Decathlon: omnichannel-ready logistics
The new Decathlon warehouse in Brazil has increased the storage area by 124%
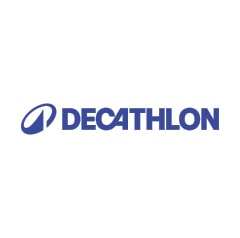
Decathlon opens its new distribution center in Brazil to supply 42 physical stores and online customers throughout the country. Mecalux has installed storage systems that speed up order picking and optimize surface area: pallet racks, picking shelves, and a mezzanine.
Decathlon: warehouse for sporting goods
Decathlon is a renowned company dedicated to the sale of products for sports enthusiasts, both beginners and experts. It arrived in Brazil in 2001, opening its first store in Campinas (São Paulo). In 2013, it began selling its merchandise online. Currently, the business has 42 brick-and-mortar stores in eight Brazilian states.
- Founded in: 1976
- No. of points of sale: 1,600
- Present in: over 60 countries
- No. of exclusive products: 7,000
THE CHALLENGE
|
THE SOLUTIONS
|
THE BENEFITS
|
---|
The commitment to online sales and the resulting modernization of its warehouses is a logistics strategy pursued by Decathlon worldwide. Italy, the UK, France, and Germany are among the countries that have installed Mecalux storage solutions designed for omnichannel retail and to streamline order preparation for this popular sporting goods company.
Decathlon has made a name for itself among the largest sporting goods retailers in Brazil just as it celebrates its 20 year anniversary in the country. And it has done so through unprecedented expansion, accompanied by milestones such as the creation of new brands, the development of strategic alliances, the opening of physical stores, and the consolidation of its e-commerce strategy.
To bolster its logistics division and ensure the sustainable growth of its business activity, the company has just opened its main and largest distribution center (DC) in Brazil, where it stores 21,000 SKUs. “This warehouse supplies our 42 brick-and-mortar stores and our online customers,” says Thiago do Nascimento, Logistics Manager at Decathlon Brazil. Strategically located in Barueri (São Paulo) and connected with the country’s main highways, the center occupies an area of 13.8 acres with the potential to add on 2.47 acres in the future.
“Before opening this new DC, we stored all our goods in two warehouses in Embu das Artes, located about 15 miles from the new center. There, we had a 2.47-acre warehouse for bulky products and full pallets and another 3.7-acre facility for loose units and order picking for online sales,”, says do Nascimento. With the new DC, Decathlon has increased its storage area by 124%.
By starting up this center in Barueri, Decathlon had very specific targets in mind: “We wanted to obtain greater storage capacity, improve operation flows, boost productivity, and reduce delivery times of orders to our online customers and physical stores. Ultimately, the warehouse was designed to support Decathlon’s growth in Brazil,” says do Nascimento.
Decathlon contacted Mecalux because, according to do Nascimento, it considers Mecalux a global partner. “Mecalux has experience implementing other Decathlon projects all over the world, so we know their storage systems and have great confidence in them.”
The company’s omnichannel strategy led Mecalux to install sstorage solutions that speed up order picking and optimize the available surface area: pallet racks, a mezzanine, and picking shelves. Greater capacity means improved operation flows as well as increased productivity when it comes to shortening delivery times, which is essential for satisfying online customers.
“We’re extremely pleased with the storage systems from Mecalux. The warehouse smells like new! We now have more storage space, systems that adapt to the characteristics of our products, and can ensure much greater safety for our employees.”
Ecommerce logistics challenges
Decathlon Brazil’s supply chain stands out for its massive picking operations for orders distributed to the 42 stores in the country and to customers who buy their products through the webpage. To ensure the supply of goods at any time, Decathlon has taken the following objectives into account:
- Choose the most appropriate storage system, i.e., the one that best matches your needs. Direct access to the products facilitates goods handling and order prep. The racks should also be versatile and incorporate accessories for storing SKUs of different sizes.
- Distribute the goods in the warehouse based on their characteristics, size, and demand level to speed up order picking. It is preferable to prioritize the distribution of top-selling products, for example, setting aside a specific area just for these items.
- Use picking assistance devices. RF (radiofrequency) scanners and put-to-light, pick-to-light, voice-picking and vision-picking devices significantly increase productivity levels by making it easier to locate the items.
- Optimize pick paths in the warehouse. Whenever possible, it is recommended that operators prepare more than one order at the same time. These orders should then be checked to ensure that no mistakes have been made.
- Zone the warehouse into different areas. Each section can be made up of a certain number of aisles or can constitute an entire floor of the warehouse. These individual zones can be assigned to a specific number of operators, which can vary according to demand and the number of orders to prepare. This methodology raises picking throughput, provided the sections are connected to each other by means of appropriate handling equipment (such as conveyors).
