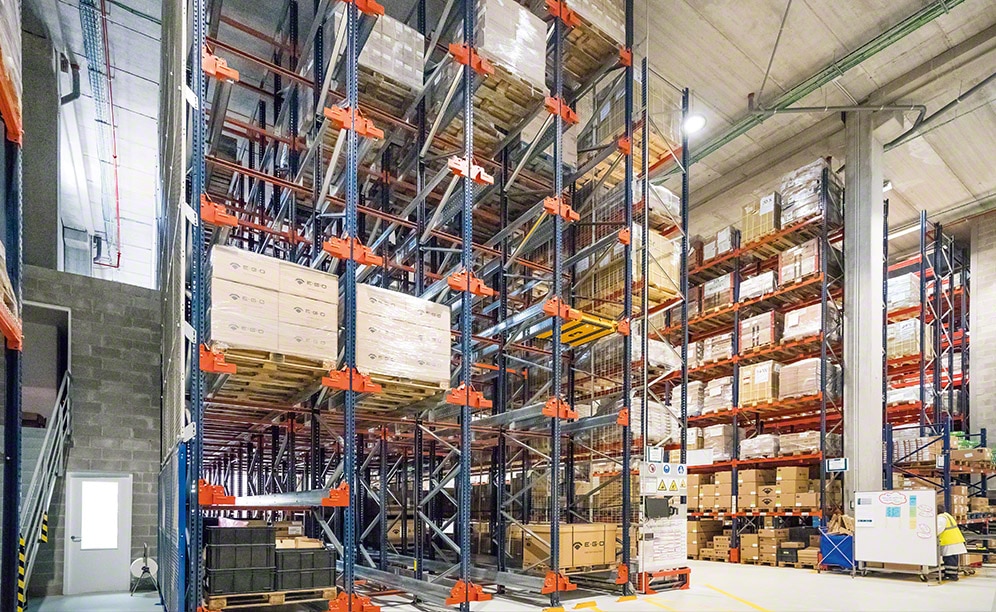
EGO Appliance Controls: a three system combo maximizes productivity
The triple storage system makes the most of the available storage area in the warehouse of EGO Appliance Controls
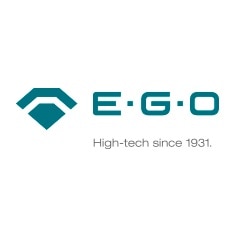
EGO Appliance Controls obtained a solution tailored to its needs in the warehouse it owns in Lliçà de Vall (Barcelona). Interlake Mecalux equipped the facility with the high-density Pallet Shuttle system, two blocks of Movirack mobile racks and selective pallet racking.
About EGO
Founded in 1931, EGO has built up a specialized business model that includes, among other things, control components and engine management systems for domestic and industrial devices like washing machines, clothes dryers and dishwashers. Its business dealings also extend into other applications, such as for kitchens and refrigeration, as well as household, industrial and business settings. Currently, it sells more than 20,000 different products in 16 countries.
Three storage systems
The storage space EGO owns and operates in its center in Spain was a tight fit when faced with growing demand. The business required more capacity without a drop in operating speeds. Likewise, it was crucial to keep the wide variety of products available, as well as its multiple high, medium and low turnover SKUs.
Interlake Mecalux has supplied two compact storage systems in EGO’s warehouse: a block with the semi-automatic Pallet Shuttle for consumer products and another two Movirack mobile racks, one in front of the other, for medium and low consumption products.
At the same time, it made use of the aisle created between the two blocks by installing pallet racks there.
Pallet Shuttle system
The 883 ft2 block with the semi-automatic Pallet Shuttle system comprises 25 channels that are 46' long and able to store 16 pallets deep. Overall, the storage capacity is 448 pallets of 32" x 48" with a 1,100 lb unitary weight. To store the goods, the operator places the electric shuttle in the corresponding channel by means of a reach truck. Next, he or she sets the pallet in the channel’s entry point, and the Pallet Shuttle moves it to the first open location. The shuttle returns to the home position in order to repeat the operation with the next pallet.
This sequence is repeated as many times as needed. The same process is carried out in reverse from the opposite side of the block of racks to remove the goods. This block of racks operates with the FIFO criterion (first in, first out), in other words, the first pallet to enter is the first to leave.
Goods slotted into one side of the aisle are extracted from the other side, obtaining excellent turnover and preventing interference between the loading and unloading of the pallets.
