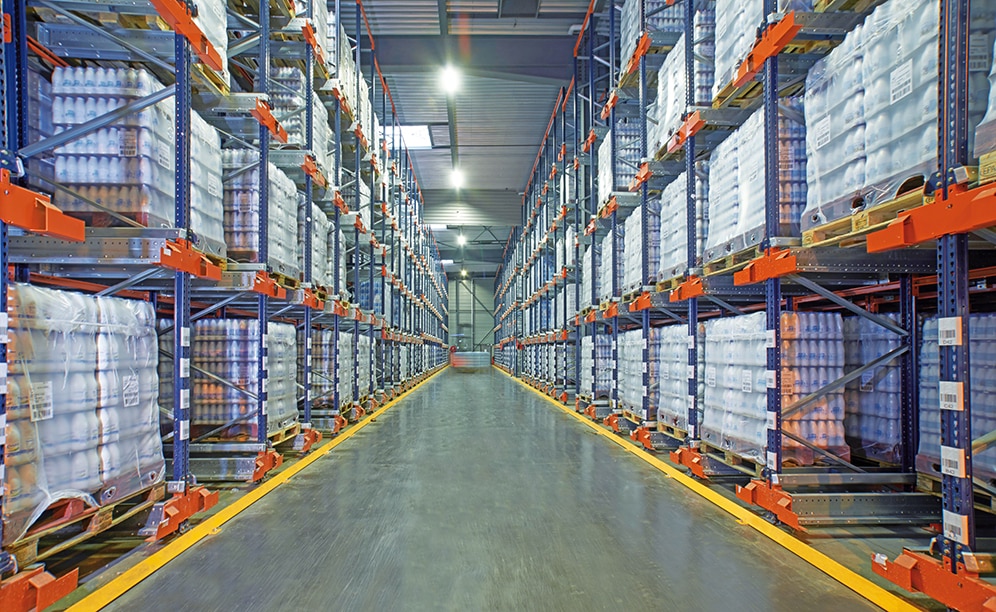
The dairy producer SLVA manages the handling and storage of more than 7,400 pallets with nine Pallet Shuttles in up to 20 m deep channels
The Pallet Shuttle system: an ideal milk storage solution for SLVA
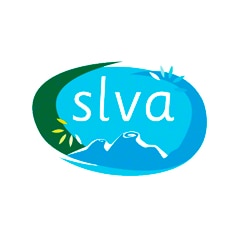
SLVA, a company that produces and delivers milk in France, relies on a semi-automated high-density system served by Pallet Shuttles to manage the goods located in its Theix installation. This solution, which can store approximately 7,500 pallets, is perfect to achieve high storage capacity while increasing workflows.
About SLVA and its needs
SLVA (Société des Volcans d’Auvergne Laitière) is a French company that produces and supplies high-quality milk to different brand distributors. The company, created in 2007, processes a large quantity of milk stored in its logistics center in Theix, near Clermont Ferrand. To manage such a production volume, SLVA required a warehouse that offers high workflow speeds of incoming and outgoing pallets and, in turn, would provide large storage capacity in a small space.
Racking served by Pallet Shuttles
SLVA has a facility with an approximate 43,056 ft2 area, and is 29.5’ high, 253’ long and 172’ wide. Three blocks of high-density racks of different depths were enabled to maximize space around the premises, separated by two access aisles, to deposit processed milk into cartons and bottles. The storage area occupies 30,451 ft2, allocating the rest of the warehouse to the goods dispatch and reception zone.
The racks are served by nine Pallet Shuttles, a high-density storage system designed to optimize the movements of loading and unloading pallets and to stop forklifts from having to enter into the storage aisles. This solution enables storage of different SKUs in each bay (one per channel) and the possibility of having the same SKU in several different channels to increase the actual capacity.
With a height of 29.2’ and a length of 177’, the racks can house 7,424 pallets weighing up to 1.1 t each. The load levels of each rack vary depending on the pallet height that is used: type A (31.5” x 47” x 53”) and type B (31.5” x 47” x 61”). All racking blocks work via the LIFO management system, so inputs and outputs take place on the same side. The blocks are divided taking into account the turnover rate of the products:
- Block 1: the block with the greatest surface in the SLVA warehouse has been reserved for high consumption products. With a capacity for 3,792 pallets, racking channels measure 69’ long and deep store 24 pallets.
- Block 2: it has a capacity for 3,158 pallets. Being located in the center of the warehouse, storage channels face two working aisles so that each side is considered a separate channel. Channels, 61’ long, have been divided into two aisles of 10 pallets deep each.
- Block 3: it is the smaller and shorter block of the warehouse. In these racks, 474 pallets with lower consumption products are deposited. Each channel measures 9.2’ long, and three pallets deep per level can be introduced. The blocks are separated by a working aisle of approximately 16’, more than sufficient width so that operators can move and work with several forklifts at the same time.
