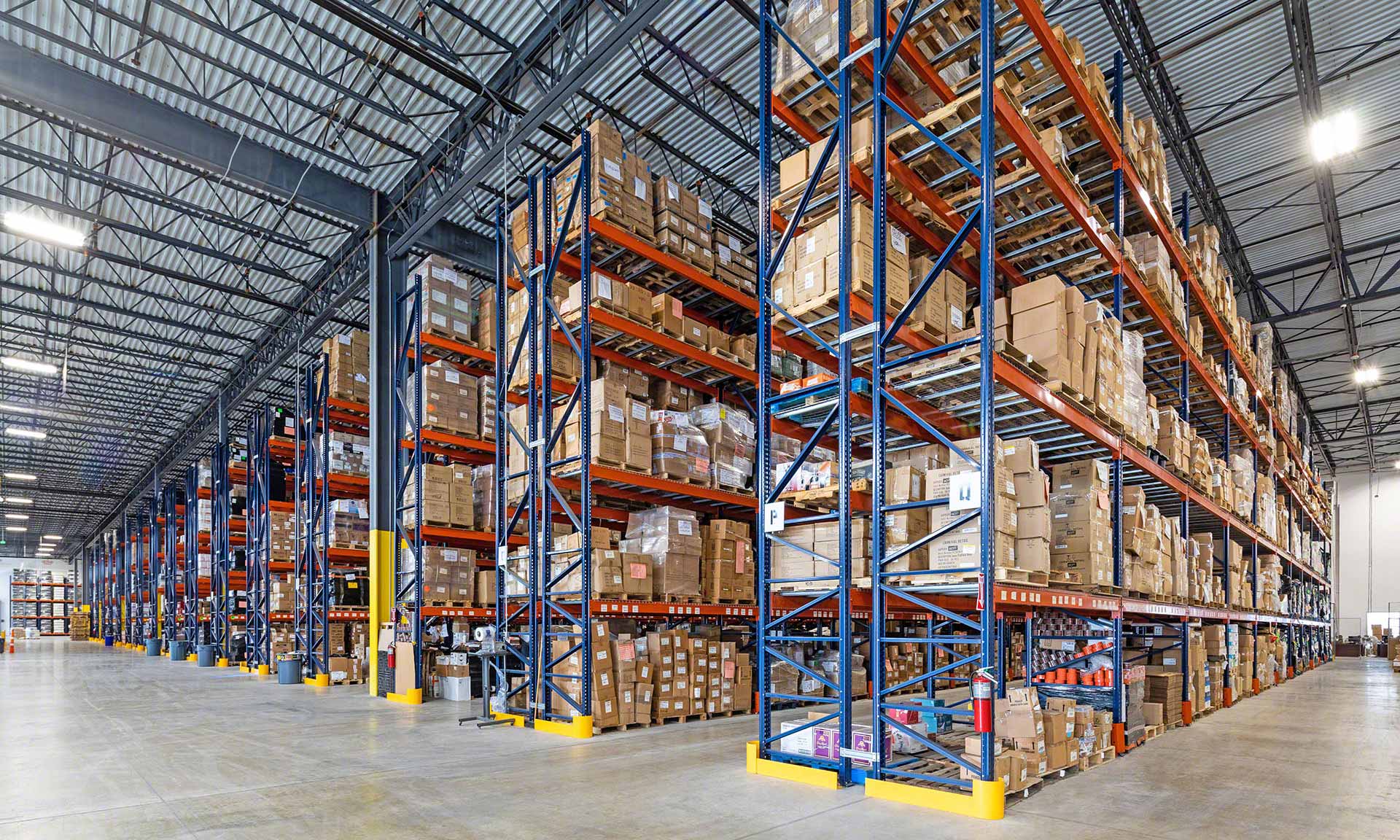
Dufry: direct access and massive storage of 30,000 SKUs
The pallet and push-back racks have been designed to store 30,000 SKUs
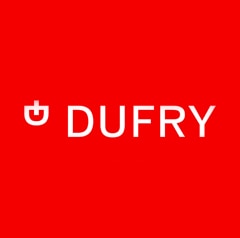
Interlake Mecalux and partner Andersen Material Handling have equipped a 150,000 ft2 warehouse in Miami, Florida for Dufry, a travel retailer. The project includes bolted selective pallet racks and the high-density push-back racking system. Overall, the systems have a 9,200-pallet storage capacity. These two solutions help Dufry manage 30,000 different SKUs and 300 incoming pallets per day.
More than 60 years of travel retail experience
Dufry Ltd is a leading travel retailer that operates 2,400 duty-free and duty-paid shops located at airports, on cruise liners, in seaports, and in other tourist locations.
Founded in 1865, the Swiss-based company employs 31,000 workers and sells more than 50,000 products. The firm also has developed a strong portfolio of long-term concessions with airport authorities and other landlords, managing almost 5 million ft2 of commercial space across the globe.
Selective and compact push-back racks
Dufry needed a well-organized warehouse in order to manage the enormous number of products that it sells to nearly 2.5 billion potential customers. Interlake Mecalux, in partnership with Andersen Material Handling, outfitted a new 150,000 ft² warehouse for Dufry in Miami, Florida with a combination of bolted selective rack and high-density push-back racking.
