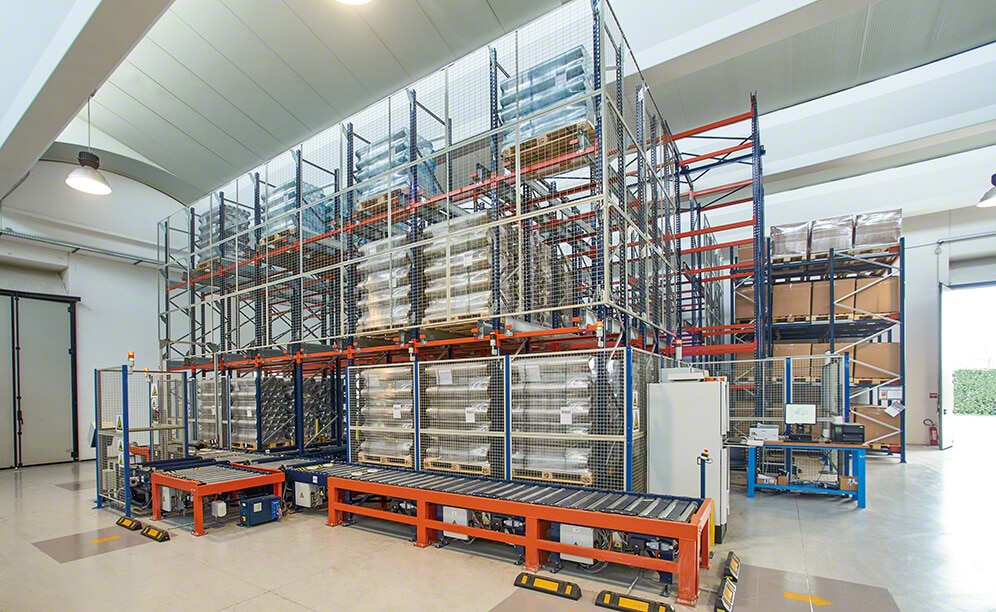
VI-MA automates its components warehouse for metal containers in Italy
VI-MA stores components for metal containers in the Pallet Shuttle system with stacker crane
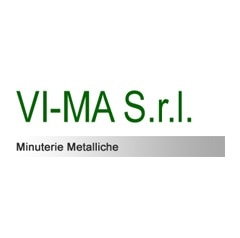
With the inauguration of a new automated warehouse in Miradolo Terme (Italy), VI-MA, a manufacturer of metal container components, has streamlined its logistics to reinforce its business expansion. Interlake Mecalux has equipped it with the Pallet Shuttle system operated by a stacker crane and the Easy WMS warehouse management software (WMS). This installation stands out for its capacity, agility and flexibility.
Success runs in the family
With more than 25 years of experience manufacturing cans, in 1986, Mario Angelo Vitaloni knew it was time to build his own business and one he named after himself, with an acronym: VI-MA.
Located in the town of Miradolo Terme (northern Italy), VI-MA is a family business that manufactures components for metal containers (bases, rings and lids) used in all sorts of industrial sectors, although more specifically by food companies.
VI-MA’s new warehouse
Continuous market developments and new customer demands have driven VI-MA’s investments. “We are a company on the up and up. I have no doubt that growth is what lays ahead for us,” explains Marco Vitaloni, company owner. In response to increasing demand, it recently unveiled a 25,887 ft2 warehouse where it stocks finished products ready to be shipped to in-country clientele.
In the past, the company lacked a dedicated storage space, so it grouped pallets on the floor. This made management tougher and increased the likelihood of errors being made. It was clear: the company needed a warehouse.
The manufacturing center is located right next to the new warehouse. The operators, running counterbalanced forklifts, collect the pallets from the manufacturing lines and transfer them directly to the warehouse.
“We wanted to expand storage capacity and store as much merchandise as possible in a tight space,” says Marco Vitaloni. So, VI-MA got in touch with Interlake Mecalux to get the ball rolling. “Interlake Mecalux recommended its racks because of their quality. After working with Interlake Mecalux, we noted its professionalism and speed in finding an efficient way to meet our needs,” he adds.
