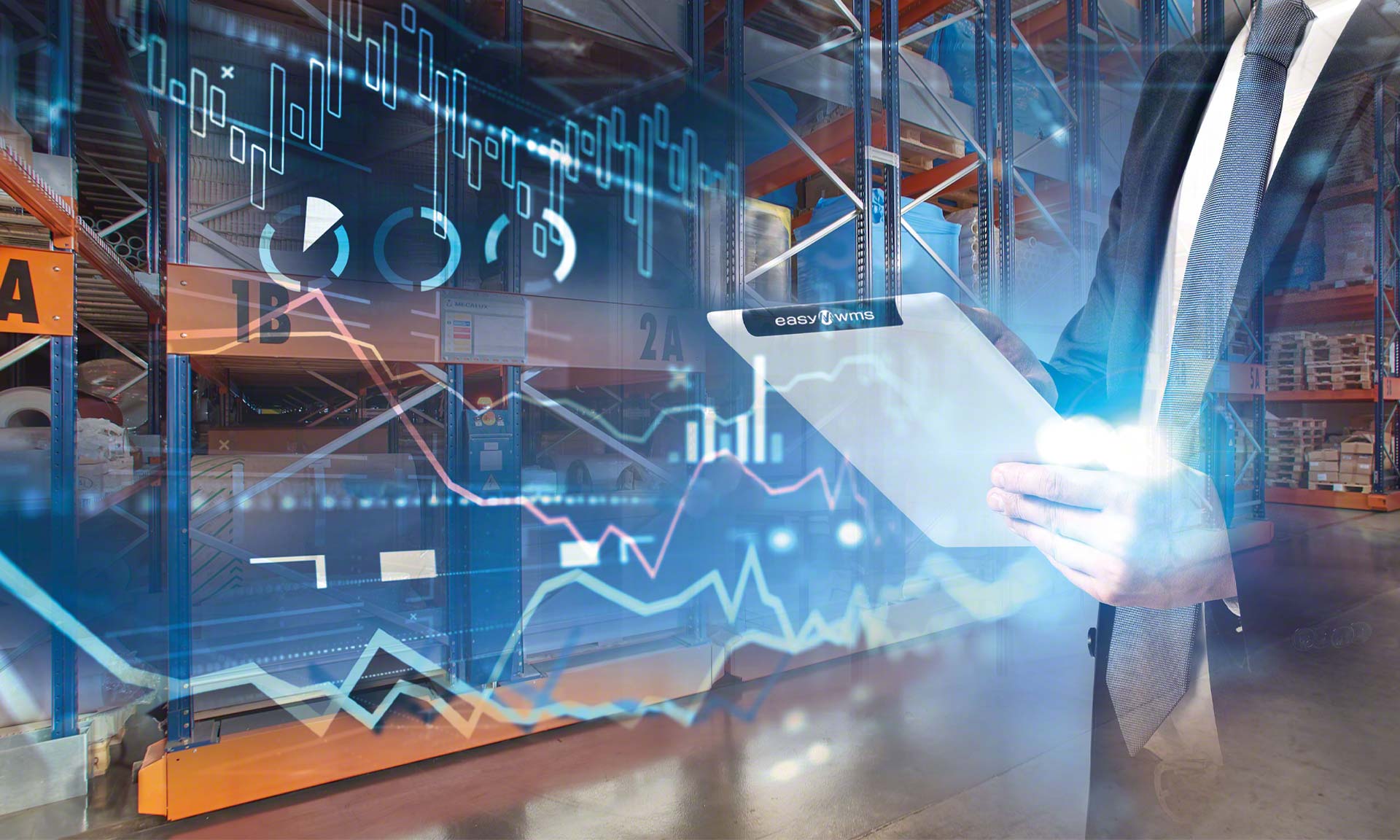
Madel digitizes its warehouse for air control equipment
Madel opens a digital warehouse run by Mecalux software to manage the status of its 250 SKUs in stock.
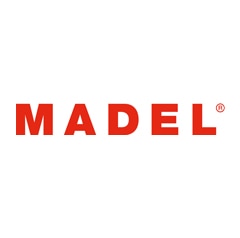
Madel, a business specializing in air diffusion and control products for air conditioning systems, has digitized its warehouse for raw materials. With Easy WMS, the company accurately controls all its SKUs and knows the exact location of its raw materials in real time.
