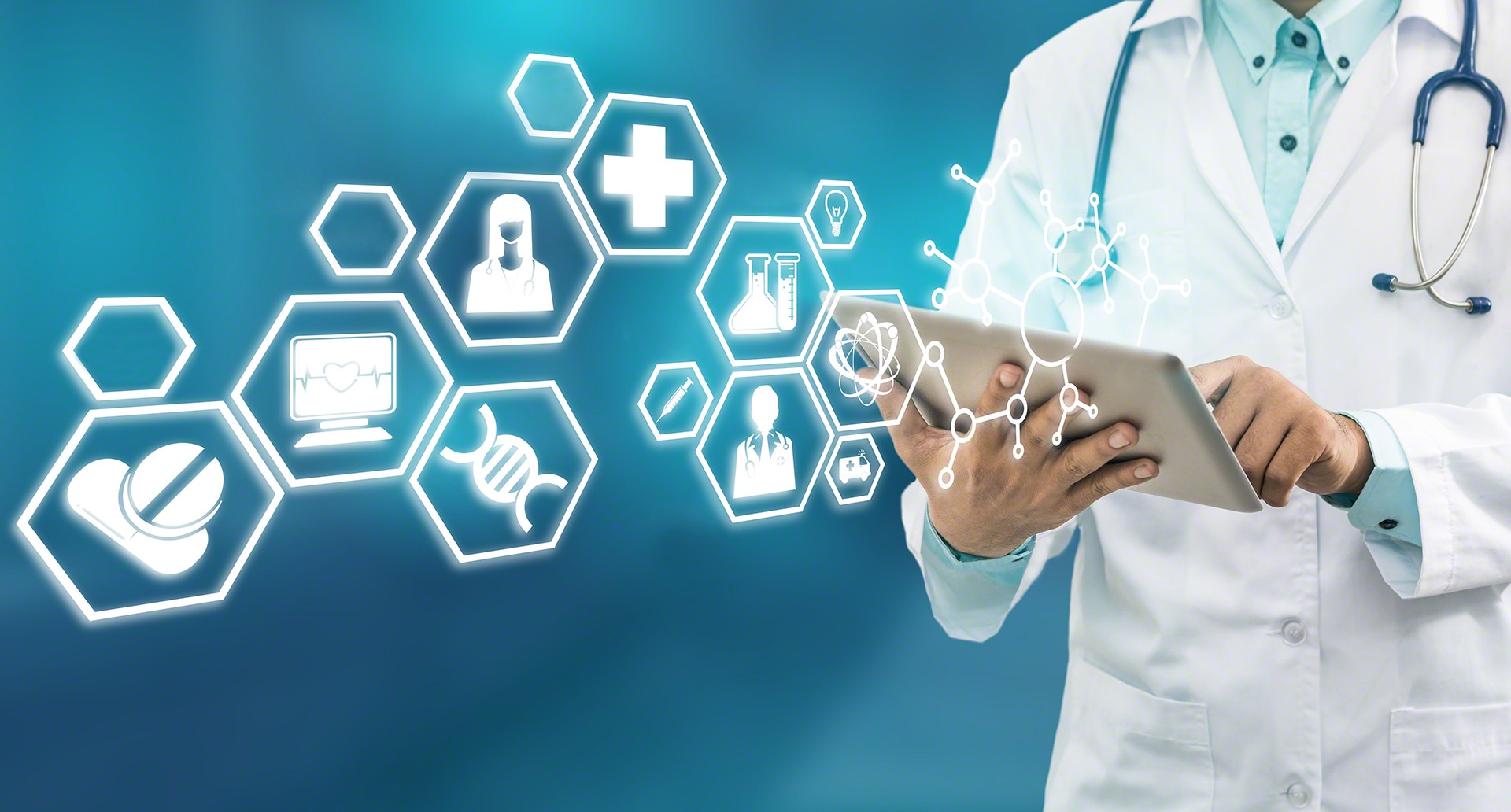
Intersurgical's logistics breathes traceability and security
Easy WMS optimizes the resources in the warehouse, from storage systems to the work of the operators.
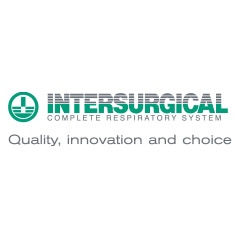
Intersurgical, a multinational specializing in medical devices for respiratory care, has completely transformed the organization of its warehouse in Wokingham, UK. The company has sectioned it into zones in which different operations are carried out in order to avoid interference and reduce the risk of errors. The real change, though, has been brought about by the installation of Easy WMS, the warehouse management system by Mecalux. This software provides stricter goods control, as it knows the exact location and the status of the 3,000+ available SKUs, which is essential when dealing with medical products. With this solution, Intersurgical has been able to cope well with the increased number of orders due to COVID-19.
Extensive range of respiratory products
With more than 30 years of experience, Intersurgical is a multinational that, every week, manufactures and distributes four million respiratory care products for the medical and hospital sector providing solutions for use in anesthesia, critical care, and oxygen and aerosol therapy. It is represented globally via direct subsidiaries and exclusive specialty distributors.
