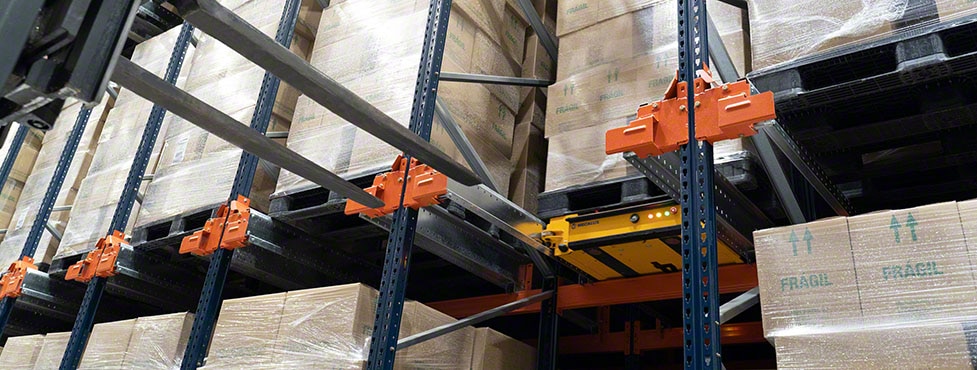
Nicopan: integration and innovation, the recipe for Easy WMS
Nicopan stores bakery products and pastries with the Pallet Shuttle system, managed by Easy WMS
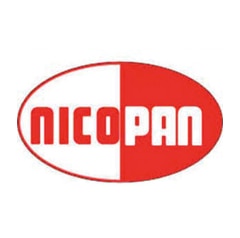
The warehouse of bakery goods and pastry producer Nicopan in Atarfe, Spain, is divided into multiple cold stores that Interlake Mecalux has equipped with the semi-automatic Pallet Shuttle system. In total, 9,931 pallets with finished products and raw materials are stored. Mecalux has also implemented the Easy WMS warehouse management system, as well as the Pallet Shuttle control software, prepared to direct the motorized shuttles used in this storage system.
Bread and butter
Nicopan was founded in 2014, born out of a family business that started in the sixties. It is dedicated to making bakery goods and pastries that are sold in supermarkets, restaurants and hotels in Spain and Portugal.
The company has a production plant in the town of Atarfe in southern Spain that stands out for incorporating the latest technology in all processes. Next to this factory is the warehouse, which has a dual function: on the one hand, it supplies production with the raw materials and packaging required for daily operations and, on the other hand, it stores and distributes the finished items.
Good communication between the two installations is crucial for preventing interruptions in service. All processes are coordinated to carry out the largest volume of work and, thus, dispatch and deliver orders on time.
Proper organization of the goods is crucial for Nicopan, especially since it manages 1,692 SKUs of different volumes, characteristics and demand levels. To eliminate any possibility of error, the warehouse has been divided into five cold stores. Each of them is used to accommodate a type of product stored under specific conditions.
The installation receives 100 pallets per day on average (from production and/or suppliers) and ships another 350 pallets to customers. These numbers increase at times of the year when there is a higher consumption of pastry goods, such as at Christmastime.
Taking this into account, Interlake Mecalux has fitted out the five cold stores with the semi-automatic Pallet Shuttle system. This high-density storage system uses an electric shuttle to load and unload pallets inside storage channels. It was chosen based on the following factors:
- The racks make the most of the available space, ensuring increased storage capacity. As their dimensions were adapted to the surface area of the various cold stores, the channels are between five and thirteen pallets deep. Overall, there is room for 9,931 pallets.
- By limiting the number of aisles, energy consumption for cooling is significantly reduced.
- Goods movements are quick and safe.
As more movements are carried out in the cold store for finished items, it is specifically designed to absorb a large number of inflows and outflows. It is formed by a single aisle with a racking unit on each side that can hold a maximum of 13 pallets deep. Mecalux has also installed pallet conveyors that automatically connect the production area with this storage chamber. Since the central aisle is very narrow, only one operator can work with the fork truck to insert or extract goods from their location and move the Pallet Shuttle to another channel when required.
Monitoring the operations
Nicopan has also implemented Easy WMS, the warehouse management system by Mecalux with which it manages its wide range of SKUs. This software controls inventory in real time and knows which stock is available and where each pallet is at all times.
Traceability is imperative when managing food products. By identifying each item, Nicopan can carry out extremely accurate monitoring of the goods across the various supply chain processes.
Likewise, Easy WMS continuously guides the warehouse operators, telling them where to deposit each product. For this, the workers use RF terminals to receive orders from the WMS and then confirm that they have been fulfilled.
