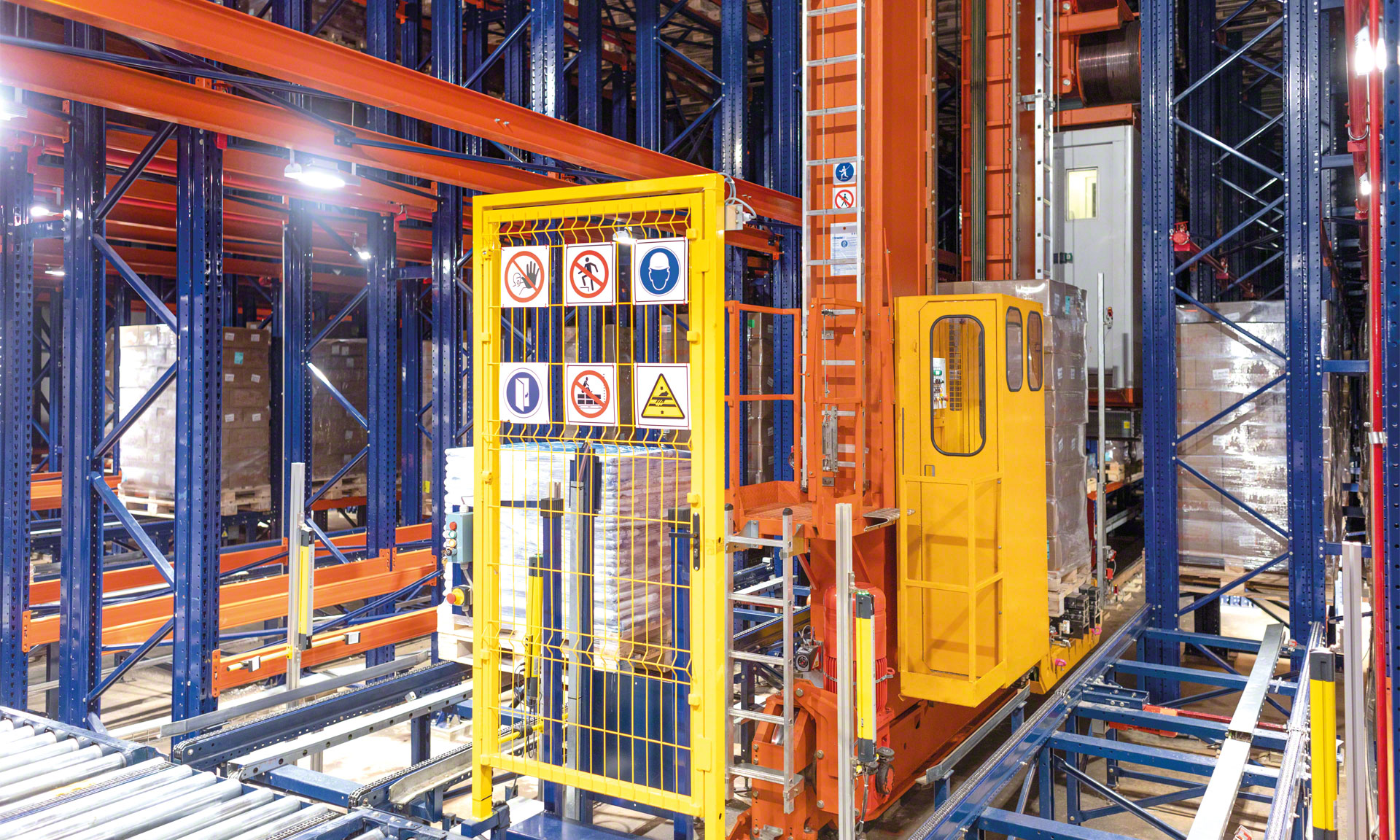
Copacol: automation and digitization, key to food safety
Copacol has increased productivity by 20%, dispatching 1,020 tons of meat every day
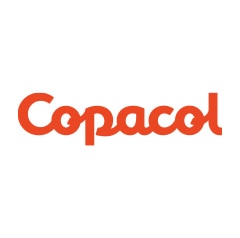
Copacol (Cooperativa Agroindustrial Consolata) centralizes its logistics operations in a modern, fully automated distribution center in Corbélia, Brazil. The company has also implemented Easy WMS management software from Mecalux to ensure product traceability in real time.
Copacol: flavor and quality
Copacol is an agribusiness cooperative founded in 1963 in Cafelândia, Brazil, with the aim of providing electricity to the farmers in the region that were members of the cooperative. Over the years, it has specialized in food production and marketing.
