
Selective pallet racking with wire shelves and a conveyor circuit multiply picking efficiency in a major toy manufacturer
The Atosa distribution centre in Marseille increases its picking productivity
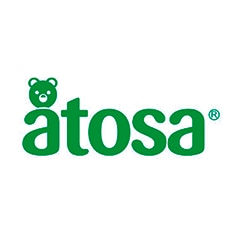
Atosa, a leading family business who makes toys, commissioned Interlake Mecalux to equip its logistics center in Marseille (France). The installation has selective pallet racking, as well as a sorting and order consolidation area that streamline operations being carried out. With this solution, the company can grow at an expected pace and serve its customers in central Europe faster.
About Atosa
Atosa is one of the oldest and most innovative toy makers in its sector, who started doing business in Spain in 1969.
Throughout its history, the company has not stopped expanding and has established itself as a quality, prestigious brand internationally.
Currently, it distributes toys to several European countries. Likewise, it devotes its resources to develop and diversify its product portfolio to avoid the seasonality that is typical in this sector, by incorporating school supplies, costumes, Christmas items, beach products, gifts, etc.
Since its founding, Atosa has always relied on the knowledge and experience of Interlake Mecalux to resolve its logistics needs and make its expansion projects a reality.
The warehouse in France
Atosa constructed a new 2.32 acre logistics center in Marseille (France), a well connected city that has an extensive network of highways, a port, an airport and railway services.
The firm asked for Interlake Mecalux’s advice to find a solution that would bring together a large storage capacity for all its products and speedy picking.
The warehouse is sectored into two separate 1.61 acre cells, each with specific functions and distributions:
- Storage area, set aside to house Atosa products.
- Order consolidation and package closing.
- Dispatches and preloading.
- Future expansion, considering the growth of the company.
Selective pallet racking
The company works with a variety of different, lightweight box sizes that are placed directly on the shelves, without using pallets.
Interlake Mecalux equipped the warehouse with selective pallet racks, noted for their versatility in adapting to a wide variety of SKUs of distinct sizes, turnovers and volumes. At the same time, they offer direct access to products, which is essential for Atosa because this facilitates picking tasks. Levels have mesh shelves, which have sufficient load capacity for the goods to be deposited safely.
The Atosa installation has an advanced fire detection and extinction system, which includes smoke detectors and other control devices that turn on in the affected area if necessary.
Automatic sprinklers are distributed strategically inside the racks, bearing in mind the fire load, i.e., according to the fire risk present in the different warehouse areas.
The racks are 133' long. For this reason, there is an underpass set up that cuts across the rack installation and serves as the emergency exit. The bays on top of the emergency underpass are covered in mesh shelving to avoid material from accidentally falling there.
Emergency evacuation aisles were provided in compliance with the safety regulations in force in the country. The lateral racking located next to this is protected with mesh, which covers all levels.
Picking
Operators use high-reaching order picking machines to handle the goods, either to select the products for orders or to replenish stock during two different time slots. These pieces of equipment have a cabin, where the operator works from, and which raises and lowers with the load. This creates greater maneuverability when accessing the boxes.
Operators extract the needed boxes from the shelves and then move them in a cart to the order consolidation and classification area. Orders served in full boxes are validated and can go directly to the preloads area. However, a large part of the orders at Atosa is single product requests, and this means splitting boxes. For this reason, the company has enabled a specific area near preloads, since it is where orders are finalized for their subsequent dispatch.
Interlake Mecalux has installed a circular conveyor circuit that branches into three channels, allowing maximum efficiency in organizing products according to their origin and destination. The products, which are deposited in containers labeled with a barcode, move automatically to the three channels. Then operators distribute the goods in boxes and pallets, sorted by customers or shipping routes.
Advantages for Atosa
- Best use of surfaces: sectoring the warehouse has allowed optimal storage capacity and the picking of orders in the same space.
- An integrated warehouse: the two cells that comprise the warehouse, with different distributions and functions, are connected to each other with the same objective, to expedite picking.
- Speedy order preparation: the logical distribution of the warehouse and the installation of selective pallet racking facilitate operator access to any product.
Selective pallet racking of Atosa warehouse | |
---|---|
Storage capacity: | 312 pallets |
Picking levels: | 2,400 |
Racking height: | 30' |
Racking length: | 133' |
Aisle width: | 5' |
Gallery
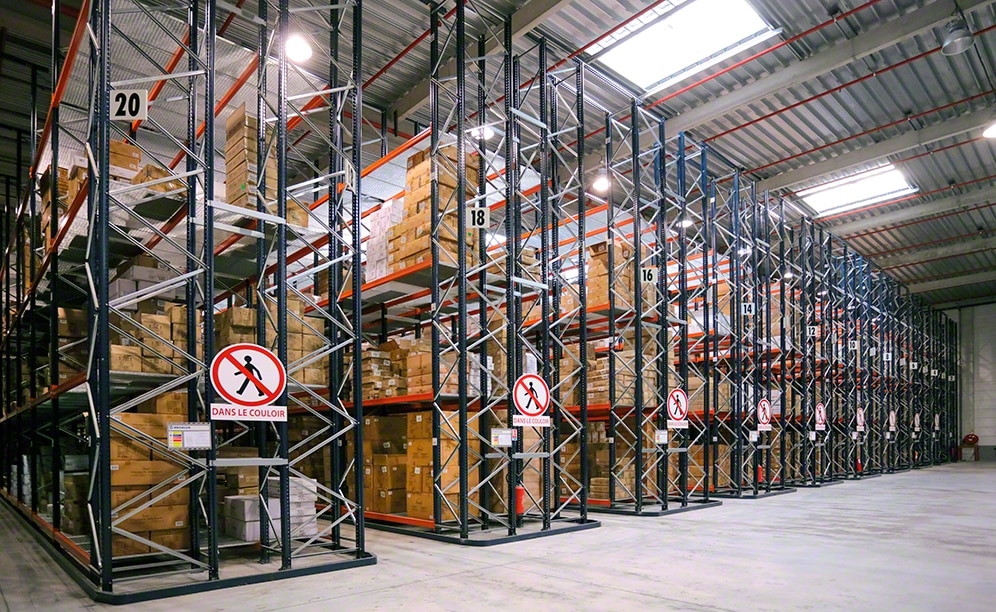
Mecalux equipped the warehouse with pallet racks, noted for their versatility in adapting to a wide variety of SKUs
Ask an expert