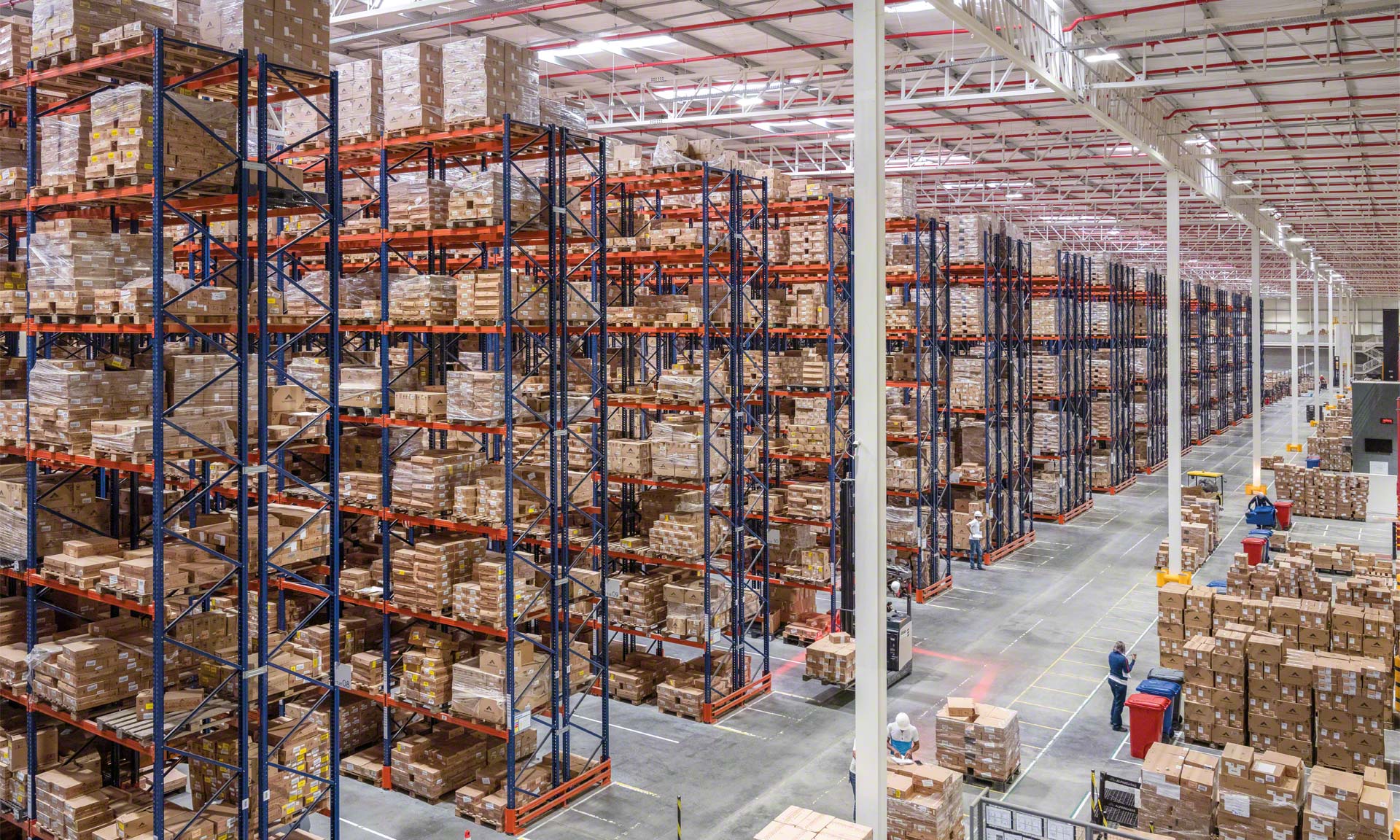
Footwear company Alpargatas equips 2 facilities in Brazil with Mecalux solutions
Alpargatas installs the semi-automated Pallet Shuttle to support production lines and pallet racks in supplying physical stores and points of sale.
Alpargatas, owner of the brand Havaianas, has outfitted 2 facilities in Brazil with 2 Mecalux storage solutions. The semi-automated Pallet Shuttle system connects production with the warehouse, while pallet racks facilitate order picking.