- Founded in 1963
- Acres of farmland: 250,000
- No. of cooperative members: 6,900
- International presence: over 70 countries
CHALLENGES
|
SOLUTIONS
|
BENEFITS
|
---|
Guaranteeing safety is a priority for any business working with food products. In this sector, storing goods in a suitable environment is essential for preserving the proper condition of the food and ensuring the health of consumers.
Copacol (Cooperativa Agroindustrial Consolata) is firmly committed to food quality and safety and, at the same time, to the continuous supply of products to its customers. It does this by investing in the automation and digitization of its supply and distribution chains. For Copacol, it is vital to have flexible logistics operations that enable it to maximize stock capacity, streamline processes, and strictly control the condition of its goods.
In its modern distribution center (DC), the automatic handling equipment safeguards the food, ensuring optimal hygiene in all processes. The company has also implemented the Easy WMS warehouse management system to ensure traceability of the products in real time.
Centralized logistics
“Before bringing all our logistics operations together under one roof, our goods were stored in our different centers around Brazil. And this made order preparation and dispatch very difficult. We had to contract the services of logistics providers to distribute the goods, with the high cost that this entailed for our business,” says Logistics Manager Itamar Ferrari.
The need to centralize logistics activities grew along with the production volume. In 2020, Brazilian tilapia production grew by 12.5% compared to the previous year, exceeding 590,722 tons of fish. Of this figure, Copacol was responsible for producing 44,974 tons. In addition to fish, the company markets poultry meat: poultry production accounts for 60.29% of the cooperative's gross earnings (578,383 tons of meat were processed last year). The company's revenue rose by 27.24% between 2019 and 2020.
Copacol decided to centralize its logistics operations in a 3.9-acre distribution center in Corbélia, Brazil. “The DC serves as a logistics hub: there, we classify and dispatch goods for the national and international markets, in line with our sales strategy,” says Ferrari.
The company wanted to start up a warehouse with the maximum possible storage capacity in order to accommodate all the products.
The new center has space for storing a large number of goods, specifically, 17,086 tons of products for 15 days before they are distributed to customers. “When starting up this DC, our priority was to facilitate management and handling of the food at a controlled temperature. And we knew we definitely wanted its operations to be automated. Automation would allow us to boost productivity, reduce the presence of staff in low-temperature environments, and improve our customer service.”
For this ambitious project, the company contacted Mecalux “because of its experience in setting up automated warehouses,” says Ferrari. “We liked the fact that Mecalux would use simulation to design the best solution for us and that its technical team was so strict about compliance with regulations. The sales team showed us projects of other companies with needs similar to ours to guide us in making the right decision.”
With this new facility, Copacol no longer relies on external logistics providers to help it manage its operations, which has cut costs. Moreover, the new center has provided Copacol with another considerable advantage: the company has freed up storage space in its production plants. Thus, it has expanded its facilities and can now store products destined for export. The aim of all this is to continue growing and broadening its market in the future.
Automated logistics operations in freezer rooms
Copacol’s distribution center comprises two automated warehouses that operate at different temperatures. One of them is a rack-supported facility allocated to frozen products (mostly made from chicken and fish). The warehouse is made up of four aisles that work at a temperature of -13 °F and store 13,780 tons of chicken and about 1,875 tons of fish. The other automated facility, which has a single aisle operating at 39.2 °F and capacity for 1,430 tons of chicken, houses refrigerated products.
Every day, the DC receives 1,230 pallets from Copacol’s different production plants in Brazil, in addition to items sent by suppliers. All these goods are deposited in the corresponding warehouse prior to their distribution to customers. The DC dispatches 400 orders a day, the equivalent of 1,020 tons of meat delivered in 70 trucks.
This high number of movements is only possible with automated storage systems. “We have a very modern DC. It’s equipped with stacker cranes that perform the storage tasks with full autonomy. The speed of product inflows and outflows is much faster than it would be with forklifts. Plus, as the stacker cranes do all the work, we’ve gained in accuracy and eliminated errors,” says Ferrari.
Process digitization in the warehouse
With such a demanding supply chain, another challenge the company faced was goods control. In order not to lose track of any of its products, Copacol has implemented the Easy WMS warehouse management system from Mecalux. This software supervises and optimizes everything that happens in the DC, from the moment the goods are received until the orders are dispatched. Copacol ensures full product traceability in its center.
