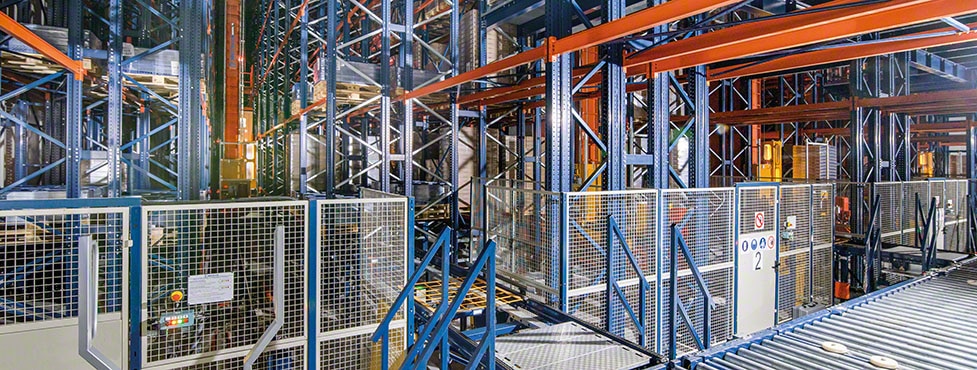
Automation at Lantmännen Unibake's warehouse: our daily bread
Automation of its operations enables the company to dispatch close to 100 pallets/hour to its customers in Poland
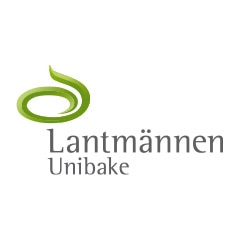
Behind every baguette is a complex logistics network that must operate with the utmost efficiency to achieve the quality customers expect. Well aware of this, Lantmännen Unibake, one of Europe’s leading bakery groups, has relied on technology to streamline its supply chain and ensure goods traceability. The company has built a new logistics center in Nowa Sól, Poland, capable of dispatching close to 100 pallets per hour. Connected to production, the facility has two automatic storage systems that provide a total capacity of 15,920 pallets containing refrigerated and frozen products.
Tradition and innovation
Founded in 1880 and headquartered in Copenhagen, Denmark, Lantmännen Unibake is one of the main suppliers of fresh and frozen dough for the production of baked goods and pastries in Europe.
The company supplies hundreds of restaurants, supermarkets, fast-food establishments, service stations and catering businesses with bread for their customers. In recent years, Lantmännen Unibake has expanded globally, opening production plants in Belgium, Denmark, Sweden, Norway, Poland, Germany, Russia, Finland, the UK and the US.
Currently, the company has an annual turnover of 1.2 billion dollars and employs over 6,000 workers. It boasts 36 production plants in 20 countries and sales outlets in 60 countries all over the world.
Technology and traceability
Since its arrival in Poland in the 1990s, Lantmännen Unibake has constantly increased its production rate. Over the past few years, it has successfully marketed an impressive 33,000 tons of frozen bread to hundreds of customers in that country.
To face this rise in demand and strengthen its growth, the firm has opened a new 5.93 acre production plant in the town of Nowa Sól, one of western Poland’s most industrialized areas. This is Lantmännen Unibake’s third production plant in this country (after its first two in Poznań and Nieporęt) and its second largest in Europe.
“At our logistics center in Nieporęt, we use non-automatic storage systems, such as pallet, drive-in and mobile racks,” says Jerzy Sobieszczuk, Supply Chain Manager at Lantmännen Unibake in Poland and Hungary. However, “we were managing a flow of about 10 to 12 pallets per hour, which was not enough for our growth prospects. We needed to look for more effective storage systems because we wanted to ramp up the number of entries and exits,” he adds.
The company understood that automation was the only possible way to remain competitive. Therefore, it has equipped the installation at its production plant in Nowa Sól with two automated systems: one for managing refrigerated products and a clad-rack structure for frozen products (-18.4 ºF). Connected to production, the warehouse is fitted out with the latest technology to ensure controlled and precise goods flows, Stacker cranes, conveyors and lifts are charged with moving the products to the various points throughout the installation, operating 24 hours a day without interruption.
Traceability is imperative when managing food products such as those of Lantmännen Unibake. To guarantee optimal product quality, it is necessary to monitor the goods in all stages of both production and the supply chain.
Goods arrival
The logistics center is right next to the production lines, and the two buildings are connected by a conveyor circuit.
The conveyors transport the palletized products to the storage area. Once there, they go through a checkpoint, where their characteristics and compliance with several established and required parameters (mainly weight and size) are verified. Subsequently, the warehouse management system (WMS) determines whether the goods should be stored in the refrigerated or frozen section, assigning them a location.
In the words of Jerzy Sobieszczuk, “the productive capacity of a single production line at the new plant in Nowa Sól is greater than that of the entire manufacturing facility in Nieporęt.”
An entry point has also been set up for products arriving from other Lantmännen Unibake production centers. It is located alongside the loading docks and — just like the production entry zone — has two hydraulic tables and a checkpoint through which products pass before being placed on the racks.