Alpargatas: more than 100 years of history
Alpargatas is a century-old Brazilian multinational company that owns renowned brands such as Havaianas, Rothy’s, and the technology company Ioasys. Present in over 130 countries, the business has become a global leader in the flip-flops industry. With a vertical supply chain, Alpargatas owns four manufacturing plants in Brazil where it produces quality merchandise in line with a strong commitment to the environment. Founded in 1907, Alpargatas is a company with a professional team of over 17,000 people and a presence in more than 130 countries.
CHALLENGES
|
SOLUTIONS
|
BENEFITS
|
---|
Alpargatas, the multinational owner of renowned sandal brand Havaianas, has modernized its supply chain to cope with expanding production and address growing market demand. At year-end 2022, the company recorded a 5.9% increase in sales. With a global footprint, its primary market continues to be Brazil. Last year, it grew by 9.2% in the country, accounting for a turnover of $490.6 million.
To satisfy the needs of the Brazilian market, Alpargatas has opened two logistics centers: a warehouse in the town of Santa Rita for goods used on the production lines and a distribution center (DC) in the city of Campina Grande to house and ship finished products. The footwear company has relied on Mecalux storage solutions to equip both facilities.
The Santa Rita warehouse is outfitted with the semi-automated Pallet Shuttle. This high-density logistics solution consists of a motorized shuttle that moves along rails inside the storage channels to insert and remove pallets. “We needed a storage system that would optimize the space for storing semi-finished goods before sending them to the assembly lines. Once the finished products are made, they’re stored temporarily in the manufacturing plants. Then, they’re shipped to a DC like the one in Campina Grande,” says Rodrigo Lakes, Logistics Manager of this Alpargatas facility.
The Campina Grande DC fulfills two basic functions in Alpargatas’ supply chain: “To consolidate and store all stock from the plants in northeastern Brazil and ship finished goods to brick-and-mortar stores and sales points across the country and abroad,” says Lakes. To facilitate product management in the DC, Mecalux has installed pallet racks. This versatile storage solution can hold pallets of distinct weights and volumes, with a wide variety of SKUs.
High-density storage in the manufacturing plant
“The main benefit we’ve seen with Mecalux’s semi-automated Pallet Shuttle system is the significant reduction in the floor space required to store all the products,” says Lakes.
High-density storage systems such as Mecalux’s Pallet Shuttle leverage the available surface area to accommodate a greater number of goods. In less than 3,230 ft2, Alpargatas can hold over 1,000 pallets on 36-foot-tall racks. Their channels have storage capacity for 10 pallets deep.
In addition to optimizing the existing space, the semi-automated Pallet Shuttle system boosts goods inflows and outflows via its motor-driven shuttle car. This vehicle moves inside the storage channels with full autonomy. “Every day, we store 150 pallets from different areas in the plant and remove another 150 from the racks to send them to the production lines,” says Lakes.
To insert goods, operators use a forklift to place the Pallet Shuttle car at the entrance to the assigned storage channel. The motorized vehicle then moves the pallet to the deepest available position. Once the load is stored, the device returns to the channel entrance to repeat the same process with the next pallet. In the Alpargatas warehouse, items are arranged according to the FIFO method. Short for first in, first out, this inventory organization strategy ensures perfect product turnover.
The motor-driven shuttle cars follow instructions sent by operators via a Wi-Fi-connected tablet. The software features a highly intuitive interface and an extensive array of options for performing goods-in/goods-out and maintenance operations. Additionally, the electric shuttle is equipped with multiple sensors and mechanisms to execute precise, fast pallet movements.
Sturdy, versatile system for the DC
Campina Grande is home to one of Alpargatas’ largest DCs in Brazil. The facility fills and distributes 1,500 orders a day and has a capacity for more than 34,000 pallets, each with a maximum weight of 1.1 tons. The company has centralized its logistics operations in this DC, which accommodates Havaianas sandals from its production centers. “Before, our merchandise was spread out among several warehouses and manufacturing plants,” says Lakes.
“When it came to putting this facility into operation, we knew exactly what we needed to do: expand storage capacity, streamline shipping, and distribute finished goods from our production centers in northeastern Brazil,” says Lakes.