Mezzanine with picking shelves
The mezzanine is reserved for smaller products (such as clothing and footwear) and was designed to facilitate order picking. “This solution makes much better use of the space, tripling the useful storage area: the mezzanine houses about 85% of our SKUs,” says do Nascimento. Standing 33.5’ tall and divided into three floors, the mezzanine stores 175,620 boxes measuring 16” x 24” and with a maximum unit weight of 55 lb.
Each of the three levels is allocated to a specific product type and has a specific number of operators to carry out picking. These workers walk up and down the aisles, picking the products that make up each order directly from the shelves. The design of the shelves, which features direct access to the goods, makes operators more productive.
The different mezzanine floors are connected by means of a multi-level conveyor circuit, which brings finished orders to the consolidation area. Thus, instead of having to travel around the warehouse to prepare orders, operators can work exclusively in the area assigned to them.
“One of the advantages of this mezzanine is that all the picking areas in the warehouse are very close together, so replenishment and inventory control are performed more quickly. Even though it’s only a mezzanine, we’re thrilled with it because it gives our employees a pleasant place to work,” says do Nascimento.
Pallet racks
“The thing we like most about the pallet racks is their versatility and robustness for storing the bulkier products,” says do Nascimento. These racks house items such as bicycles, punching bags, and tents, in addition to the reserve stock used for the picking shelves.
In total, this area stores 13,809 pallets containing goods of three different heights: 8’, 6.2’, and 3’. Therefore, pallet racks were the most suitable choice for storing pallets with many SKUs of varying weights, sizes, and dimensions. Operators work mainly with reach trucks to insert and remove pallets from their locations and with low-level order pickers to prepare orders.
Modern logistics
Logistics operations at Decathlon are complex: items can be purchased in any of its physical stores throughout Brazil and are also at everyone’s fingertips via its webpage.
With the opening of the DC in Barueri, Decathlon can ensure deliveries in the shortest time possible and cope with the high demand. Do Nascimento says, “We set out to improve processes and increase efficiency. The DC will help us to continue growing in Brazil. And we’re definitely going to keep investing in technology to cut order delivery times and enhance the quality of our operations.”
The new DC in Barueri has consolidated Decathlon’s expansion in Brazil: we’ve opened more points of sale all around the country, and our online orders have increased. With the storage solutions from Mecalux, we’ve raised productivity by reducing the number of movements operators make in the warehouse.
Pallet racks | |
---|---|
Storage capacity: | 13,809 pallets |
Pallet size: | 40” x 48” |
Max. pallet weight: | 1,543 lb |
Max. rack height: | 34.5’ |
Max. rack length: | 180’ |
Gallery
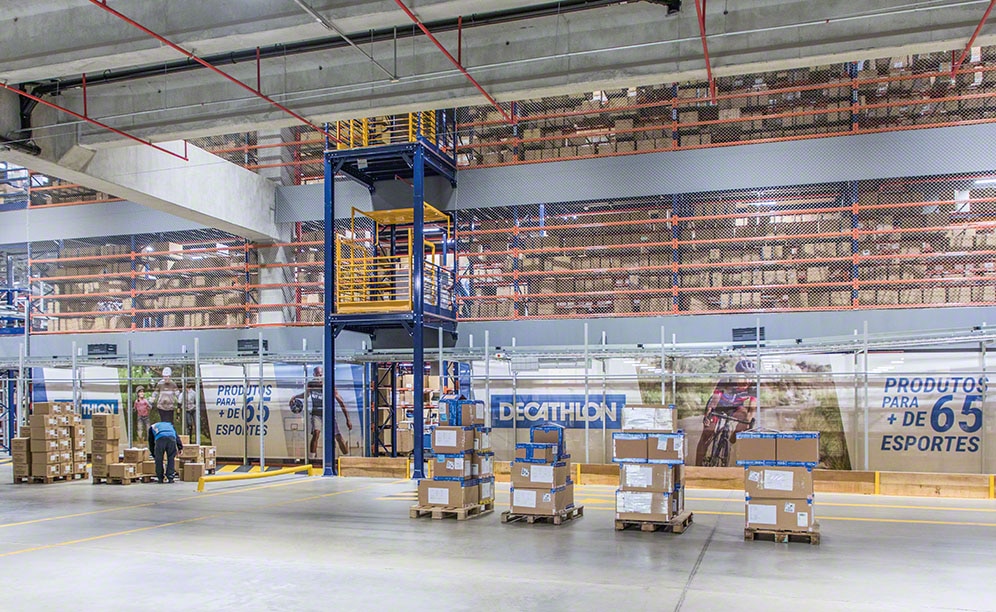
Decathlon's new omnichannel warehouse in Brazil
Ask an expert