The tablet
Operators run the automatic shuttles via a Wi-Fi connected tablet. This tablet has a very intuitive software that does not require specific training and can carry out multiple applications and functions, including:
- Uninterrupted loading and unloading of channels.
- Automatic stock keeping of the number of stored pallets.
- User management and authorized personnel.
- Activation of the locking system, which enhances the bond between the Pallet Shuttle and the handling equipment’s forks and prevents it from accidentally falling.
Movirack mobile racking
Two blocks of Movirack mobile racks are installed in which the company houses 1,680 pallets of 32" x 48" with a maximum 1,100 lb unit weight. Each block consists of three, double-depth racks on mobile bases down the center and two stationary racks at the ends. This high-density system is a game changer, as far as space goes. It compacts the number of aisles, as well as eases direct access to the goods when the corresponding work aisle opens.
Both blocks run automatically. The operator sends the required open aisle command through an RF remote control to extract or deposit the goods, and to also pick directly from pallets located on lower levels. To ensure the safety of the goods and, above all, of the operators, the Movirack system includes optoelectronic devices or light curtains, longitudinal photocell sensors placed bilaterally on the bases, as well as emergency stop and reset buttons.
Selective pallet racking
The four blocks of selective pallet racks can accommodate 287, 32" x 48" sized pallets. Each pallet can weigh up to 1,100 lb. It is a very versatile system, which adapts to any unit load type, able to house heavy pallets and those with variable volumes.
Direct access to products streamlines the management of goods and order picking. Reach trucks are the primary handling equipment operated in this warehouse to insert and extract pallets from their locations.
Advantages for EGO Appliance Controls
- High storage capacity: the triple storage system makes the most of the available storage area, thus achieving an overall 2,415 pallet capacity.
- Adaptable to many different products: the combination of three systems eases the sorting of a huge variety of products according to their characteristics and turnover.
- Safety first: the storage system includes safety devices that ensure the installation runs smoothly and safely.
Pallet Shuttle system | |
---|---|
Storage capacity: | 448 pallets |
Pallet size: | 32" x 48" |
Max. pallet weight: | 1,100 lb |
Max. rack height: | 36' |
Gallery
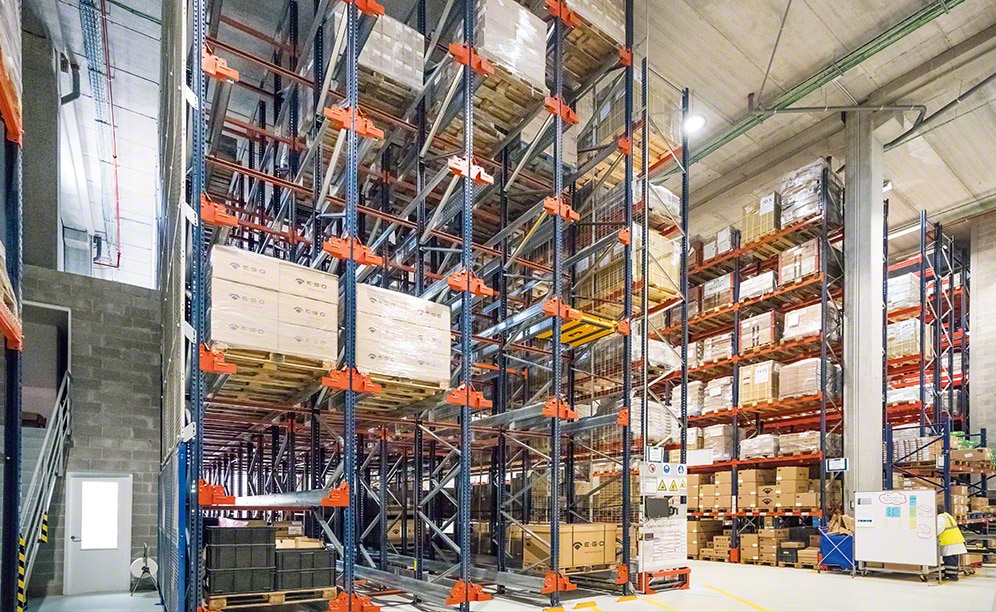
Mecalux equipped the facility with the high-density Pallet Shuttle system, two blocks of Movirack mobile racks and pallet racking
Ask an expert