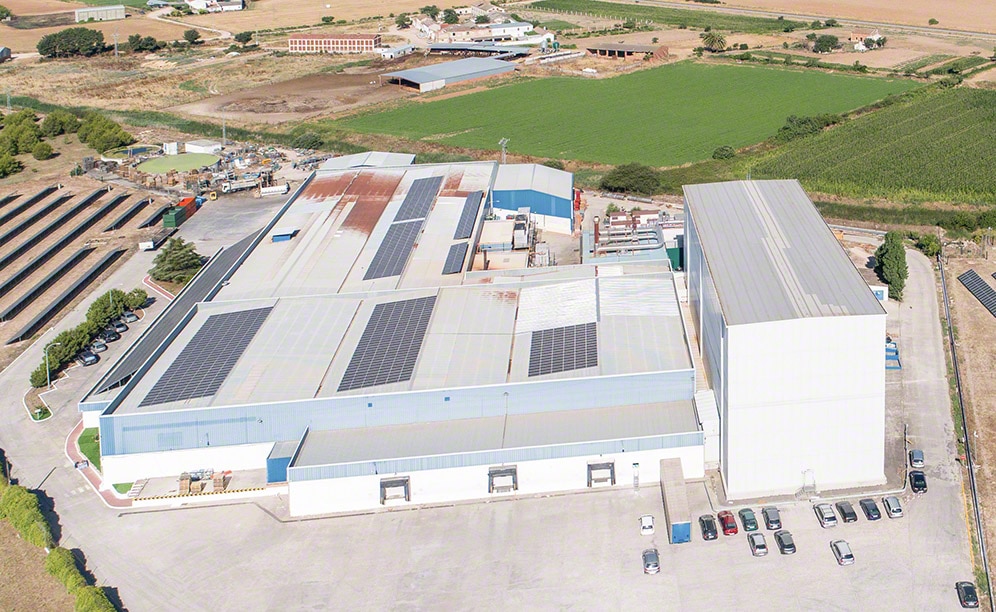
Automatic and semi-automatic systems to store frozen vegetables
Comagra de Congelación renovates production centre with a rack supported warehouse and two Pallet Shuttle run chambers
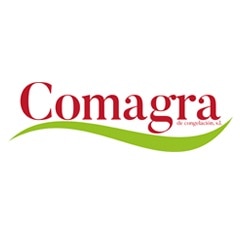
Comagra de Congelación, one of the largest frozen food companies in Spain, has recently expanded its production center in Alberche del Caudillo (Toledo) by collaborating with Interlake Mecalux. For this redevelopment, the company has benefited from advances in technology to increase the productivity of all its operations. Interlake Mecalux erected an automated rack supported warehouse and equipped two traditionally built installations with the semi-automatic Pallet Shuttle system. These solutions have reduced operating costs and helped the company offer fast, efficient customer service.
Internationally recognized broccoli and peas
Comagra de Congelación, founded in 1983, is a driving force in frozen vegetable production in Spain. In recent years, it has achieved unprecedented expansion, and 85% of its produced goods are exported to five continents. Although it carries a very diverse range of frozen vegetables (potatoes, cauliflowers, carrots, onions, etc.), broccoli and peas are its most globally-known flagship products.
Comagra de Congelación runs its production center in the small village of Alberche del Caudillo, only 87 miles from Madrid. From a logistics standpoint, its location is unbeatable. Fantastic transportation routes connect it to the ports of Lisbon, Gibraltar and Valencia, which speeds up the distribution of goods in Europe, the United States, Africa and Asia.
“Initially, the Comagra de Congelación factory in Alberche del Caudillo had two manually run frozen-storage chambers with three-level high drive-in pallet racks and space to accommodate ten pallets deep,” explains Cristian Portalatín, head of the company's Production Department.
Since its grand opening, the center has been under constant expansion and modernization, adapting to new consumer trends and the increase in sales achieved by the company. “In an ever-competitive market, growing in volume is crucial to place us on the same footing as other European manufacturers. Here is where the efficiency of good storage becomes the linchpin, so the whole system runs smoothly, from the fields to warehouse logistics.”
Cristian Portalatín - Production Department Manager at Comagra de Congelación
“We are very satisfied with the performance of our warehouses. All our planned objectives have been met since the startup stage. And, most importantly, we have not had any setbacks, and everything has run as expected.”
The automated rack supported warehouse
When it comes to reworking its logistics center, the company has always depended on the collaboration and expertise of Interlake Mecalux. In this instance, the company knew very clearly that an automated solution was the key “to have comprehensive control over our goods and have a handle on any and all in-warehouse movements.”
Tracking merchandise is a top priority for this company “Comagra de Congelación holds international quality certifications such as the IFS and BRC, meaning all these food safety requirements make any sort of manual control inefficient, insufficient and involve a huge workforce, with poor results,” noted Cristian Portalatín.