The town of Wokingham (just 31 miles from London) is home to Intersurgical’s UK headquarters and a warehouse to store and dispatch stock for the UK market. In recent years, management of this installation has become more complex due to the rise in the number of SKUs (which stands at over 3,000), new market challenges and the expansion of business on an international level.
“For us to continue growing, our logistics systems needed to be more robust and flexible,” explains Charles Bellm, Managing Director of Intersurgical. It was then that the company decided to implement Easy WMS, Mecalux’s warehouse management system across a number of international sites.
Warehouse management system Easy WMS has been integrated with the EFACS ERP at Intersurgical. Both systems communicate via an SQL Server database, exchanging data and information on how to carry out the various operations more efficiently. As a result, the logistics operation has been streamlined with the preparation of up to 500 orders a day.
Intersurgical’s Wokingham facility is divided into specific areas that have different operations but are perfectly interconnected:
- Receipt and storage. Product from the manufacturing sites and from UK and European suppliers arrives here. This zone also houses reserve products from the picking area.
- Order preparation. Dedicated entirely to picking, items used in this operation are deposited here, while orders are put together, consolidated and dispatched.
To prevent interference that could lead to errors, operators can only work in the zone assigned to them. An intermediate area for exchanging goods has been set up (for example, transfers of reserve products required in order preparation), always under the supervision of Easy WMS.
How Intersurgical has boosted productivity
Mecalux’s Easy WMS not only controls all processes but also optimizes them. This software oversees operators at all times, telling them how to do their work effectively. In this way, Intersurgical is prepared to face any challenge, such as the surge in the number of orders due to the coronavirus pandemic.
The company is a key supplier of respiratory devices and has worked with the UK’s NHS (National Health Service), supplying medical devices that have been needed by patients with COVID-19.
Intersurgical has relied on the tireless efforts of its team, the organization of the resources in its installation, and digitalization to provide the best service and dispatch of products in the shortest time possible. And Easy WMS has contributed to this success by assisting in efficient warehouse operations, including goods receipt and storage.
Goods receipt and storage
Every day, the Intersurgical installation receives an average of 175 pallets with different products and origins: raw materials from suppliers, customer returns, and finished products. These finished goods are sent from the production plant in Wokingham (the production facilities and warehouse are on the same road) or from Intersurgical’s production centers in Europe, Guernsey (UK) and Lithuania.
The installation operates according to Advanced Shipping Notices (ASNs). This means that the EFACS ERP notifies Easy WMS in advance of the items scheduled to arrive. Easy WMS then generates and prints labels, which workers place on each product while carrying out the relevant checks.
Once the items are identified, Easy WMS assigns them one of the 5,927 locations available in the warehouse. To do this, it takes into account (mainly) the type of product, its demand level and whether it is needed to prepare the orders. Thus, for example, higher-turnover items are deposited in the most accessible locations.
Picking
This is the main operation performed. Every day, workers finish and dispatch up to 500 orders. Easy WMS contributes towards streamlining the operation:
On the one hand, the WMS simplifies the employees’ work, telling them where to locate the items they need and how many of them to pick. The WMS creates a route throughout the installation, guaranteeing that operators travel the minimum distances.
On the other hand, it distributes the goods based on their demand level, thus, facilitating their location whenever necessary. To carry out picking, workers remove the boxes directly from the pallets located on the lower levels of the shelves. Easy WMS ensures that these locations are stocked with products. To do so, it organizes replenishment ahead of time.
Restocking is done in two ways: by placing the reserve pallet – originally on the upper shelving levels – in the required location or by moving the corresponding pallets from the storage zone to the picking area.
Dispatches
The ERP informs Easy WMS of the articles to be dispatched and their destination. Typically, 120 pallets are sent to the company’s customers in the UK every day. There are also orders for other Intersurgical Group sites, mainly those in Lithuania, France and Germany (400 pallets a week).
When the shipment includes items housed in the receipt and storage area, operators extract them from their locations and deposit them in the intermediate zone. Following this, the worker in the dispatch area picks them and takes them to the corresponding dock.
“All these movements and transfers of pallets from one warehouse zone to another are supervised by Easy WMS. Therefore, the system knows exactly where all the products are located at all times, with a view to avoiding mistakes,” highlights Intersurgical’s Managing Director.
Stringent goods control
Intersurgical has improved the processes of its installation in the UK to keep up with its growth. Digitalization and automated resource management by means of a WMS make it possible to accurately control the goods and eliminate any potential errors.
Extremely strict organization of the warehouse has proven to be a very effective way to monitor the goods in real time. It also facilitates and speeds up the work of the operators.
The increased workload brought on by the pandemic has only served to confirm that this is the way forward. When the coronavirus pandemic is over, Intersurgical’s installation will continue to have modern, efficient operations, thanks to Easy WMS. The system will assist in the future with further automation, expansion and efficiency.
