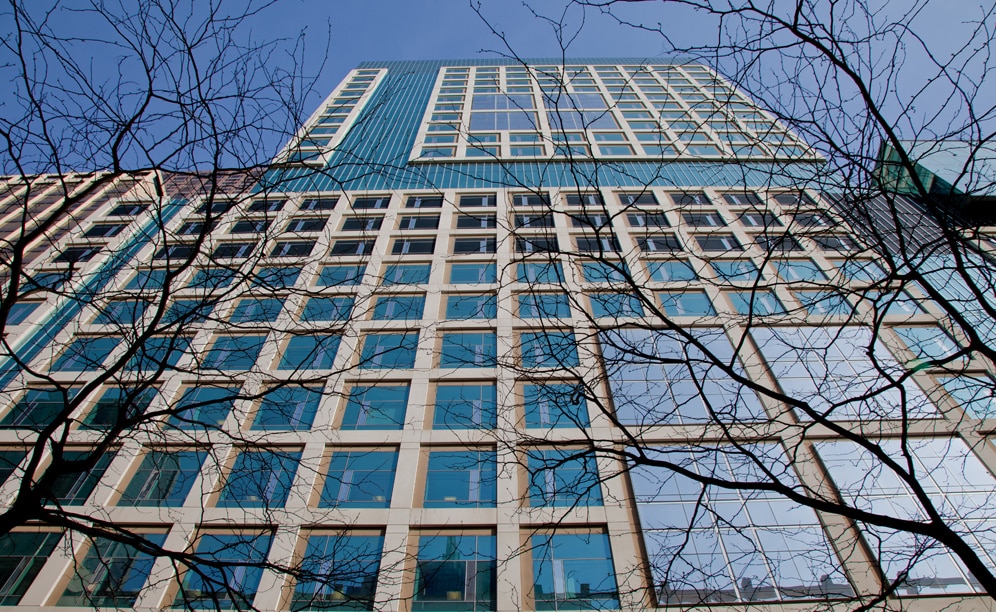
Interlake Mecalux installed Wide Span in Children’s Memorial Hospital
Children’s Memorial Hospital, the Ninth Floor at the Eleventh Hour
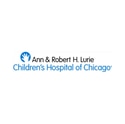
Children’s Memorial sat on a 6-acre plot for more than 130 years. The new hospital is a markedly more compact 1.8 acres. Time was of the essence as the ninth floor service center in the world’s tallest children’s hospital went from fragmented to functional in 21 days. The Interlake Mecalux team worked closely with the hospital’s procurement división and effectively saved material by using the room’s dimensions more efficiently. Requests are made through a sophisticated product tracking system, ensuring that whatever items were taken from the shelves today will be replaced tomorrow.
A group of distressed personnel unpacked boxes filled with I.V. fluids, bed pans, syringes, rubber gloves, and dozens of other medical supplies. The group was deliberate, almost frenzied. The entire floor, nine stories above downtown Chicago, was flush with building engineers. Particle board guided foot traffic and only a small number of security doors scattered around the hospital were being used. The central hub of this floor is called the service department. In fewer than 10 weeks, the 1.25 million-square-foot Ann & Robert H. Lurie Children’s Hospital would be a functioning cog in the Windy City’s healthcare cycle. In fewer than three weeks, this supply room would transform from the gaping space in the floor’s center to an operational concentration of service filled with almost 1,000 square feet of metal-decked shelving storing 1,700 different products. And in fewer than seven days, all of it would be expected to feed supplies to other parts of what would soon be the world’s fifth tallest hospital. The problem at this point was that there was very little on the shelves.
A Foot in Both Camps
Getting this room up and running wasn’t the only responsibility of the staff in charge. Several of the staff involved in the installation vented that as daunting as opening a new hospital can be, it’s nothing compared to doing it while also keeping the old hospital functioning. While the new 23-story, $915 million hospital was still being primped, the original children's hospital several miles away functioned normally.
Opening a hospital is a far more delicate process than opening most other facilities. Transferring goods from an old structure to a new one is stressful, but it pales in comparison to transferring patients. The added pressure showed on the faces of the personnel filling the Wide Span shelving inside of the service department.
And although it was close, the hospital’s supply chain staff, in concert with Interlake Mecalux, maintained its schedule and saw to it that every box along the process checklist was ticked on time. But while the checklists kept ticking, so did the countdown to the big opening. The new hospital, built on a relatively tiny 1.8-acre patch of land, is in the heart of downtown in one of the largest cities in the U.S. In its new location, Children’s Memorial works closely with the adjacent healthcare facilities including Northwestern Memorial’s state-of-the-art Prentice Women’s Hospital. The idea behind placing Children’s Memorial in such close proximity to Prentice was to provide, among other things, faster transport of critically ill newborns between the two facilities.
