24 hours a day, and without human intervention. We also wanted to install storage systems that would enable us to reach the right capacity. In terms of order picking, we had the challenge of optimizing operating costs and boosting productivity by means of automated solutions that would help operators in handling heavy products. Efficient organization and the incorporation of automated equipment have provided us with the cycles we required, enabling us to perform picking optimally.
-
What role does warehouse management software play in organizing the different logistics operations?
The software makes it possible to correctly prepare orders containing any product at the right time The Mecalux warehouse management system is the digital brain of Porcelanosa Group’s five facilities. The software makes it possible to correctly prepare orders containing any product at the right time. It also monitors available stock to dispatch thousands of orders a week without errors and to control the traceability of each product in real time. For stock control, the software takes into account several logistics parameters, such as the model, characteristics, color, size, batch, and manufacture date of each item. Using these parameters, the management software establishes the necessary rules to automate the selection of products to be included in each order and not depend on the subjective decisions of warehouse staff. Another process that would be impossible to manage without the WMS is product packing and labeling. Digitization allows us to choose the best format to deliver the product in optimal conditions, without breakage or damage, in line with the needs of each customer and the type of transportation used to distribute the goods.
-
How does automation help Porcelanosa Group’s five warehouses work efficiently and safely?
Automation offers safe, continuous movements of products in the different AS/RS while facilitating the work of the operators. For example, the conveyor lines and stacker cranes ensure efficient order picking, delivering goods to the pick stations automatically. Automation minimizes operator movements, so these workers can dedicate more time to completing orders at their pick stations. These stations are outfitted with hydraulic systems adjustable to the height of the operators for better ergonomics. As a result, Porcelanosa Group’s productivity has risen significantly.
-
How have Porcelanosa Group’s logistics operations responded to the challenges seen in recent years, including the coronavirus pandemic?
During the Covid-19 pandemic, the automated warehouses enabled us to ensure uninterrupted service. The automatic handling equipment — i.e., stacker cranes and conveyors — continued to operate efficiently despite the lockdown and restrictive measures adopted. The Mecalux software also gave us real-time visibility of the status of our supply chain and allowed us to adapt operations to the health measures. For instance, thanks to the software, order picking and dispatch were organized in advance to guarantee social distancing for both operators and carriers.
-
What are Porcelanosa Group’s plans for the future?
We want to continue leading the growth and expansion of the Group at the international level. To do so, we have to constantly adapt our logistics activity to new market demands as well as to the needs of our customers in this VUCA environment. The future of Porcelanosa Group lies in continuing to drive innovation in our supply chain with cutting-edge technology solutions that give us the scalability we need.