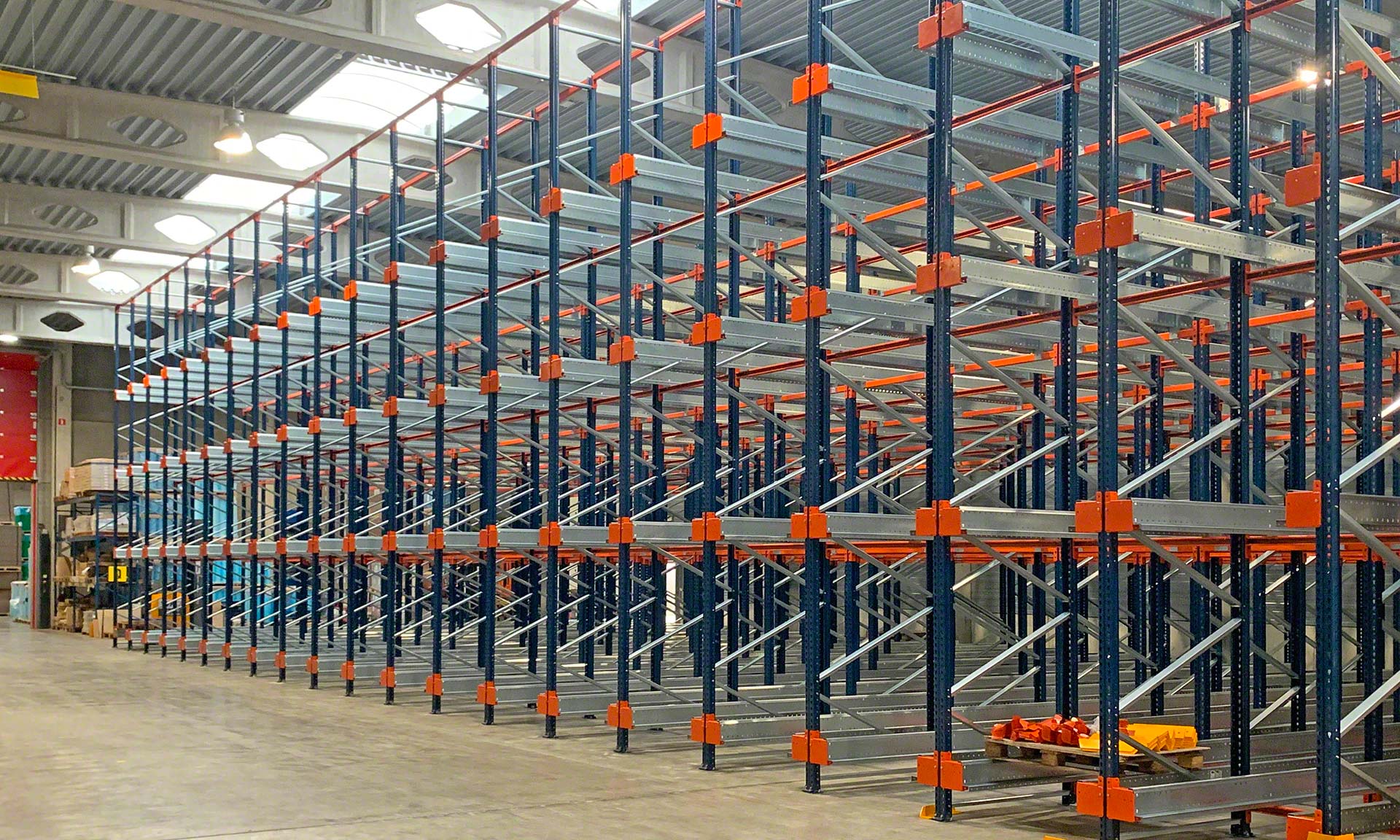
Manna Foods: maximum capacity in minimum space
The motorized shuttle streamlines entries and exits of Manna Foods' goods to and from their locations
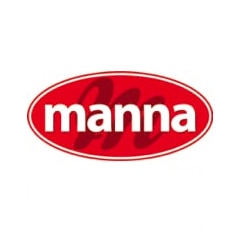
Sauce manufacturer Manna Foods has renovated its warehouse in Wijnegem, Belgium, with the installation of the Pallet Shuttle system from Mecalux. This solution makes the most of the available space to provide greater storage capacity: 1,120 pallets in just 3,767 ft². The secret? A motorized shuttle tasked with handling the goods, thereby streamlining pallet entries and exits.