In 2005, Interlake Mecalux built an 82' high automated rack supported warehouse next to the two traditionally erected chambers. This single-aisle installation can hold up to eight pallets deep due to a stacker crane that runs between the two blocks of laterally placed racks. Overall, about 120 SKUs and more than 5,400, 32" x 48" pallets are stored, each with a maximum weight of 1,764 lb.
Daily workflows include an average of 150 incoming pallets from production and another 120 pallets shipped out of the center. Warehouse operations are automatic and do not require workers to slot and remove unit loads from their corresponding locations. According to Cristian Portalatín, “It is a stable system that requires little to no large-scale maintenance servicing. It doesn’t cause problems or breakdowns during day-to-day labor. It is completely reliable and, owing to its robustness, completely safe.”
The stacker crane picks up pallets and moves them to the location assigned by the warehouse management system. Once there, a Pallet Shuttle rolls along the inside of the channel and deposits the load in the first open location.
Two freezer stores with the semi-automatic Pallet Shuttle
Recently, the company asked Interlake Mecalux to reorganize two already constructed frozen-storage chambers to gain needed storing capacity to fulfill increased production and to speed up storage tasks. The challenge was that “the chambers were encased with panels, as was the outside of the built structure and the ceiling's upper trusses, meaning any modification would require an excessively large investment.”
Interlake Mecalux proposed equipping the two installations with the semi-automatic Pallet Shuttle system because “it adapts perfectly to the sparsely available height.” Plus, this solution gives the company the upper hand so “we always have stock under control and enjoy quick access to them,” points out the production department manager of Comagra de Congelación.
The two installations comprise a central 108' long aisle and two blocks of 23' high racks, with three storage levels. Altogether, a 2,334-pallet storing capacity is achieved.
Operators use Wi-Fi connected tablets to give commands to the Pallet Shuttles. “It is so easy-to-use, which makes quick work of training and user proficiency,” explains Cristian Portalatín. In addition, when operating at a steady -4 °F, tablets mean operators can “control the automatic shuttles without getting out of the forklift.”
Advantages for Comagra de Congelación
- Control of the merchandise: control over its goods is a priority for Comagra de Congelación, as it works with frozen foods. The automatic solutions that Interlake Mecalux has put into place offer total traceability on a daily basis.
- Maximum storage capacity: the rack supported warehouse and the Pallet Shuttle system in the two freezer stores take advantage of the available space, providing storage capacity for more than 7,800 pallets (adding all three facilities together).
- Streamlined operations: within high-density systems, the Pallet Shuttle system offers the greatest dynamic workflows for pallet inputs and outputs. It moves a total of 540 pallets every day among all the frozen-storage installations.
Rack-supported warehouse | |
---|---|
Storage capacity: | 5,490 pallets |
Pallet size: | 32" x 48" |
Max. pallet weight: | 1,764 lb |
Warehouse height: | 82' |
Warehouse length: | 190' |
Working temperature: | -4 ºF |
Gallery
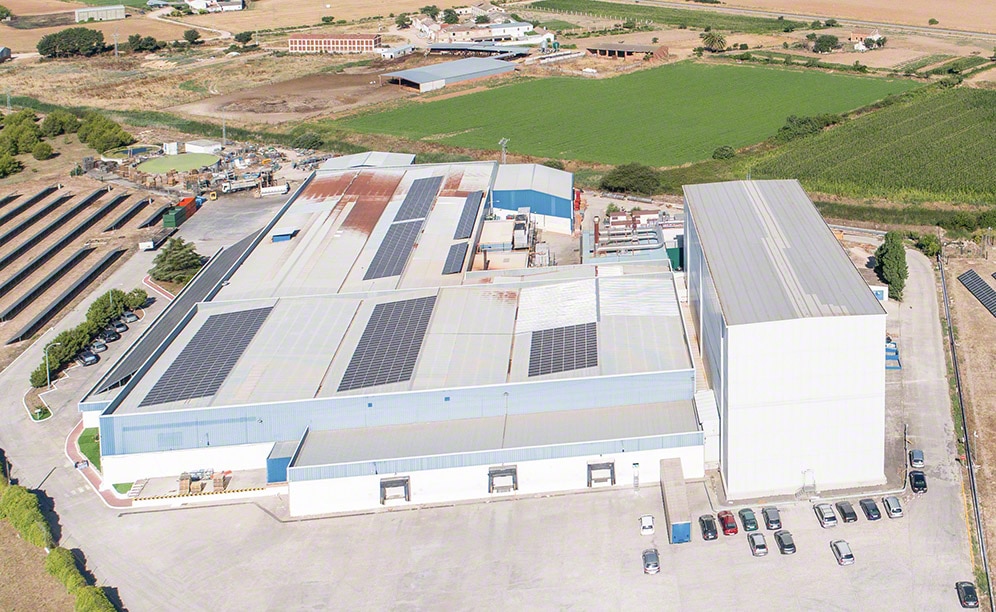
Automated clad-rack warehouse of Comagra de Congelación
Ask an expert