Easy WMS has been integrated with Nicopan’s ERP to maximize the throughput of all the center's operations. The connection between these two systems has helped manage the vast amount of work:
Goods receipt
There are two types of inflows, depending on the product:
- Suppliers. The ERP notifies Easy WMS of the arrival of pallets sent by suppliers. The operators identify each of them with their RFID terminals so that the WMS can verify that no errors have been made.
- Production. Easy WMS registers the items that arrive from the production plant as the operators identify each pallet.
The receipt of the goods is a fast and intuitive process. Operators merely scan the barcode label of each pallet with their RF terminals, and the WMS accesses all the information it needs (SKU, batch and expiration date). This working method prevents data from being entered manually and mistakes from being made.
Pallet storage
Easy WMS uses rules and algorithms to assign each item a location based on its characteristics (whether it is a raw material or a finished product) and turnover. Operators read the pallet labels, and the WMS automatically tells them where to deposit the pallets.
The WMS controls the Pallet Shuttle to ensure maximum safety and agility in goods inflows and outflows. The operators have a tablet with which they carry out various actions, such as selecting the number of pallets to be removed from each location and taking inventory.
One of the advantages of the Pallet Shuttle system and its integration with Easy WMS is that operators can work from inside heated fork trucks without having to get out of them.
Goods dispatch
Goods are shipped in two ways: raw materials are sent to production, while orders (finished items) are distributed to Nicopan’s customers.
In the first case, the ERP tells Easy WMS which raw materials the production plant requires, and the WMS immediately generates an exit order, which the operators receive. This order constitutes a list of the pallets that the workers have to extract from the slots and transfer without delay to the production area.
To dispatch the shipments, Easy WMS assigns an exit order to a particular dock. As per commands sent by the WMS, the operators locate the items that make up each shipment and deposit them in the corresponding loading dock. The shipments remain there, waiting to be distributed.
Integration: the main ingredient
Nicopan has perfectly coordinated its warehouse with its production center, in terms of both sending raw materials and receiving finished items. For the two facilities to work in unison, it was essential to integrate Mecalux’s Easy WMS warehouse management system with the company's ERP.
With the installation of Easy WMS, Nicopan has an efficient logistics system, prepared to meet the needs of the production plant and supply customers as quickly as possible.
Nicolás Espigares - CEO of Nicopan
“We are thrilled with the Pallet Shuttle system by Mecalux because it has enabled us to cope with our business’s high rate of activity. I should also emphasize that the Easy WMS warehouse management system has been easily integrated with our ERP. This has prevented problems and helped us control all our supply chain processes.”
Advantages for Nicopan
- Coordination with production: the warehouse sends raw materials and receives finished items ready to be delivered to customers.
- Cost savings: the Pallet Shuttle system optimizes the available space, reducing energy consumption for cooling.
- Stock control: Easy WMS knows the status of the 1,692 SKUs of different volumes, characteristics and demand levels.
Warehouse of Nicopan | |
---|---|
Storage capacity: | 9,931 pallets |
Pallet size: | 32" x 47" |
Max. pallet weight: | 1.1 t |
Racking height: | 39,3' |
Racking length: | 118,1' |
Gallery
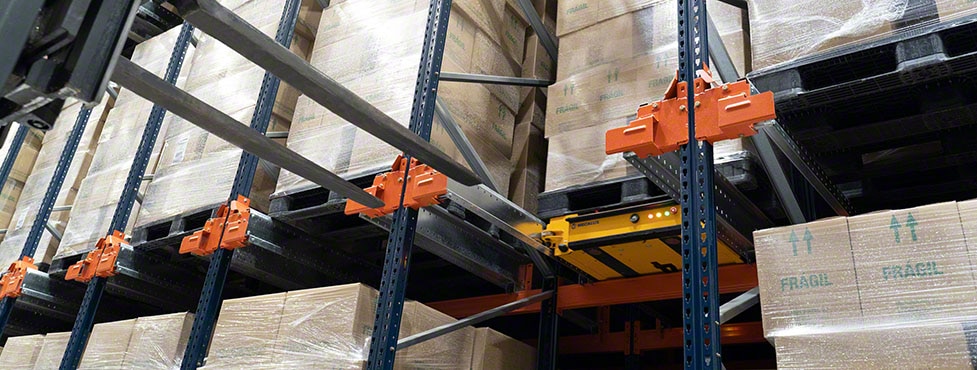
Pallet Shuttle system in Nicopan's warehouse in Atarfe (Spain)
Ask an expert