Flavor and quality
Founded in Belgium in 1935, Manna Foods is a family-run business dedicated to the production and sale of all kinds of sauces and condiments served hot (carbonara, Bolognese, and tomato) as well as cold (mayonnaise, barbecue, and ketchup). This firm’s top priority is to develop irresistible, mouth-watering sauces that will attract more and more customers in Belgium and throughout Europe. To do so, it uses the best raw materials on the market and continuously modernizes all its production processes.
New warehouse
In 2018, the company needed storage space to cope with a rise in production. Thus, it moved to a new 29,063 ft² facility in the town of Wijnegem (northern Belgium). “From there, we distribute our sauces to supermarkets and food stores. Our logistics operations have to be agile enough to guarantee the timely supply of products to our customers,” says Sven Geysels, Logistics Manager at Manna Foods.
In the beginning, all goods were deposited on pallet racks, a solution that streamlined inflows and outflows. However, as production increased, part of those items had to be stored directly on the floor. “We were squandering our warehouse space. We realized we needed to optimize the available surface area more efficiently to be able to accommodate more products,” says Geysels.
The company overhauled its facility with the installation of a racking unit served by the semi-automated Pallet Shuttle system from Mecalux. Geysels says: “We visited the facility of one of Mecalux’s customers featuring this solution, and we exchanged impressions. From that moment, we were convinced that it was the best solution for our needs.”
Pallet Shuttle characteristics
Mecalux has set up a 95-foot-long, 26-foot-tall racking unit with the semi-automated Pallet Shuttle system. The racking unit takes up just 3,767 ft² and can store up to 1,120 pallets. It is a compact warehousing system consisting of two multi-deep storage channels that house pallets one behind the other; in the case of Manna Foods, each location holds 14 pallets. Geysels says: “This solution better leverages our available space and allows us to accommodate many more pallets.”
In addition to those advantages, this system ensures that storage tasks are extremely fast and safe: a motorized shuttle is charged with inserting the products in the deepest free location in a completely autonomous way. This frees operators from having to enter the aisles to handle the loads. “We’re extremely satisfied: we’ve achieved greater flexibility and efficiency in our warehouse operations,” says Geysels.
This agility was essential for Manna Foods to be able to provide its customers with optimal service and guarantee continuous goods movements in the facility. Every day, the production lines send the warehouse 100 pallets that need to be stored.
They are all distributed on the racks, taking into account their level of turnover (A, B, or C). Simultaneously, 136 pallets are sent to Manna Foods’ customers (mostly in Benelux countries and Africa).
The operation of this storage system is very simple and requires minimal intervention from operators: with the help of forklifts, the workers position the motorized shuttle in the corresponding channel and deposit the pallets in the first position in the racks. The electric shuttle then moves them to the closest free location. To remove the goods, the same process is performed but in the reverse order.
Geysels says: “Our operators got used to this system in no time, and their work is now much more efficient. Before putting the solution into operation, Mecalux held a very helpful and practical training session for our entire team. Plus, the system is so intuitive and user-friendly that our employees haven’t even needed to consult the training manual provided.”
The operators use a tablet to send instructions to the motorized shuttles. This device lets them perform a number of functions, e.g., select the quantity of pallets to extract, take inventory, or designate the goods management strategy (FIFO or LIFO).
Efficient logistics
Manna Foods has boosted the storage capacity of its warehouse in Wijnegem with the Pallet Shuttle system from Mecalux, a solution that optimizes the available surface area to store a greater number of products in a limited space.
The most evident advantage of this solution is the ease and agility with which it carries out goods entries and exits. The motorized shuttle makes pallet movements faster and safer.
This solution has enabled Manna Foods to deftly cope with the increase in production expected over the next few years and to serve its customers with the promptness for which it is known.
Geysels says: “In spite of the difficulties brought on by the coronavirus pandemic, we’ve grown, which was no easy feat. And we aim to continue doing so by 7-10% in the next year.”
The semi-automated Pallet Shuttle system from Mecalux has helped us to optimize the available surface area, making it more efficient to accommodate even more products. We’re thrilled with our facility: we’ve achieved greater flexibility and effectiveness in our operations.
Advantages for Manna Foods
- Floorspace optimization: the racking leverages all the available space to store up to 1,120 pallets.