Semi-automated Pallet Shuttle: operations
- Operators use a reach truck to place the motorized shuttle into the channel where the pallet will be stored.
- Then, the pallet is placed at the entry level, resting on the rails.
- The Pallet Shuttle raises the pallet with the goods slightly so it can move the pallet along the channel.
- Once raised, the shuttle shifts the load to the first free location in depth.
- When the pallet is unloaded, the shuttle returns to the start position to repeat the movement with the next pallet
This sequence is repeated as many times as necessary to fill the corresponding channel. Regarding pallet extractions, the shuttle performs the same operation but in reverse.
One tablet to control the Pallet Shuttle
Pallet Shuttles move all autonomously through the channels and follow the instructions the operator specifies from a tablet connected to a Wi-Fi network. The tablet is fixed directly to the protective structure of the forklift to improve the ergonomics of the operator during use.
The Mecalux control tablet incorporates a very intuitive, secure and easy to use software from which the operator can control any of the shuttles inside the installation without interference. In addition, the tablet user can select the type of pallet they want to handle, determine the number of pallets to be extracted, count the number of pallets stored in the channel, activate the additional locking system, etc.
Racks adapted to the building
The racks of the SLVA warehouse have 4 or 5 levels, depending on the height of the pallet to be stored.
Four level high racks were set up right where the racking coincides with pillars and roof beams to optimize the warehouse volume. Thus, they combine different pallet heights to eliminate dead spaces and better use the entire surface of the warehouse.
Safety system
The entire height of the racks is protected with mesh that blocks access to the channels and prevents any loose box from falling into work or passageway areas.
Safety enclosures were also installed on both sides of the inner aisles (used as emergency exits) and protected on top by metal mesh. The frontal protection of the racks indicates the boundary the operator can bring the forklift up to when handling the Pallet Shuttle or the pallets and prevents blows to the racks. Lateral protections safeguard safety enclosures from potential impacts.
Advantages for SLVA
- Maximization of space: the SLVA warehouse can store a total of 7,424 pallets in an area of 30,451 ft².
- Many more cycles/hour: the use of Pallet Shuttles ensures greater movements of pallets.
- Top-notch safety: the storage system itself and the incorporation of safety devices reduce the risk of accidents and ensure proper maintenance of both the goods and the installation.
SLVA warehouse, France | |
---|---|
Storage capacity: | 7,424 pallets |
Pallets of 31.5” x 47” x 53”: | 3,360 |
Pallets of 31.5” x 47” x 61”: | 4,064 |
Max. weight per pallet: | 1.1 t |
Max. racking height: | 29’ |
Max. racking length: | 177’ |
No. of Pallet Shuttles: | 9 |
Gallery
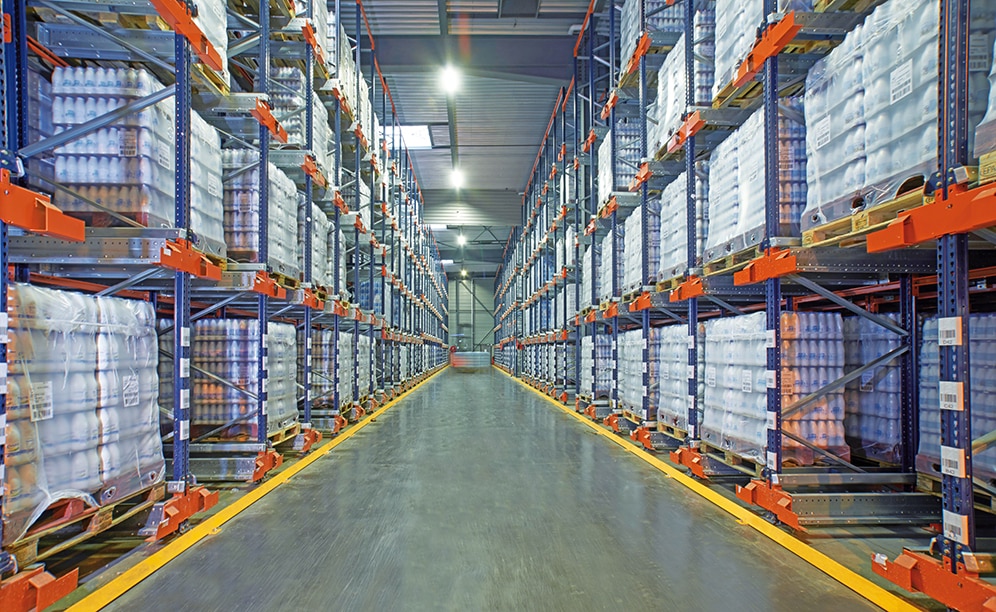
The SLVA warehouse can store a total of 7,424 pallets in an area of 2,829 m²
Ask an expert