When the pallets arrive, Easy WMS organizes them according to good type, SKU, product characteristics, and available locations in the DC’s two facilities. “The warehouse management software has modernized our logistics operations by providing us with total traceability of the goods,” says Ferrari.
Preparation of 400 orders a day
Order picking is one of the main operations in this DC. Given the large quantity of orders placed by customers and the tight time frame for delivering them, Copacol has set up a large area for carrying out picking between the two automated warehouses.
The space is divided into two aisles, one at a frozen temperature and the other, refrigerated. A transfer car is tasked with depositing the pallets in the channels used for picking. The operators walk up and down the aisle assigned to them, picking the items designated by Easy WMS directly from the pallets.
In total, the picking area contains 306 channels formed by flow roller conveyors, each with capacity for two pallets. The advantage of this system is that operators can prepare orders uninterruptedly, as they always have reserve stock. “The transfer cars supply the flow channels for picking with goods continuously to avoid interruptions in order prep,” says Ferrari.
For order picking to be effective, the operators need the help of the WMS. This is because they walk about the picking area with an RF scanner, which they use to consult the items they need and their location. “When preparing orders, Easy WMS is governed by our customers’ requirements. Its priority is to satisfy their expectations and needs,” says Ferrari.
Essential logistics for high output
Copacol places great importance on supply chain efficiency, as its objective is to effectively supply its customers in Brazil and internationally. The new distribution center opened by the cooperative in Corbélia has been built with the aim of improving storage flows and streamlining the distribution of goods.
With the implementation of automation and the Easy WMS warehouse management system, Copacol is prepared to face any challenge, such as the coronavirus pandemic. “Logistics has played a key role in the pandemic because we had to make sure customers would always find the products they needed. Thanks to automation, we were able to adjust to market changes and safety protocols to protect our employees, partners, and consumers,” says Ferrari. And what does the future hold for this company? Copacol has no doubts about that: “We’re going to keep producing healthy, tasty food. Our mission is to ensure the health of our customers, and to that end, we’re extremely demanding when it comes to food safety,” says Ferrari.
The new DC has enabled us to improve our logistics operations, handle the rise in production, and offer our customers better service. Automation has increased speed and efficiency in the movement of goods. And the management software has given us total traceability of our products, which is a priority target in the food sector.
Warehouse 1 | |
---|---|
Temperature: | -13 °F |
Construction: | Rack-supported |
Storage capacity: | 15,672 pallets |
Warehouse height: | 118' |
Warehouse length: | 440' |
Gallery
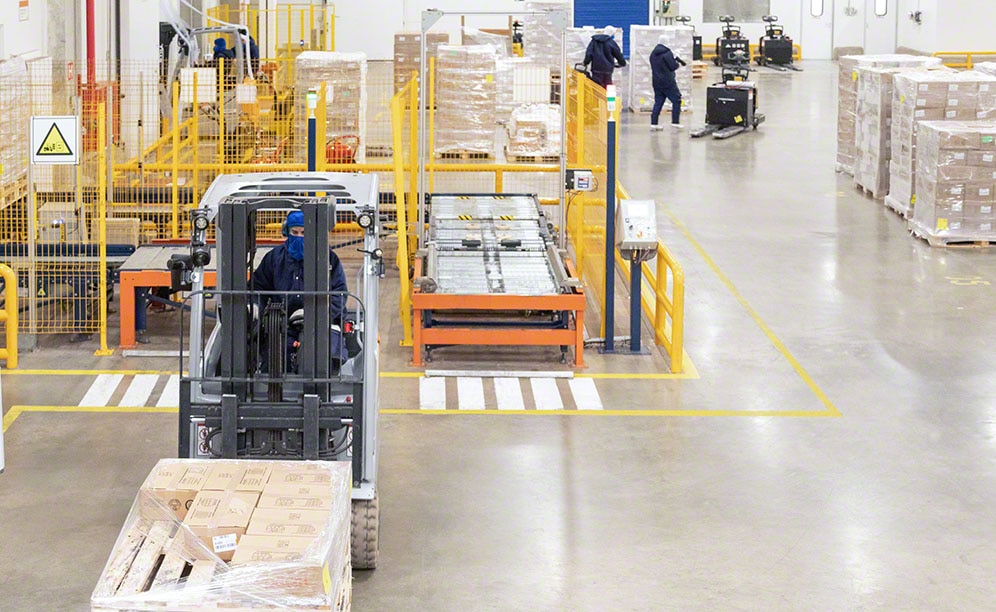
Copacol's picking area at frozen and refrigerated temperatures
Ask an expert