“The customer brought us in for a fantastic opportunity to help them with their growth,” says Anthony Merkel, Warehouse Products Manager at Andersen. “After a lengthy consultation period, we were finally in a position to provide a proposal for a list of materials. At that point, we brought Interlake Mecalux to the table for their superior pallet racking products. We felt they gave us the best chance for a successful project.”
Interlake Mecalux and Andersen Material Handling worked closely to determine the appropriate solutions for Dufry. “Interlake Mecalux is always heavily involved in proper engineering of a solution,” Merkel continues. “They are meticulous in ensuring that the customer will receive a solution that not just meets immediate needs, but also ensures the durability to last in a rugged environment. Initially we bring them the data, they analyze, and in turn provide the list of componentry to construct a system.”
The racks installed for Dufry are 30’ and 28’ high with four to seven storage levels, and they can hold 9,200 40” x 48” GMA pallets with a capacity of 2,500 lb. There are 31 aisles of racking in the facility and the storage systems hold two to three pallets per level.
Selective pallet racking was the perfect choice for Dufry as it sells such a diverse range of products, such as liquor, chocolate, perfume, textiles, cigars and jewelry. The racking provides direct access to all the products, which was essential for a warehouse with so many SKUs. Direct access speeds up the work of operators when managing the warehouse’s 30,000 SKUs and picking orders. It also ensures accurate stock control because each location stores a single SKU.
The compact push-back racks provide Dufry with excellent selectivity and high-density storage that allow it to house more products. Nesting carriages of this system can deep store up to five pallets at a time. As operators load each pallet, they place it on the free-rolling carriage and push it back into the lane by loading additional pallets. Gravity moves the pallets forward to the aisle on the telescopic carriages during unloading. As such, no reaching or equipment driving into the rack is necessary.
An active warehouse
Both of the storage systems provided by Interlake Mecalux and Andersen help this facility to prepare 40 orders per day with 20 lines per order. Each day the installation receives and delivers 300 pallets, mainly from and to the United States and South America.
Dufry also benefitted from the building’s height, allowing it to store even more products. “What did make this unique is that South Florida has traditionally had lower ceiling elevations,” Merkel said. “This was a spec building with significantly more height than what is traditional in the region. The elevation flexibility allowed us to properly slot and utilize the full extent of their vertical limits.” The advantages provided by this extra height, in addition to their new storage systems, have enabled Dufry to increase its storage capacity by more than 20 percent.
Merkel credited the partnership between Andersen and Interlake Mecalux for devising a solution that satisfied Dufry’s needs. “We are very high on the Interlake Mecalux product and support. We have designed and implemented substantial projects as a partner with Interlake Mecalux, and can speak to the point that they always deliver. Their racking is rugged, their componentry is solid, and their service doesn’t disappoint.”
Interlake Mecalux is always heavily involved in proper engineering of a solution. We have designed and implemented substantial projects as a partner with Interlake Mecalux, and can speak to the point that they always deliver. Their racking is rugged, their componentry is solid, and their service doesn’t disappoint.
Advantages for Dufry
- Direct access to the goods: The bolted selective pallet racking enables operators to have direct access to the 30,000 SKUs stored in Dufry’s facility.
- Increased storage capacity: Dufry’s new storage systems helped to boost the company’s storage capacity by over 20 percent.
- High-density storage: The push-back racking installed in the Dufry warehouse gives the firm the ability to store more products while maintaining excellent selectivity.
Gallery
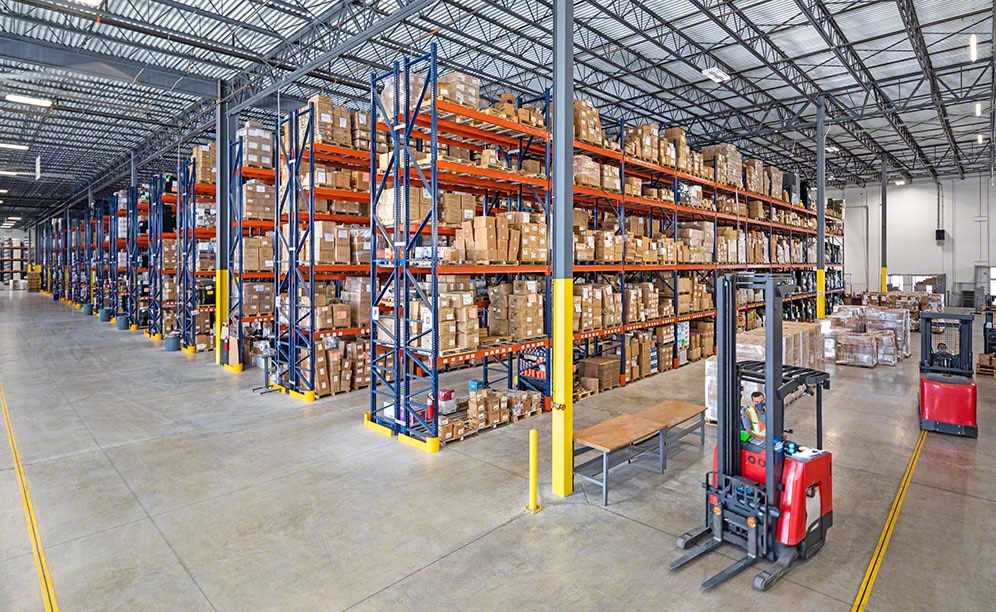
The Dufry facility in Miami with racks from Interlake Mecalux
Ask an expert