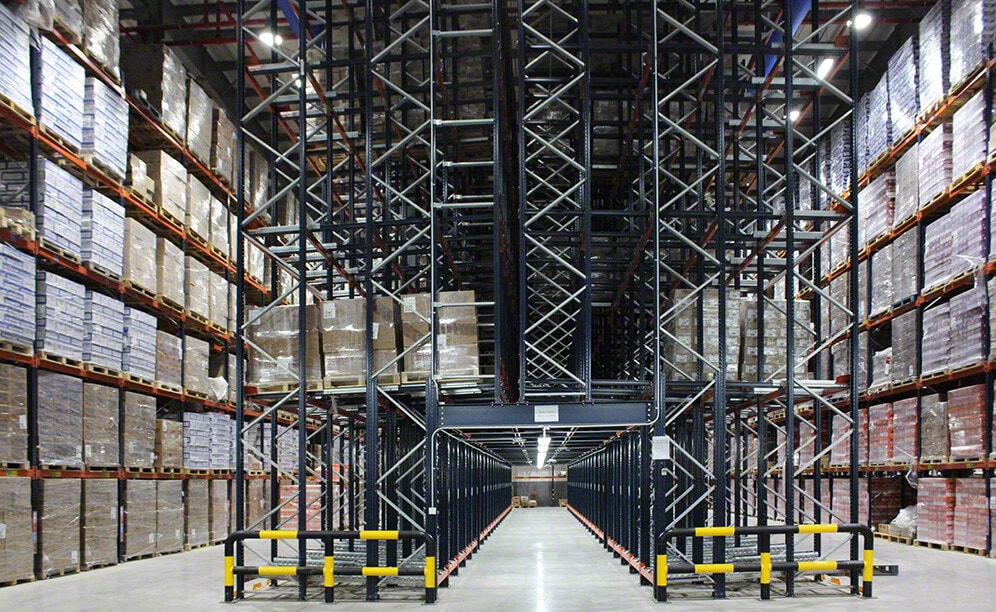
Combination of solutions for logistics operator Tamer in Saudi Arabia
The warehouse comprises multiple solutions to manage more than 200 SKUs
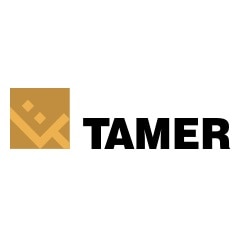
Interlake Mecalux has equipped an 8.05 acre warehouse, in collaboration with Alshaya, for Tamer which is a logistics operator in Jeddah (Saudi Arabia). The project includes selective pallet racks, the high-density Pallet Shuttle system, push-back racks and an underpass set up for picking from flow channels. Overall, the systems yield a 22,706-pallet storage capacity. This warehouse comprises multiple solutions to manage more than 200 different SKUs, to facilitate 700 inflowing pallets per day and to streamline order picking of around 440 orders/day.
About Tamer
Founded in 1922, Tamer is one of the biggest logistics operators in Saudi Arabia. It works for customers in the health care, beauty and consumer goods manufacturing sectors.
Tamer’s business activity consists of importing, storing and distributing products. Additionally, it designs marketing and promo campaigns for customers. Besides doing business in Saudi Arabia, it is able to distribute products in other countries thanks to agreements and collaborations with international logistics operators.
More than 200 SKUs in 8.05 acres
The company keeps growing and, as time goes by, it has become the first choice for many companies that require logistics services in Saudi Arabia.
Tamer’s key to success has been investing in storage. It was self-evident to the company’s directors that the business would have to improve its storage and distribution processes at a steady pace to meet its customers’ demands.
Dealing with its expanding business is a priority. So, the company just commissioned a new 8.05 acre logistics center meant to house its customers’ products (mainly, perishable consumer goods).
Tamer had to install a storage system to make the most of this surface area, one that would provide good space purposing to obtain a higher overall capacity. According to Samer Sabri, executive manager at Tamer, “Our top priority was to have a well-designed warehouse, one ready to manage the more than 200 SKUs we work with and one that would let us distribute 440 orders a day.”
One of the major difficulties this logistics operator runs into is how to store multiple products from different customers, each with different sizes, features and demand levels. In light of this situation, Interlake Mecalux, in conjunction with Alshaya, proposed the installation of four storage systems and that each system be allocated to certain SKUs and/or to specific operations:
- Selective pallet racks
- High-density Pallet Shuttle system
- Push-back racks
- Pallet flow channels
“We assessed the user-friendliness of these solutions when it came to handling products in our facility”, explained the executive manager. Streamlined management of the merchandise is vital in order to handle 700 incoming pallets from customers located at different points in Saudi Arabia and, likewise, the dispatch of another 800 pallets. Tamer’s four storage solutions offer the capacity to hold more than 22,706 pallets.
Selective pallet racks
Single and double-deep racks were installed throughout almost the entire warehouse. They measure 33' high, divided into six levels, and allowing storage space for 13,980 pallets.
They provide direct access to products, which equates to faster merchandise management, as well as quicker insertion and extraction of pallets from their locations.
The double-depth racks feature two pallets of the same SKU in each location (one behind the other). Here is where top rotation products are housed, such as higher demand food goods and those with upcoming expiration dates.