One installation, two automatic systems
The storage area for frozen products (-18.4 ºF) is a clad-rack warehouse occupying a surface area of 28,255 ft². With this type of structure, the racks not only support the unit loads, but also the rest of the building, since the roof and side walls are attached to the racking. This construction system optimizes both the available surface area and height to achieve the maximum storage capacity.
This zone has five aisles with double-deep racking on both sides that can hold 15,120 pallets (mainly with frozen bread). In the end, Lantmännen Unibake chose this option because the 131-foot-tall double-deep racks cut costs related to energy consumption. The more space the goods take up, the less the volume that needs to be cooled.
In each aisle, a stacker crane moves at a speed of 722 feet per minute. These machines are equipped with telescopic forks to be able to reach pallets in the deepest locations.
Just in front of these aisles and inside the site is a lower (60.7') automatic storage aisle, which operates at a cooled temperature of between 39.2 and 59 ºF. It is made up of a single aisle with double-deep racking and capacity for 800 pallets (fresh products).
Jerzy Sobieszczuk - Supply Chain Manager at Lantmännen Unibake in Poland and Hungary
“We chose Interlake Mecalux after analyzing and weighing various options. From the beginning, Interlake Mecalux told us that a few months of tests would be necessary to start up the installation successfully. In our case, however, the process was carried out relatively quickly. We began testing at the beginning of May 2019, and the final tests were run at the end of August. Presently, we are thrilled with the warehouse operations. They are running smoothly, and we can count on them to fulfill their intended purposes.”
Dispatch organization
At the front of both automatic systems is a conveyor circuit distributed among two floors where different operations are carried out. Entry and exit points to/from the cold storage area have been set up on the lower level, as has the exit point of flows from the freezer store to dispatch zone. Meanwhile, the entry of goods from production to the freezer store takes place on the upper level.
“The plant in Nowa Sól has an extensive dispatch area where we load between 12 and 18 trucks, approximately equivalent to 600 pallets, during every work shift (8 hours). We aim to increase this figure in the future,” affirms Jerzy Sobieszczuk. This zone comprises three groups of three preload channels, each of which can store eleven pallets. Each channel group holds a total of 33 pallets, the full capacity of a truck.
A warehouse with a present and a future
Lantmännen Unibake has automated its logistics systems with the aim of streamlining and optimizing the goods storage, preparation and dispatch processes at its factory in Nowa Sól. Technology has also helped it to achieve total traceability of its goods.
Automation has offered the company numerous advantages, including reduced operating costs, speedy goods management, product control and improved hygiene in the installation, among others. Ultimately, the firm’s productivity has been boosted considerably.
In addition, the installation is prepared for the business’s future growth. According to Jerzy Sobieszczuk, Supply Chain Manager at Lantmännen Unibake in Poland and Hungary, “the automated clad-rack warehouse was designed in a modular way; that is, we can expand the installation as our production pace quickens, adding more aisles to the five we have now.”
Advantages for Lantmännen Unibake
- Total traceability: automation enables extremely strict control of the goods throughout Lantmännen Unibake’s entire supply chain.
- Uninterrupted activity: the installation operates 24 hours a day, guaranteeing entries of pallets from the production plant and other warehouses, as well as the distribution of approximately 100 pallets/hour from the company’s customers in Europe.
- Automatic connection with production: the logistics center is directly linked to the production lines via a conveyor circuit, slashing logistics costs considerably.
- Two temperatures: Lantmännen Unibake has a storage area for frozen products and another for cooled goods to ensure optimal food quality.
Cooled zone | |
---|---|
Storage capacity: | 800 pallets |
Warehouse height: | 59' |
Pallet sizes: | 32" / 39" x 47" |
Max. pallet weight: | 1.1 t |
Temperature: | 39.2 - 59 ºF |
Gallery
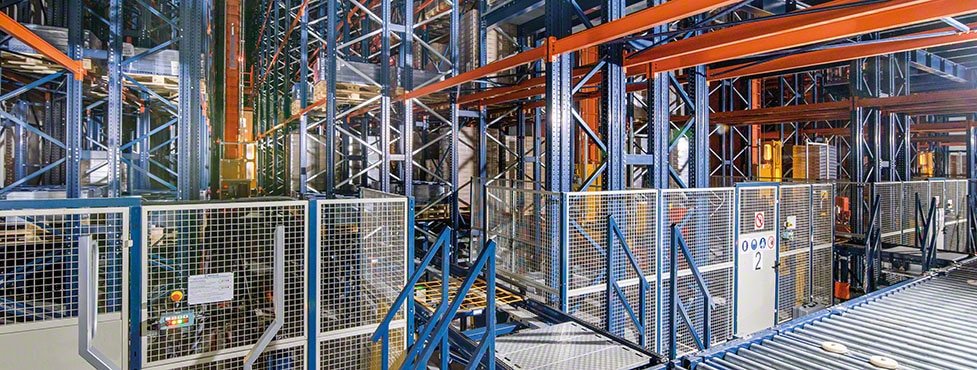
Lantmännen Unibake's automated clad-rack warehouse in Poland
Ask an expert