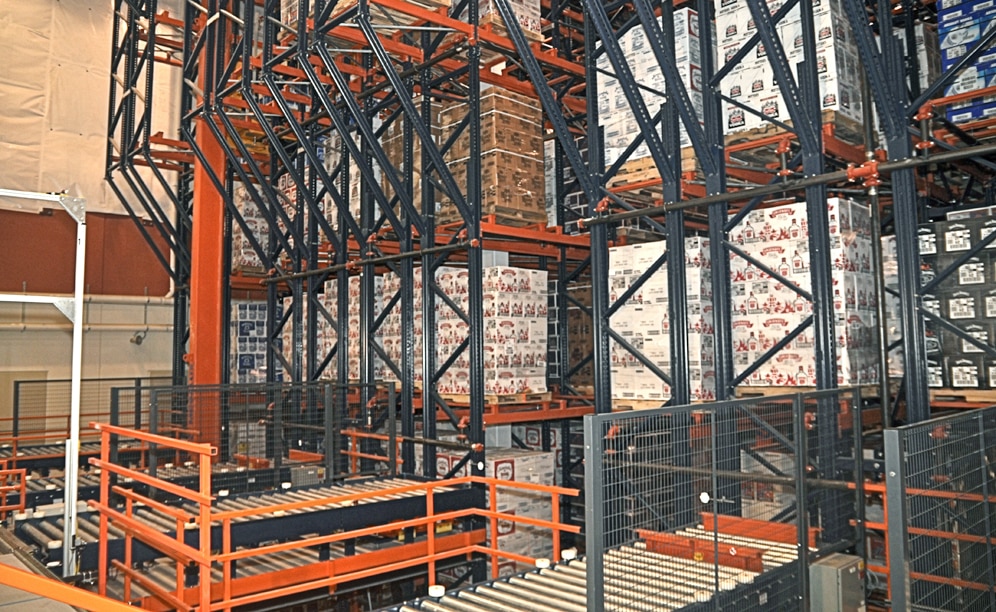
Raising the Bar in Boise: Mecalux Constructs Comprehensive AS/RS Pallet Racking Solution
The ISLD toasts the success of their new Interlake Mecalux unit load Automated Storage and Retrieval
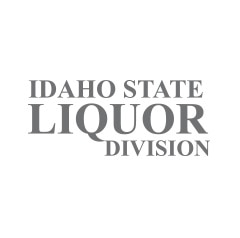
After experiencing 114% growth in twelve years, the Idaho State Liquor Division (ISLD) warehouse and distribution center in Boise was bursting at the seams. The old way of managing their inventory was not working for them anymore and they had to find a new, more effective storage solution. The Interlake Mecalux unit load Automated Storage and Retrieval System (AS/RS) provided the storage they needed now and in the future.
Customer’s Needs
When the Idaho State Liquor Division moved into their new 55,000 ft² Boise distribution center in 1998, they were confident in the facility’s capacity to accommodate any increase in demand over the next few years. Higher population coupled with a consumer shift to premium liquor brought the ISLD to a point where they had to manage their inventory better or find a new, larger facility.
Additional space was needed as suppliers frequently produced new or improved spirits. Moreover, with a growing number of liquor manufacturers, the number of spirits products produced could grow exponentially. As a result, the ISLD team determined they needed to increase storage density. “We had to automate, we had to modernize,” said top management. This conclusion led the ISLD team to look into automated warehouse options, “We needed to improve our effectiveness, improve our layout and to touch product less often.”
Although the ISLD team initially wanted to expand the warehouse outward with a uniform height ceiling, after seeing AS/RS Pallet Racking in action, they realized it was time to do something different and build up.
Mecalux’s Proposed Solution
A single solution stood out from the rest, the one from Interlake Mecalux (IKML). The ISLD felt the Interlake Mecalux plan was superior because it was closely aligned with their original vision for the warehouse. Three factors from the Interlake Mecalux proposal made IKML the clear front runner: the capability of the AS/RS system, the automated product management, and the price. Not only did their design manage the needs of ISLD at the pallet level, but it provided a solution at the case picking level as well. Their newly installed AS/RS Pallet Racking supplied high-density storage in a smaller footprint with room for many years of growth.
The ISLD team decided to improve their storage capacity for palletized product by building upward instead of expanding outward installing the Interlake Mecalux AS/RS Pallet Racking in a warehouse expansion of only 17,200 ft². They worked with the IKML team to design an AS/RS that complemented the existing manual warehouse operation. This provided the ability to store and retrieve pallets for case and split-case replenishment. The new AS/RS fully utilizes the 51’ high warehouse addition by adding nearly 3,000 pallet storage locations.
These pallets are received at one of the facilities’ three docks and either taken directly to the new AS/RS or to the Pallet Racking storage for full case picking. For entry into the AS/RS Pallet Racking, lift trucks transport pallet loads to an induction station conveyor. Sensors within the station automatically weigh and measure each pallet. To improve safety and product security, pallets are also scanned to determine tolerance. Pallets that are loaded improperly or damaged are diverted for repair or adjustment. Most pallets though are deemed acceptable and conveyed to one of the three 160’ long aisles of the AS/RS. Servicing each lane of the system is a high speed, double-mast, double-deep stacker crane.