Madel: air diffusion and control solutions
Madel is a Spanish company dedicated to the manufacture and sale of air diffusion and control products for air conditioning systems. Among its extensive product portfolio are air diffusers, supply grilles, control dampers, and fire safety and temperature control systems. The company works in conjunction with architects, engineers, interior designers, and installation technicians to offer quality products at a competitive price.
- Founded in: 1965
- Employees: 160
- International presence: 59% of production exported
CHALLENGES
|
SOLUTIONS
|
BENEFITS
|
---|
Transformation is part of Madel’s DNA. Since it was founded in 1965, the company has invested in innovation to expand its range of air control products and adapt to new market demands. Due to a rise in sales, Madel added on to its center in Centelles (near Barcelona). However, the increased workload and future growth prospects compelled the company to continue expanding and renovating this facility to align it with the business’s new requirements.
Previously, Madel stored all its goods in the production plant itself. But sharing a single space was no longer compatible with business growth. “We came to the conclusion that we needed more manufacturing space and that we could use the storage space occupied by the racks to expand our production processes,” explains Aleix Parés, Process Engineer at Madel. At that point, the company decided to open a new 2,691 ft² warehouse dedicated exclusively to the storage of all the raw materials.
This solution enabled Madel to free up space in its manufacturing plant, add more production lines, and keep close control of the raw materials. And it was able to do all this by digitizing its logistics processes with the help of the Easy WMS warehouse management system from Mecalux.
In addition to Easy WMS, Madel has equipped the facility with Movirack mobile pallet racking, a system that greatly boosts storage capacity. “Our warehousing space was limited, so we were looking for a solution that would make the best use of it,” says Parés.
Digital warehouse before and after
“We digitized our logistics processes as a result of opening the new warehouse because we knew they could be improved,” says Parés.
The installation of Easy WMS has marked a before and after for Madel’s supply chain. Stock control is flawless: the software monitors the goods from the time they enter the warehouse until they are sent to the production lines.
The first improvement in Madel’s facility can be seen in the raw materials receiving area. This space is key since it constitutes the origin of all operations. Previously, operators managed the goods receipt process aided by the company’s ERP system. When the raw materials arrived at the production center, the operators would enter them into the ERP system manually, where they were recorded as “production center”; that is, operators knew they were in the building but could not pinpoint their precise location. “The goods could be slotted at one end of the warehouse or the other, depending on where space was available,” says Parés.
Digitizing the warehouse with Mecalux software has meant a leap forward for goods receipt management: all products are controlled automatically. Every day, when the facility receives pallets sent by suppliers, the operators merely have to read the barcodes with their RF scanners. The goods are automatically recorded in the Easy WMS database, and the system assigns each pallet a location taking into account the product type, SKU, and consumption level.
The software provides information on stock in real time, so operators always know exactly where each product is slotted. With Easy WMS Madel has not only shortened the time spent on goods receipt but also streamlined storage and order picking tasks.
“Before implementing the software, when we ordered an item from the warehouse, we had to wait until the operators could go and pull it. Now, we enter it into the WMS, and the system instantly tells us the specific location, availability, and quantity. We’ve saved a lot of time when it comes to finding products,” says Parés.
By means of the RF scanner, Easy WMS sends the operators instructions on how to do each job: from where to slot the goods to which raw materials to send to production. By following the software’s instructions, operators are much more accurate.
“Easy WMS has helped us to better supervise everything that happens in the facility. Prior to its deployment, we had no way of knowing which operators had entered the warehouse or which items they’d picked if they weren’t recorded in the ERP system,” says Parés.
Another improvement made to Madel’s center is digitization of its inventory management. In the past, operators had to travel around the warehouse counting the items one by one to know the number of products stored.
Manual management could lead to discrepancies between the amount of available stock according to the ERP system and the products actually stored on the racks.
Easy WMS, however, ensures perpetual inventory: the software knows which items are available in the warehouse at any given time. “We’re sure that the information contained in Easy WMS is 100% reliable because we now have extremely strict control over the goods that enter and leave the facility,” says Parés.