Wide Spanning History
To keep the operational pistons pumping smoothly, the service department runs on a dually capable manual and electronic requisitioning system called the Pyxis MedStation. When personnel from different parts of the hospital need supplies, they must make a request through the automated supply system. Pyxis maintains a minimum and maximum range for each product type stored on the shelves and replenishes items based on where in the range inventory falls. Requests are made at all hours of the day through the system, ensuring that whatever items were taken from the shelves today will be replaced tomorrow.
With turnover demanding such sophisticated product tracking, it was necessary to fortify each Wide Span bay with galvanized shelves. In addition to offering resistance-free product stacking and removal, the smooth shelves are also the easiest to clean – a necessity in a facility storing liquids.
Customers occasionally have a basic understanding of what storage solution is best for their space. According to Steve Zimmerman, the Midwest sales representative from Interlake Mecalux overseeing the installation, Children’s Memorial had more than done its homework. “Wide Span really is the best rack for hand-picking, and they knew that,” Zimmerman said. “We discussed the pros and cons with them, ensured they had the information they needed, and we all agreed.”
This was not the first time Interlake Mecalux had teamed up with the hospital. In 2006, two years before construction began on the new hospital, the consulting firm designing the room spaces throughout the building had to determine how the product would best be stored. Several vendors were reviewed and Interlake Mecalux won out. A hospital director closely associated with the service department’s development, who cannot be identified due to hospital policy restrictions, noted that the receiving dock at the old hospital had Interlake Mecalux shelving. The consultants charged with fortifying the new space with rack decided Interlake Mecalux rack was durable and could be cleaned easily. The Wide Span shelves would also maximize some of the height advantages the new hospital has over the old facility. Four-shelf systems were more prevalent in the old hospital store rooms, whereas each bay in the new hospital allows space for a fifth shelf.
Lowering the Roof
Mike Schiller, the corporate director of procurement at the new hospital, pointed to only one hiccup in the installation: the height of the ceiling. Early in the installation process, before any decisions had been cemented, personnel from both Children’s Memorial and Interlake Mecalux convened several times to look at the space and create a design plan. On these early occasions, the floor-to-ceiling height was near 16 feet, but none of the mechanical, electrical or plumbing components (MEP) necessary for a functioning room in the center of a high-rise had been installed. One personnel member present at those walk-throughs described, with a hint of hyperbole, the original ceiling height as resembling a cathedral and added that when she returned several weeks later, she was surprised by the change.
The HVAC system and lights had reduced the available floor-to-ceiling height by two feet. The building’s fire codes called for no less than 18 inches of air space between the sprinkler heads and anything else. By the time everyone involved in the installation understood what the final height would be on the roof, the 10-foot rack beams and frames had already been manufactured and needed to be refigured to accommodate the loss of space.
Zimmerman agreed that the changes to the room’s layout resulted in minor delays, but the ceiling wasn’t the only hurdle. He noted that the walls caused a momentary hyccup as well. “We didn’t have the exact dimensions of the room, and Children’s Memorial requested a few changes on installation day,” the sales associate said, recalling the effort. The Interlake Mecalux team worked closely and eticulously with the hospital’s procurement division and effectively saved by using the room’s dimensions much more efficiently. “ Initially, the design called for two rows going all the way back,” Zimmerman said, explaining that the row of Wide Span along the southern wall of the room would jut out two feet in order to avoid multiple load- bearing columns. The team’s solution was to push the frames against the wall and separate some of the bays by incorporating the columns. "It changed the number of beams and frames we needed,” Zimmerman said. “That’s why there was extra material.” Another smaller group of rack bays was shifted from the center of the room to extend across the west wall. This proved to be a vital alteration later on, after the receiving process started. Zimmerman said that the redesign was neither difficult nor time consuming. “ It actually worked out real well,” he said weeks later. “The manufacturing plant staff was flexible and the redesign only added an extra week to the delivery. We ended up cutting the beams down and installed [them] rapidly.” All involved concur that the installation was the easiest part of the process. Once the room’s dimension issues were resolved, all of the other pieces fell into place. Even the Interlake Mecalux installation crew drew kudos from the hospital personnel, who commended every aspect of their performance from their speed and timeliness to the fact that they were thorough enough to alert personnel if they were pausing for lunch.