The 50’ tall stacker cranes are automatically summoned to gather any pallets diverted to their lane for put away. Moving at speeds of nearly 10’ per second and lifting speeds of nearly 4’ per second, the cranes swiftly and securely place products in the double-deep rack. The movements of each crane are precisely controlled by Mecalux’s Galileo software ensuring the pallet arrives at the appropriate picking station.
The primary output station is located near the case picking area. Full case picks are directed by a voice system and placed onto pallets. A secondary output station is located on the mezzanine level servicing split-case picking. When a stacker crane delivers a pallet to this station, a worker is given instructions on a computer screen to pick a required number of cartons. The cartons are removed from the pallet, labeled and placed onto the split-case conveyor supplied by IKML. Once the required cartons have been removed from the pallet, a stacker crane returns the pallet to the AS/RS Pallet Racking for storage.
Not only will the comprehensive system provide for future growth without needing to increase labor, but it will also increase the building’s safety, productivity and reduce product damage.
Advantages for the Customer
The Idaho State Liquor Division has nothing but praise for the team from Interlake Mecalux that brought the ISLD AS/RS Pallet Racking from inception to reality. This system offers:
- High-density Storage: upgrading from 350 SKUs to around 1200 SKUs allows the ISLD to reduce the number of full cases that are shipped and stored at the retail outlets.
- Full Product Control: Easy WMS allows Galileo control software to facilitate the movements of the crane ensuring the pallet arrives at the appropriate picking station.
- Enhanced Picking: voice picking system directs each worker to select the appropriate bottles from the flow racks and place them into the cartons. The split-case conveyor supports the picking of individual bottles into mixed cartons.
- Safety Devices: sensors within the station automatically weigh and measure each pallet. To improve safety and product security, pallets are also automatically scanned to determine tolerance. Pallets that are loaded improperly or damaged are diverted for repair or adjustment.
- Consolidation: once the cartons from the split case area arrive on the main level, they are consolidated with any necessary full case orders and staged for shipment.
AS/RS Pallet Racking for Idaho State Liquor’s Warehouse | |
---|---|
AS/RS Warehouse Addition: | 17,200 ft² |
Rack Length: | 160’ |
Rack Height: | 51’ |
Aisle Width: | 5’-11” |
No. of Additional Pallets: | 2,740 |
Pallet Weight Capacity: | 2,800 lb /pallet |
No. of Load Levels: | 7 full levels, 3 cantilevered levels at the front end |
Load Unit: | GMA pallet (40” x 48”) |
No. of Stacker Cranes: | 3 double-mast, double deep |
Stacker Cranes: | Lifting speed: 216.53’/min - Travel speed: 590.55’/min |
Forks Speed: | 98.4 – 196.8’/min |
Main Conveyor System: | Split-case |
Gallery
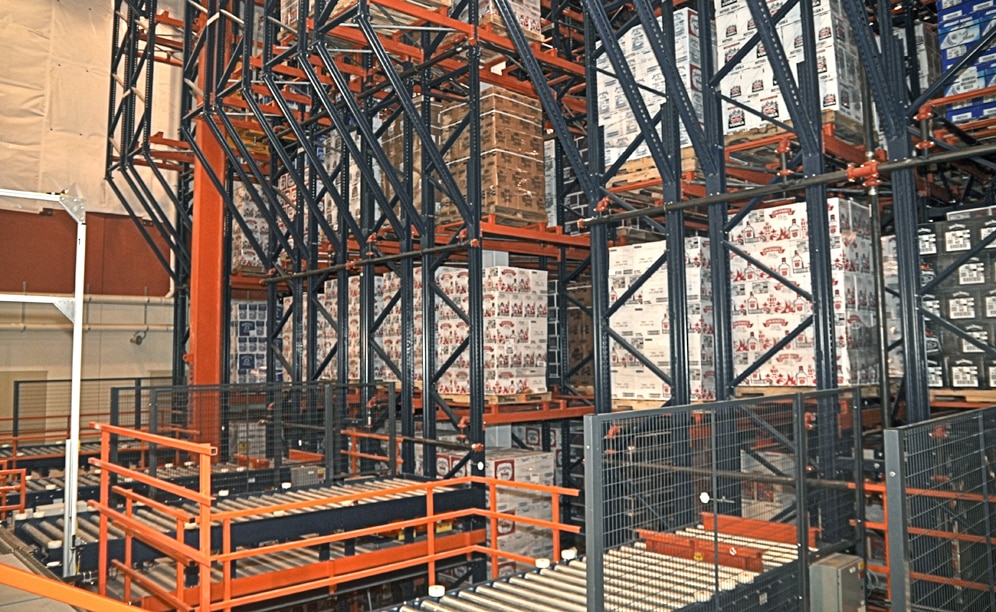
The new AS/RS fully utilizes the 51’ high warehouse addition by adding nearly 3,000 pallet storage locations
Ask an expert