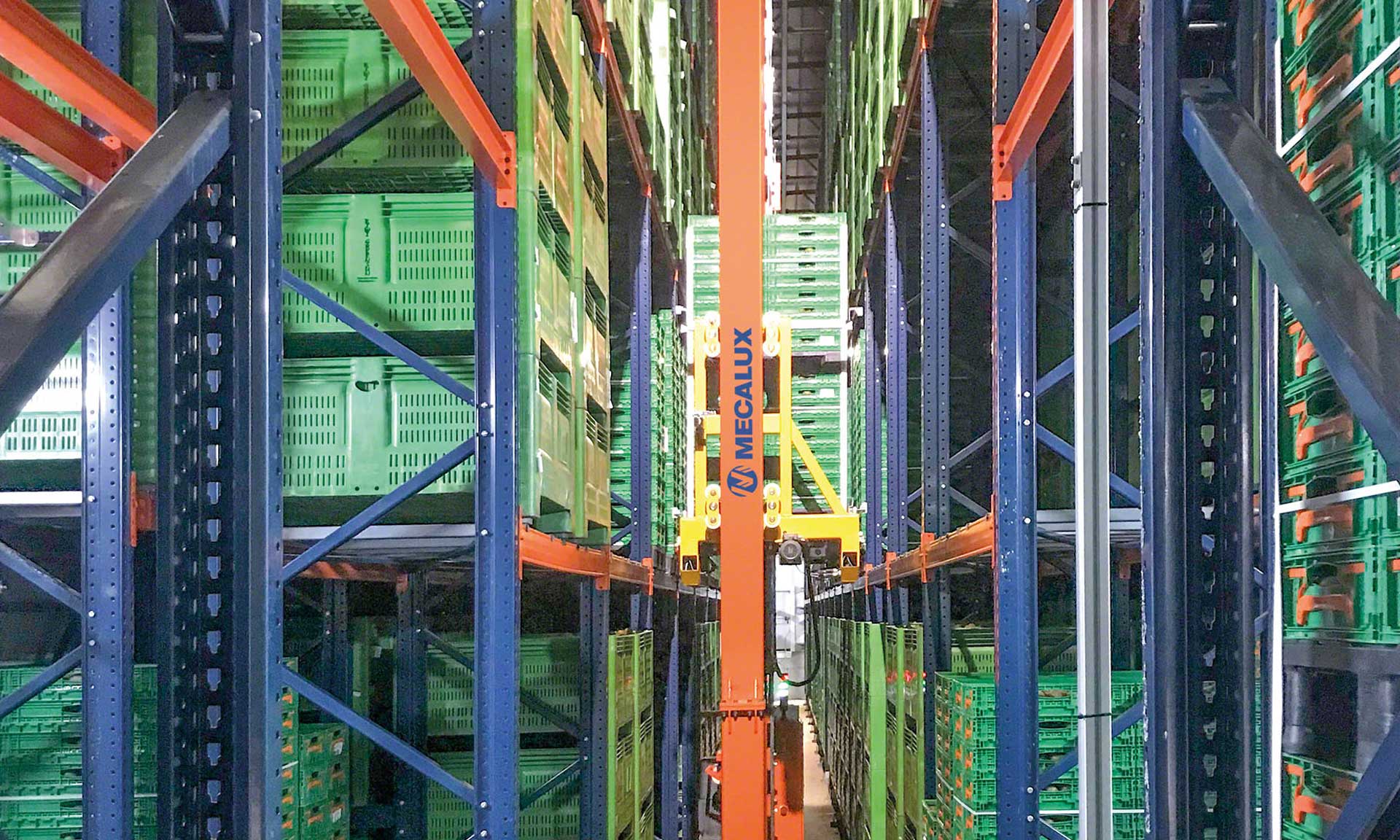
Kiwi Greensun: the perfect degree of ripeness for a cold storage warehouse
With the new installation, the company aims to raise yearly production to 13,230 tons of kiwi
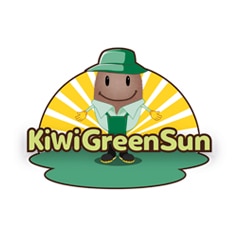
Kiwi Greensun, the Iberian Peninsula’s largest producer of kiwis, has overhauled its fruit ripening room in Salvador de Briteiros, Portugal, with the construction of an automated clad-rack warehouse by Interlake Mecalux managed by Easy WMS. With this installation, the company has its sights set on raising production to 13,228 t of kiwi fruit a year. One of the advantages of this warehouse with fully automated operations is the accurate control of products stored at refrigerated temperature.