BEFORE Manual stock management |
NOW Stock management with Easy WMS |
---|---|
Manual entry of items received in the ERP system. | Automatic entry of items received in the Easy WMS database via barcode scanning. |
Lack of accuracy in knowing which items were available. | Exact location and available quantities of each item in the warehouse are known. |
Operators walked around the entire facility to find the item they needed. | Optimized routes: operators travel minimal distances to locate products. |
Lack of control in processes and in goods management. High risk of error. | The software sends operators detailed instructions on how to do each job without making mistakes. |
Physical inventory: operators traveled around the facility counting the items stored one by one. | Perpetual inventory. Easy WMS knows precisely where each item is located. |
Ever-changing, ever-expanding logistics
Madel has modernized its production and logistics processes to increase its rate of expansion. The opening of the new warehouse, which has enabled it to add more production lines, falls within the business’s plans for growth.
With the new digital warehouse, the company can now effectively monitor its more than 250 SKUs. Easy WMS has completely overhauled Madel’s logistics operations. The software provides information on the status of the raw materials in real time and organizes all operations, from the storage of the goods until they are sent to production.
Madel’s future prospects are extremely promising. “In 2021, despite the difficulties brought on by the pandemic, we obtained positive results. And we expect to see that trend continue in the years to come,” says Parés. The business is set to make that happen with the efficient organization of its logistics operations and its products through digitization.
Movirack mobile racks: storage capacity and direct access
Movirack mobile racking is the only compact storage system that offers direct access to the goods. Installed on mobile bases, the racks can be moved to open the working aisle required and to access the location where the goods are to be deposited or retrieved, facilitating stock management. The movement of the racks is completely safe, as they are equipped with motors, electronic equipment, and safety devices.
“We chose Movirack mobile racks from Mecalux because they provide high space occupancy and enable direct access to the products,” says Parés. “We’re really happy with the result — we’ve doubled our storage capacity.”
We’re thrilled to have real-time stock management. We only have to enter a product in the system to know its availability, quantity, and location. With Mecalux software, we can find the raw materials we require much more easily.
Madel responds:Interview with Aleix Parés, Process Engineer at Madel |
---|
What made you open a new warehouse? We used to store our goods in the production plant. But with the increased pace of growth came the need to expand manufacturing space. And the best option was to use the floorspace where the racks stood to expand our production processes. So, we decided to separate the warehouse from production. We opened a new 2,691 ft² facility to house all our raw materials. |
Why did you outfit the warehouse with Movirack mobile racks? The new facility had limited space, and we were looking for a solution that could make the best use of it. We chose Movirack mobile racks from Mecalux because they provide a high occupancy of space and offer direct access to the products. We’re really happy with the result — we’ve doubled our storage capacity. |
|
In opening the new warehouse, you’ve also digitized your logistics processes. Why? The digitization of our logistics operations was a consequence of opening the new warehouse. Although our main problem was the lack of space, when we began considering solutions, we realized our logistics operations would benefit from an upgrade. Before, we didn’t have such tight control over stock in the production center: we only knew what movements the operators made, e.g., the pallets they brought to the production lines. Since we didn’t know where the goods were located, we lost a lot of time trying to find the pallets we needed. This was one of the reasons why we wanted to implement a warehouse management system. After comparing different options, we decided on Easy WMS. Mecalux is our go-to racking supplier, so we’re confident in its technical team and its warehouse management software. |
How did you manage your goods before implementing a WMS? We did this manually, with the help of our ERP system. When the items sent by suppliers arrived at the production center, the operators would manually enter them into the ERP system. This software recorded them merely as “production center”; that is, we knew the products were in the center but not their exact location. The goods could be slotted at one end of the warehouse or the other, depending on where there was available space. |
|
What improvements have you seen with the installation of Easy WMS from Mecalux? The software has enabled us to control our stock much more effectively. In the last inventory, we noticed a huge difference. We no longer have stock discrepancies. The quantities of items available according to the WMS always match the goods stored. We’re sure that the information contained in Easy WMS is 100% reliable because we now have extremely strict control over the goods that enter and leave the warehouse. The software has also helped us to better supervise everything that happens in the facility. Before, we had no way of knowing which operators had entered the warehouse or which items they’d picked if they weren’t recorded in the ERP system. |
What are Madel’s future prospects? Our business is constantly growing. The project to open a new warehouse is a consequence of the pace of expansion we’ve experienced in recent years. In 2021, despite the difficulties brought on by the pandemic, we obtained positive results. And we expect to see that trend continue in the years to come. |
Ask an expert