Pallet Shuttle system
The warehouse includes four blocks of racks with the semi-automatic Pallet Shuttle system. The blocks are 36' high, with five shelf levels each, and run 46' long in channels where up to 13 pallets are slotted. This system eliminates the number of aisles, making full use of available space to equip the company with a 6,350-pallet capacity.
An aisle lines each side of each block of racks. The goods can be managed as per the FIFO principle (i.e., insert the pallets through one aisle and extract them from the opposite aisle) or the LIFO method (insert and extract pallets from the same aisle), depending on Tamer’s logistical requirements.
“With this solution, not only have we gotten more spots to store our goods, but we also run faster overall operations, since workers do not need to enter storage lanes with a forklift,” points out Samer Sabri.
Among high-density systems, the Pallet Shuttle is the one that yields more speed in organizing loads. Workers deposit the Pallet Shuttle in the corresponding channel. Soon afterward, they insert the goods into the first position in the channel and the motorized shuttle takes the items directly up to the first open location it finds inside the channel.
Initially, Interlake Mecalux supplied Tamer with a total of five Pallet Shuttles. Later on, this figure jumped to 12 shuttle units. The company has multiplied its pallet movements by having more shuttles in service.
Picking solutions: push-back and flow channels
Each day the installation puts together 440 orders, each of which comprises around 21 product lines. A specific zone was designed for order fulfillment to facilitate work by operators.
Interlake Mecalux has installed ten blocks of push-back racks. And below, it has set up a picking passageway where workers collect SKUs meant for each order, picking items directly off pallets located in the flow storage channels.
Reserve products are deposited in the push-back racks of the pick tunnel. As they are slightly inclined, this ensures and speeds up replenishment tasks. In this system, the pallets are inserted into each channel and are pushed along by forklifts, which assist the maneuver.
In terms of the picking tunnelway, it is filled with pallet flow channels for picking on each side. Pallets are placed into the loading aisle and, since it is inclined, these unit loads slide via gravity to the opposite end, which faces the pick tunnel. The advantage is reserve palletized stock stays stored in the same channel, which is why the company always has the products it needs for pick tasks.
One warehouse, four solutions
By combining multiple systems, the company can avail itself of the conveniences each solution brings its business.
Ultimately, the company has pooled the versatility and accessibility that pallet racks offer with the compactness and speed of the Pallet Shuttle system, while also accelerating order picking thanks to a zone specifically set up for this work (with push-back racks and a pick tunnel on the lower level).
Advantages for Tamer
- Prep of 440 orders a day: a specific warehousing zone was set up in the facility to fulfill orders, each order being an average of 21 lines long.
- Operational agility: the warehouse stands out for being pick-friendly and for receiving 700 pallets and shipping out another 800 pallets each day.
- High-density storage: Mecalux systems make maximum use of space to provide storage slots for 22,706 pallets.
Warehouse of Tamer | |
---|---|
Storage capacity: | 22,706 pallets |
Pallet size: | 39" x 48" |
Max. pallet weight: | 1.65 t |
Rack height: | 36' |
Gallery
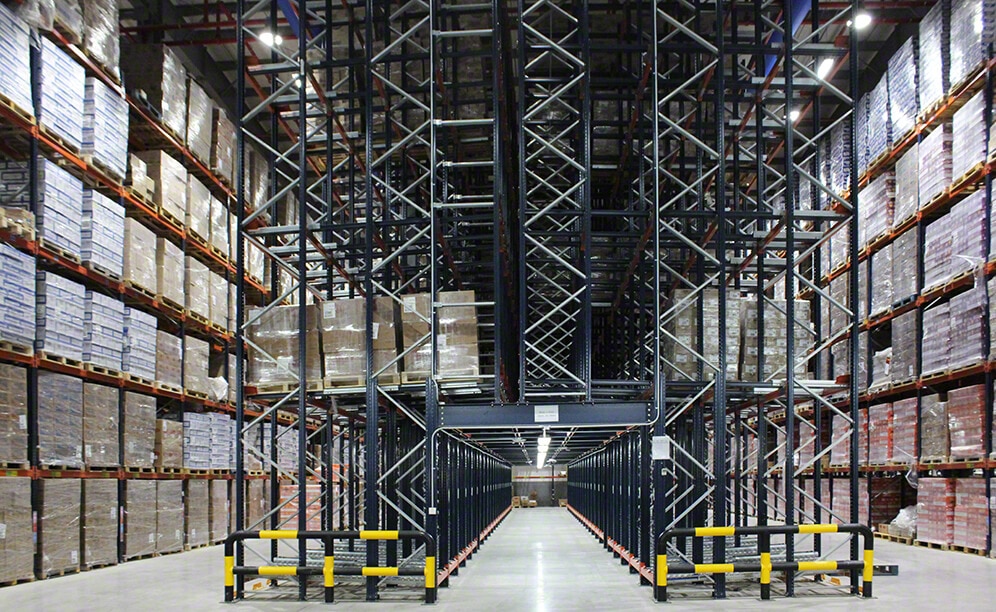
Tamer warehouse in Saudi Arabia with various storage solutions
Ask an expert