- Effective goods management: the motorized shuttle inserts and removes products into/from their locations quickly and with minimal operator intervention.
- Easy-to-use system: the operators merely have to place the pallets in the storage channels, where a motorized shuttle then moves them to the deepest free location.
Pallet Shuttle system | |
---|---|
Storage capacity: | 1,120 pallets |
Pallet size: | 32" x 47" |
Max. pallet weight: | 1,764 lb |
Rack height: | 26' |
Rack length: | 95' |
Gallery
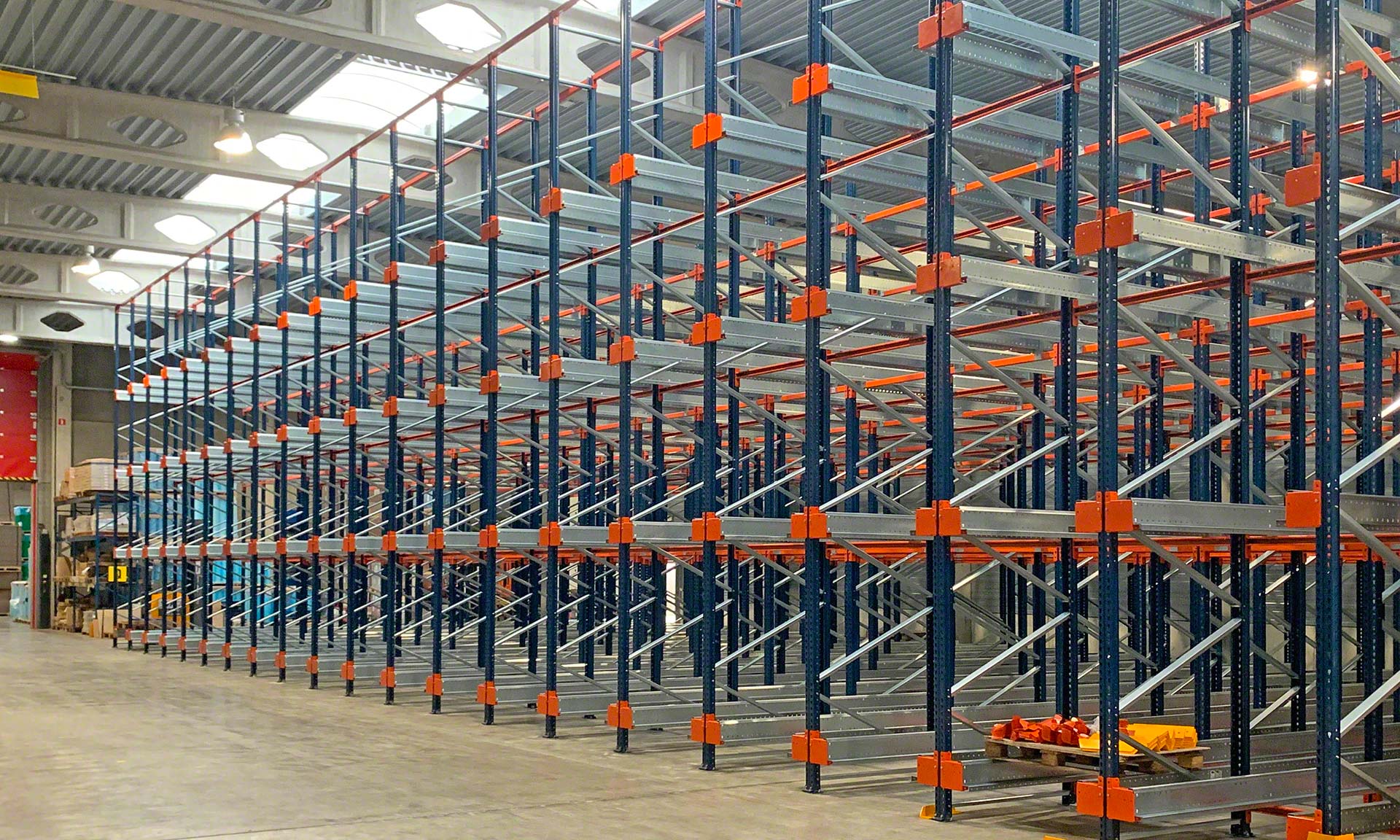
Manna Foods' warehouse in Belgium with the Pallet Shuttle system
Ask an expert