Of the Pallet Shuttle’s multiple advantages, Lakes highlights “its impressive storage capacity.” Most of the racks installed are double-deep. That is, two racking units are attached to each other to eliminate working aisles and increase the usable storage space.
“Every day, we receive an average of 400 pallets with Havaianas sandals from the manufacturing plants,” says Lakes. The 36-foot-tall racks are ideal for handling this workload and simplifying order processing. Each location is always allocated to the same SKU, resulting in flawless stock control. On the lower levels of the racks, operators fill orders by picking products directly from pallets. The upper levels, on the other hand, house safety stock to ensure the availability of merchandise at any given time. Operators use reach trucks to load and unload pallets from their corresponding locations. To perform picking, they employ ground-level pickers.
With such lengthy storage aisles (413.5' long), higher-turnover products are positioned at the ends to expedite their entry and exit. Meanwhile, items with lower turnover rates are stored in somewhat more distant locations. Mecalux also set up interior passageways that cut crosswise through the racking to facilitate the flow of movements.
Alpargatas’ Campina Grande DC moves a considerable number of goods every day. To absorb this volume of activity, the facility is outfitted with 40 loading docks and a large staging area where pallets are temporarily stored on the floor. This zone carries out three key operations: receiving, shipping, and preloading of products. Accelerating these processes is crucial for maximizing efficiency in the company’s supply chain.
Two warehouses to meet diverse needs
In the Santa Rita manufacturing center, the Pallet Shuttle system optimizes the available space while boosting speed and throughput to support the rise in production. The pallet racks installed in the Campina Grande DC offer the storage capacity and agility required to ship 1,500 orders a day and supply physical stores and points of purchase with Havaianas flip-flops.
Alpargatas chose to partner with Mecalux to equip the two strategic facilities for its business with customized storage systems. Each solution responds to separate logistics needs but with a single objective: to optimize Alpargatas’ supply chain in Brazil.
We chose Mecalux to outfit our warehouse and DC because of its competitive pricing and the quality of its service.
Gallery
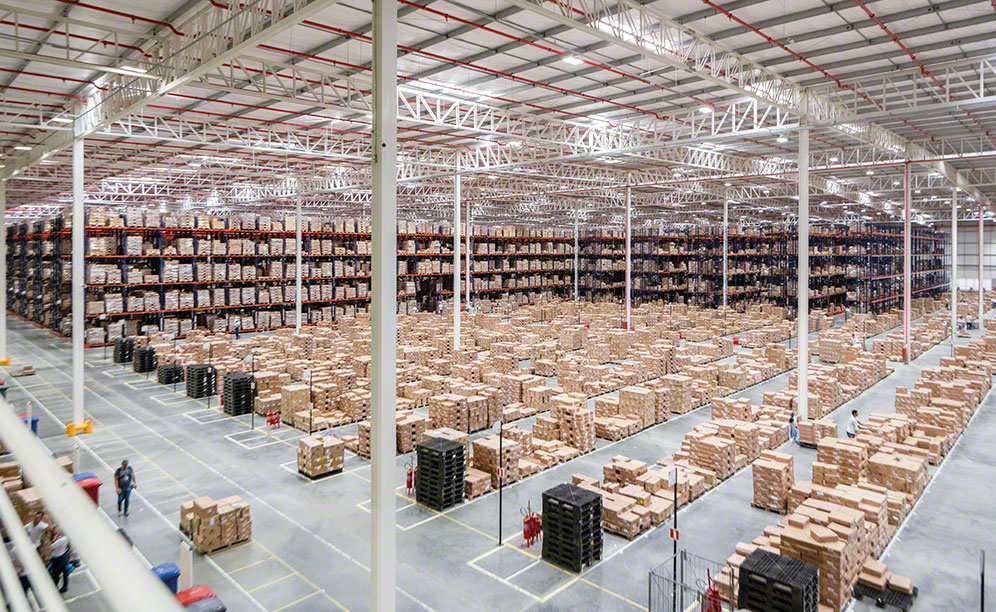
Alpargatas DC in Campina Grande with pallet racks
Ask an expert