Sitting By the Dock with Some Bays
The store room’s location on the ninth floor provides a centralized area for inventory control. Putting the mechanical and support services in the middle of the 23-story building allows more efficient service to the procedural and clinical care spaces in the lower portions of the building while still allowing economic service to patient care floors in the upper portions of the building. The drawback to this centralization, however, is there is virtually no space for any type of storage on the hospital’s ground floor loading dock. Schiller explained that the hospital’s ground level loading dock would serve as a pass-through for goods destined for the service department. The store room is located almost directly off the service elevators, a point, according to the procurement director, that was strategically located to make the transfer of supplies up nine floors simple.
The location of the department ensured that there would be as few turns of the service elevator as possible, saving time and eliminating opportunities for accidents to occur. Once inside the service area, the third of the store room closest to the service elevators is meant to remain bare and to function as the central supply and receiving dock. This is why the switch in rack layout to create more space was so important. Without the extra space, the receiving area would have been much smaller.
When the SKUs are shipped and unloaded in the hospital, one of the supply chain team members moves the pallets from the ground floor to the ninth. Once the shipment finds its way to the service department’s receiving area, the fast-moving items with low units of measure are placed on the shelving bays closest to the room’s receiving area, while the bulk box storage items are tucked farther away. The pallets of products are widely mixed as the Pyxis machine only fulfills according to what was used the day before. Rarely is a full pallet of the same product ever ordered. If one specific item is normally packaged in a case of 80, the hospital might receive 30.
As the hospital’s grand opening approached, Children’s Memorial was grateful for every break it could get. Luckily Interlake Mecalux has a manufacturing plant just minutes away. This made adjustments like shaving 2 feet off 10-foot beams almost a non-existent issue. “It really helps us in this whole geographical area,” Zimmerman adds on his way to another installation. He pauses and the suggestion of a grin crosseshis face. “ Our biggest problem is that our rack is too durable. They never need to replace it.” At least not until Chicago builds another hospital.
Storage solution, Wide Span | |
---|---|
Number of 5-shelf Wide Span bays: | 49 |
Total square footage of facility: | 3,800 sq. ft. |
Total square footage of shelving: | 980 sq. ft. |
Total product capacity: | 1,700+ |
Weight capacity per shelf: | 1,985 lbs |
Weight capacity per beam: | 8,952 lbs |
Space between shelf levels: | 20 in. |
Gallery
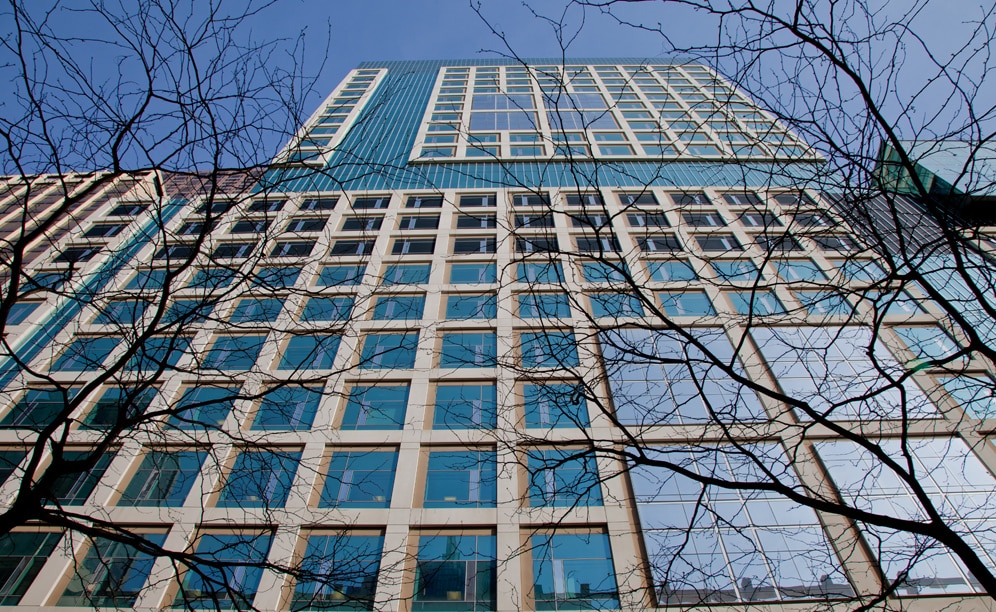
Children’s Memorial sat on a 6-acre plot for more than 130 years. The new hospital is a markedly more compact 1.8 acres
Ask an expert