Steady rise in production
Since it was founded in the 1980s, Kiwi Greensun has experienced unabated growth, becoming the Iberian Peninsula’s largest kiwi producer, with over 1,035 acres of land planted and 46 producer partners. The brand supplies Mercadona, one of the largest supermarket chains in Spain and Portugal, with more than 4,400 tons of kiwi fruit a year. In 2004, Kiwi Greensun opened a 26,900 ft2 warehouse in the Portuguese city of Salvador de Briteiros.
Since then, it has expanded the facility numerous times to absorb the company’s growth and increased production. It now boasts a surface area of 156,000 ft2 where it manages 11,464 t of kiwis a year at refrigerated temperature. Its goal for the next few years is to ramp up production even more until reaching 13,228 t per year. Therefore, Kiwi Greensun has decided to revamp its warehouse with the aim of ensuring that the kiwis are stored correctly and delivered at the optimal point of ripeness to satisfy demand as well as its customers’ discerning palates.
As the production rate went up, the company realized it needed to automate inflows and outflows to step up the pace. In this vein, Vítor Araújo, General Manager at Kiwi Greensun, explains, “We were well aware that the future of our business depended on automation. Not only would it make us quicker, but it would also enable us to have full control over our production and stock.”
To modernize its logistics systems, Kiwi Greensun sought the cooperation of Mecalux because, according to the General Manager, “Among the companies competing to carry out this project, Mecalux’s proposal was the right fit. Plus, the videos the team showed us of other facilities it had outfitted sealed the deal for us.”
Automated logistics operations
Kiwi Greensun has completely renovated its ripening room with the construction of a 43-foot-tall automated warehouse providing storage for up to 512 pallets.
The warehouse operates at a refrigerated temperature of between 32 and 32.9 °F and a humidity of 97%. This fosters the correct ripening of the kiwis, ensuring that their flavor and properties are maintained for a longer period of time. Automation, meanwhile, makes the most of the available space, notably reducing energy consumption for cooling and, thus, the energy consumption per pallet.
As a clad-rack building, the warehouse is formed by racks that withstand their own weight in addition to that of the goods, the vertical cladding and the roof. The advantage of this type of facility is the optimization of space, as it is built in conjunction with the racks. In fact, the Kiwi Greensun warehouse takes up merely 4,300 ft2 of surface area, occupying only the essential space.
The installation consists of a single 180-foot-long storage aisle with double-deep racking on both sides. Each location houses two single-SKU pallets lengthwise. To place pallets one behind the other, the stacker crane incorporates a double-deep extraction system with telescopic forks.
The racking, divided into four levels, has been personalized to be able to accommodate three different unit loads: 47” x 47” plastic containers and pallets measuring 32” x 47” and 39” x 47”. In the case of plastic containers, each location can store up to four containers stacked one on top of the other.
An entry point and an exit point have been set up on one side of the racks. Both are equipped with chain conveyors and access doors that help to maintain a controlled temperature inside the cool store. The goods remain stored for the time required for the kiwis to reach the appropriate ripeness to be distributed, sold and consumed.
Traceability as a top priority
The traceability offered by Easy WMS is key when it comes to maintaining food safety throughout all the stages through which the kiwis go before arriving in the hands of customers. Traceability would enable Kiwi Greensun to pinpoint the origin of an incident in short order and ensure the withdrawal of the affected kiwi fruit from the market in the event of an alert.
Additionally, the high degree of precise, real-time goods control provides consumers with accurate information and guarantees the utmost quality of the products. To achieve this, coordination between the WMS and ERP (enterprise resource planning) system is vital. Therefore, Easy WMS has been integrated with the Kiwi Greensun’s FLOW ERP system, exchanging data and information on how to perform the various operations more effectively.
