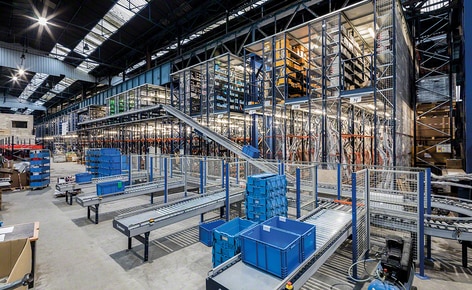
Automotive Parts Factory boosts e-commerce sales with a pick module and conveyor system
Conveyors accelerate the picking of the e-commerce operator Automotive Factory Parts
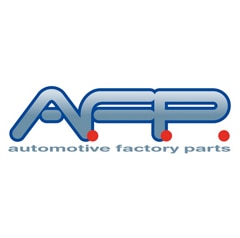
Automotive Factory Parts, an automobile spare parts distributor, owns a 1.24 acre modern logistics center in Gennevilliers (France), whose principal operation is the picking of online orders. Interlake Mecalux has provided the storage systems, including a circuit of conveyors that link all areas of the installation, so that picking is carried out faster.
The needs of Automotive Factory Parts
The French company sells an extensive catalog of spare parts for garages, gas stations and the automotive industry.
Faced with boosted sales, the enterprise required an expansion of its warehouse’s storage capacity, along with the implementation of a solution that would sort goods by market demand and size.
Automotive Factory Parts' goal is to provide competitive pricing on the best products and, to do this, it would need to keep running costs down.
Thanks to the collaboration with Interlake Mecalux, it has set up a quick picking system that helps provide excellent service to its online shoppers.
The solution
Interlake Mecalux analyzed Automotive Factory Parts' requirements at length and proposed the installation of manual hand-pick racks.
The racks are 20' high with walkways or raised aisles attached to them, making up a total of three floors. A conveyor circuit automatically moves finished orders to the completion and consolidation area.
Selective pallet racking
The sides of the warehouse are lined with pallet racks for over-sized products and palletized reserve stock for the picking shelves.
Picking shelves
The warehouse was sectored to organize the company's broad range of SKUs. Thus, maximum throughput is achieved in the installation, as well as streamlined picking.
Operators walk the aisles picking the products that comprise each order directly from the shelves. They follow the order grouping system, which consists of preparing several orders on the same trip.
Replenishment is carried out in off-peak hours, i.e., when there are fewer orders to prepare.
A mezzanine structure is installed in the central aisle area. The upper floor is where the conveyor circuit is located, with more racks on the lower level.
Ground floor
The logistics center racks are highly accessible, fostering the handling of goods. Moreover, they are very adaptable, since there are add-ons and accessories to deposit all the different sized products (from over-sized ones, down to the smallest items).
The aisles are wide enough so operators move about with handcarts, picking and replenishing products. To facilitate their movements, a cross-aisle passageway was opened up that runs front to back in the block of racks.
Upper floor
An empty, wide open mezzanine above the racks can be fitted with more racks down the road, taking into account the needs and growth of Automotive Factory Parts.
Conveyor circuit
It links the three floors and runs to the consolidation area, where orders coming from different warehouse areas are sorted and prepared.
This solution lessens the movements of operators since they are not running all over the warehouse to select the products for each order, but only work in the area assigned to them.
Consolidation area
Once on the bottom floor, the boxes are sorted into four channels. Next, orders are distributed in handcarts, as per the order they belong to, and taken to where they are validated, packaged, labeled and issued the required shipping documents.
Finished orders are sent to three different destinations:
- Mass delivery. Products are grouped on pallets and transported to delivery vehicles.
- Individual packages.
- Sales counter and direct pickup.
Galileo from Interlake Mecalux
The warehouse management system (WMS) at Automotive Factory Parts is in constant communication with the Interlake Mecalux Galileo control module.
This software is tasked with giving movement orders to the conveyor circuit and sending boxes to the corresponding warehouse areas.
Advantages for Automotive Factory Parts
- Operational flexibility: the warehouse layout offers flexibility when picking orders. Each floor has a specific number of operators, which may vary depending on the demand.
- Optimal goods management: racks offer direct access to the goods, and at the same time are equipped to classify products according to their size and characteristics.
- Rapid picking system: the automatic conveyor circuit joins the different warehouse zones and streamlines picking, since operators do not have to crisscross the installation to pick up the appropriate products.
The Automotive Factory Parts warehouse | |
---|---|
Storage systems: | Selective pallet racking |
Storage systems: | Racks with walkways |
Storage systems: | Mezzanin |
Storage systems: | Automatic conveyor circuit |
Gallery
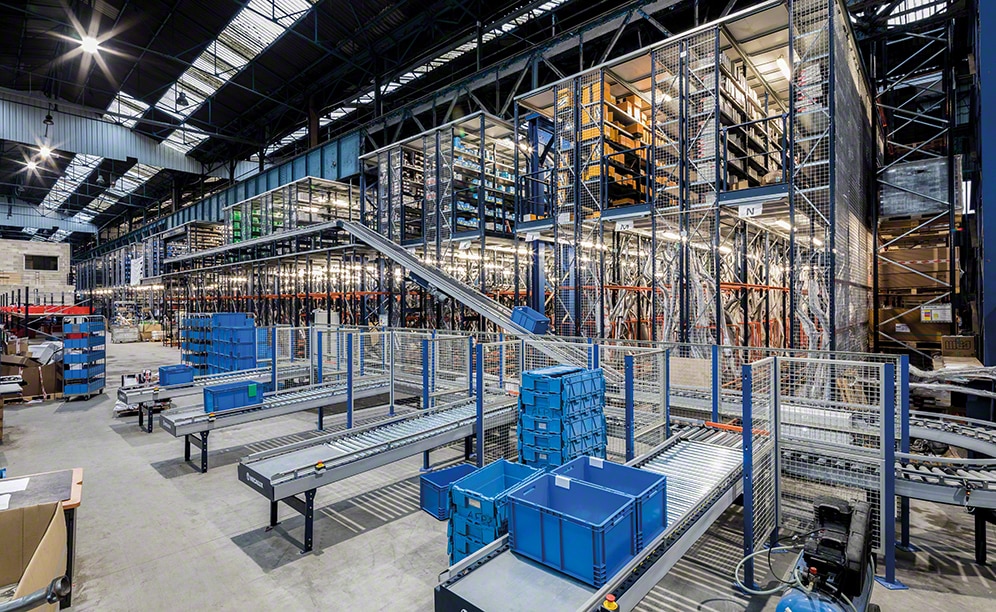
Mecalux has provided the storage systems, including a circuit of conveyors that link all areas of the installation, so that picking is carried out faster
Ask an expert