We installed Easy WMS to respond readily to the new demand requirements and to the market changes. This WMS allows us to take inventory in real time. This is vital, considering that we sell medical devices that need to be stored under specific conditions so as to guarantee their quality. With such rigorous inventory control, we can prevent mistakes and make sure that all standards are met.
Advantages for Intersurgical
- Full traceability: Easy WMS monitors Intersurgical’s 3,000+ SKUs. The WMS not only knows their exact location in real time, but also their logistics attributes, from the moment they arrive at the installation until they are dispatched.
- Effective warehouse organization: the facility is divided into areas with different operations. The objective of this layout is to eliminate interference that could result in mistakes.
- Leveraging of resources: the WMS optimizes all resources in the installation, including the goods, storage systems and the work of the operators to achieve maximum productivity. The ultimate goal is to provide more efficient service.
Warehouse of Intersurgical | |
---|---|
Warehouse management system: | Easy WMS |
Total No. of storage locations: | 5,927 |
No. of SKUs: | +3,000 |
Avg. No. of pallets received / day: | 175 |
Avg. No. of orders prepared / day: | 289 |
Avg. Nº of lines making up the orders: | 1,156 |
Gallery
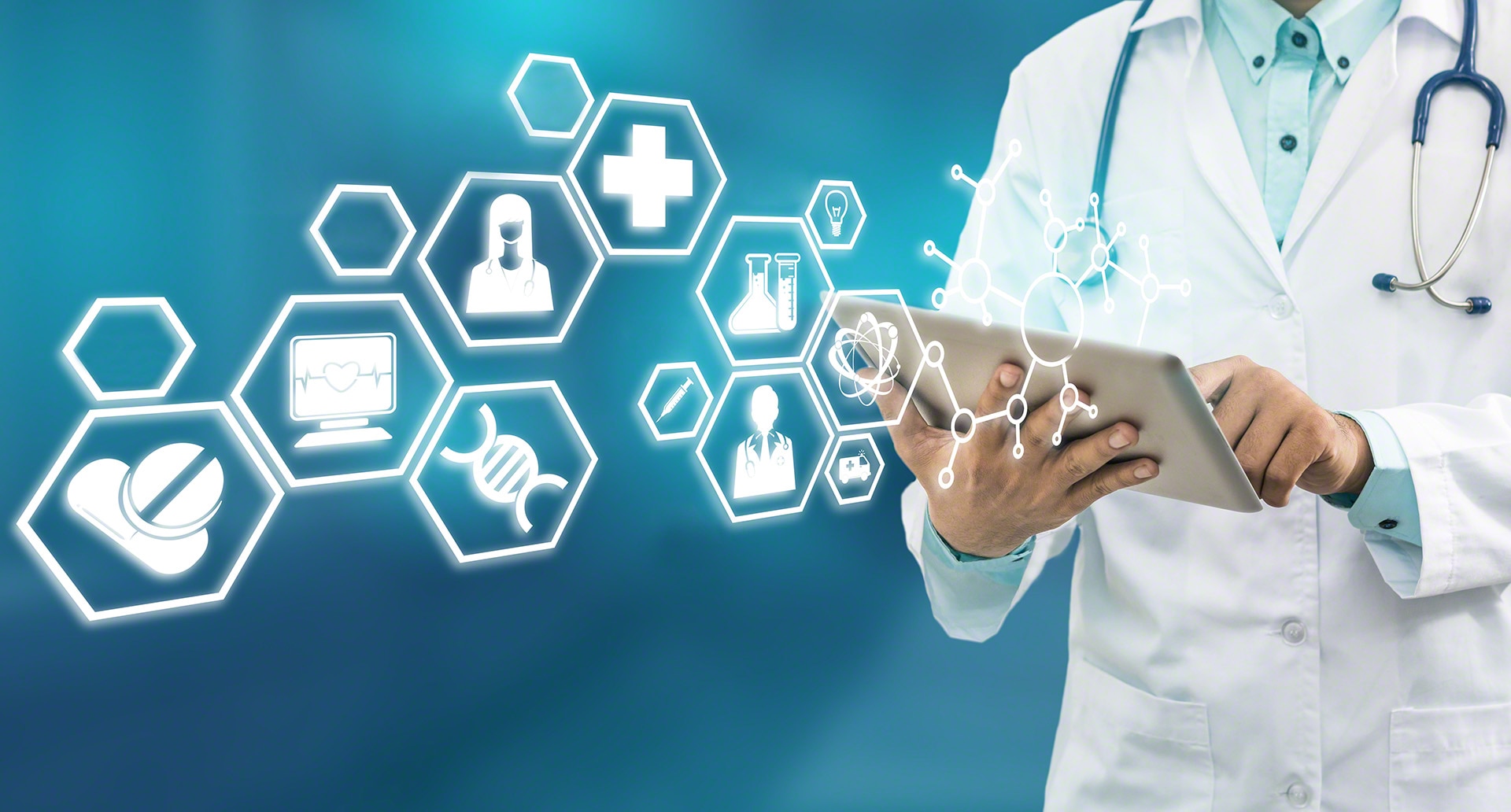
Respiratory care products at Intersurgical's installation
Ask an expert