Easy WMS assigns a location to each pallet and/or container as they go through the pallet checkpoint. “One of our main priorities when commissioning this automated warehouse was to organize products efficiently based on their demand level,” says Vítor Araújo. To decide which location to assign to each pallet, Easy WMS incorporates rules and algorithms, such as the partner that sent the kiwis and the necessary ripening time.
To dispatch the goods, Easy WMS orders the extraction of the required load unit and removes it from the inventory after it crosses the exit point. Subsequently, it sends a message to Kiwi Greensun’s ERP system for an operator to pick it and move it to the dispatch area.
Quality and customer satisfaction
The success enjoyed by Kiwi Greensun over the past few years lies in its commitment to customer satisfaction. Its main priorities are to improve the quality of its kiwi fruit and to ensure that deliveries are made without delay and at optimum ripeness.
Kiwi Greensun’s new clad-rack warehouse has provided it with much speedier inflow and outflow processes in addition to much more rigorous control of the kiwi fruit. As a result, “We’re going through a growth phase, and we expect it to continue,” enthuses Vítor Araújo.
Although we’ve just recently started-up this warehouse, we can say we’re extremely satisfied with the benefits it’s given us so far: we now have much more agile and efficient operations, strict control of the products and total traceability.
Advantages for Kiwi Greensun
- Stock control: automation and the Easy WMS warehouse management system ensure strict control of all the goods to preserve the quality of the kiwi fruit stored at refrigerated temperature.
- Improved agility: the stacker crane moves the kiwis in a much quicker, safer and more controlled way compared to traditional storage systems.
- Leveraged space: in just 4,300 ft² of surface area, the automated warehouse can accommodate the increased production seen by Kiwi Greensun in recent years.
- Energy savings: by making the most of the available surface area, automation reduces energy consumption for cooling.
Automated Warehouses for Pallets | |
---|---|
Storage capacity: | 512 pallets |
Warehouse height: | 49’ |
Warehouse length: | 180’ |
Temperature: | 32-32.9 ºF |
Gallery
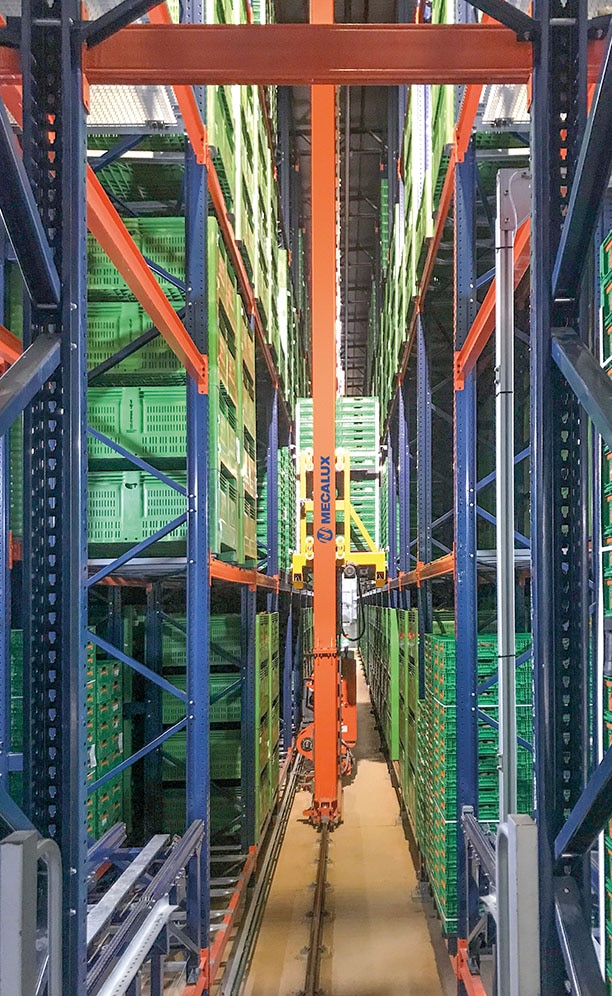
Kiwi Greensun's new, automated warehouse in Salvador de Briteiros, Portugal
Ask an expert