Interlake Mecalux suggested the installation of a compact storage system. Solutions of this type optimize the entire surface area of an installation to accommodate a larger number of pallets. It decided to take a step further and automate its warehouse. To do so, the Pallet Shuttle system was installed attended by a stacker crane as this guarantees a high flow of movements with minimum operator involvement.
“The AS/RS was commissioned on schedule and without any operational downtime. So, we were able to continue to serve our customers throughout the process,” points out Marco Vitaloni.
The warehouse has a single aisle where a stacker crane operates with the Pallet Shuttle system. On either side of the aisle are 21.3' high racks comprising channels able to hold between six and seven pallets deep.
A block of push-back racks also acts as a buffer, , i.e., for pallets that are immediately distributed, without needing to be placed in the AS/RS.
These racks measure 21.3' high and are made up of a series of channels on a slight inclination to harness gravity. The front (facing the aisle) is lower in height so that, by removing a pallet, the rest of the products move forward a position. As a solution, it provides excellent flexibility when handling goods, because forklifts insert and remove the pallets from the channel entry points without driving into the lanes.
Automation advantages
Although VI-MA chose the automatic Pallet Shuttle system for many reasons, it was mainly driven by the fast entry and exit of goods. There is room for 356 pallets, which can be stored for as long as needed, as their extraction process is very quick when they are required.
“We wanted to innovate our processes and, so, it was very clear to us that automating our logistics was the way to go,” explains Marco Vitaloni. Automation leads to error elimination and, as a result, a better end customer experience.
It also reduces goods receipt and shipping times. The stacker crane, which moves at a travel speed of 459 ft/min and 164 ft/min when raised, positions the shuttle in the assigned channel. Once there, the Pallet Shuttle enters the inside of the racks to insert or remove the pallets.
Vitaloni Marco - Owner of VI-MA
“We opted for the Pallet Shuttle system with stacker crane because of the large storage capacity it offers us in the limited space we have. Operative automation has also cut costs and delivered a quick return on investment.”
More efficient management
VI-MA has also rolled out the Interlake Mecalux Easy WMS warehouse management system (WMS) to control the inventory on an ongoing, efficient basis. This system coordinates and directs in-house operations: reception (identifying and validating the goods), storage and dispatch.
Before the WMS was available, goods were not kept track of, besides what the operators and production manager could get done manually. Easy WMS has made up for this shortfall and delivered many advantages: better space usage, fewer errors, prevention of stock outs and overstocking, etc.
Easy WMS communicates with this company’s SIA ERP through XML files. The two systems exchange information and data on the warehouse’s status and business needs.
The WMS must identify each product as soon as it arrives at the warehouse so it can get involved in all warehouse operations. Pallets have a barcode label that is scanned at the inbound inspection point. There, the pallet is verified as the one previously notified by the ERP, as well as its measurements and condition. Easy WMS then assigns each a location bearing their characteristics and demand level in mind.
The company carries pallets with three different heights (41", 59" and 67"). Thus, rack locations have been adapted to these measurements. Easy WMS prioritizes pallet sizes when assigning space to each pallet. Thus, for example, taller pallets are deposited in higher locations, preventing smaller ones from being placed there.
Once the pallets are stored, the WMS can check the status of all storage locations in real-time and continuously report to VI-MA's ERP. Making any sort of decision is easier with this information on hand. When shipping out pallets, the system prioritizes the manufacturing date and selects those that were made first.
Since operations are fully-automated, Interlake Mecalux also set up the Galileo control software. This system instructs the warehouse’s electromechanical equipment (stacker crane, conveyors and Pallet Shuttle) and controls the safety measures.
Advantages for VI-MA
- Space optimization: the warehouse makes the most of all available space and provides the capacity to store 356 pallets with a maximum 1,653 lb unit weight.
- Automatic operations: the company wanted to automate the input and output of the goods to streamline workflows and minimize any potential errors.
- Business-ready WMS: Easy WMS is integrated with VI-MA’s ERP, controls its stock in real-time and has optimized the physical warehousing space.
Automated warehouse of VI-MA | |
---|---|
Storage capacity: | 356 pallets |
Pallet sizes: | 39" x 48" x 41" / 59" / 67" |
Max. pallet weight: | 1,653 lb |
Rack height: | 21.3' |
Rack length: | 38' |
Rack depth: | 17.4' and 20' |
Gallery

VI-MA’s warehouse for metal container components in Italy
Ask an expert