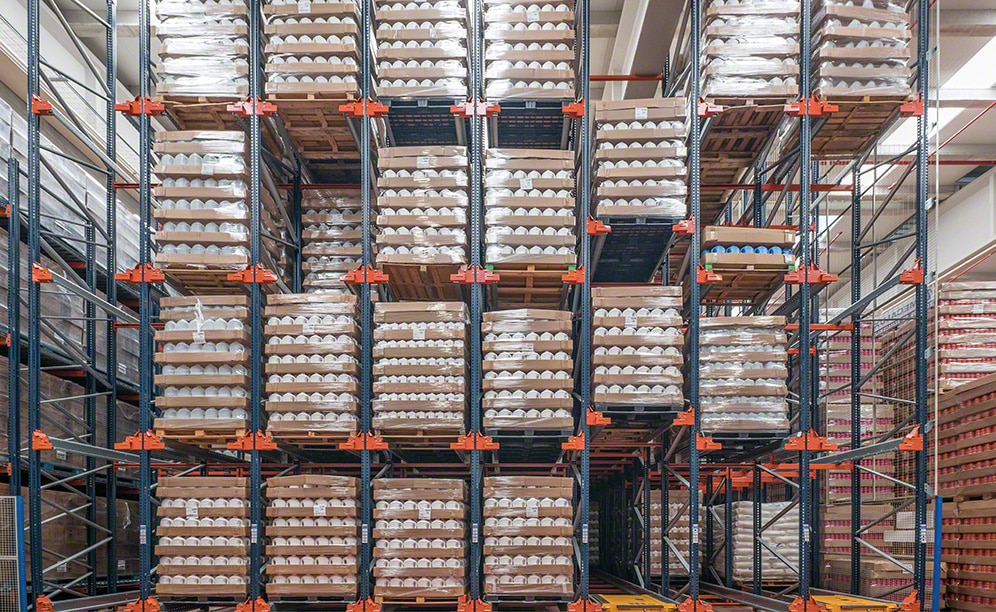
Two storage systems for chemical cleaning products
Pallet flow racks with stacker cranes and the semi-automatic Pallet Shuttle system in the Pons Químicas warehouse
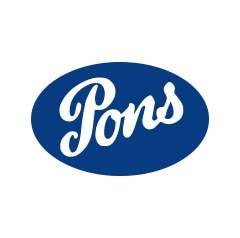
Pons Químicas, the cleaning supplies maker, has reorganized the operations of its warehouse in Jávea (Alicante) under the guidance of Mecalux. On one side, it has installed a block of pallet flow racks operated by a stacker crane where it stores finished products. On the other is the semi-automatic Pallet Shuttle, which supplies the production center with needed packaging. Additionally, Mecalux has enabled conveyors that join the production exit to the warehouse and deployed the Easy WMS warehouse management system.
Needs of Pons Químicas
Pons Químicas is a Spanish company founded in 1960 that specializes in household and professional-grade cleaning products. Spain is the site of one production plant, while another is set up in Romania. Over the last few years, it has pushed its market boundaries throughout Europe and Africa. To do so, it required higher storage capacity, while also increasing the productivity of its warehouse located next to its manufacturing center in the town of Jávea (Alicante).
Pons Químicas has always relied on the collaboration and expertise of Interlake Mecalux to work out solutions that are a perfect fit for their demands.
Production warehouse
Bearing in mind the needs of Pons Químicas, Interlake Mecalux has set up:
- Pallet flow racks run by a stacker crane.
- Semi-automatic Pallet Shuttle system.
- Roller conveyors.
The installation of these systems was executed in several phases, taking into account the company’s needs and the increase in production achieved in recent years.
Pallet flow racks run by the stacker crane are allocated to finished products. This automated warehouse can operate 24 hours a day, uninterrupted and with minimal personnel. Moreover, it ensures permanent workflows. Meanwhile, the semi-automatic Pallet Shuttle system acts as a buffer, i.e., as a temporary warehouse where bottles used for everyday production processes are housed.
Both storage systems are high-density systems and make full use of the available surface to obtain optimal capacity.
Pallet Shuttle system
The block of racks is 37' high and comprises 31 channels that provide a 600-pallet storage capacity. The merchandise flowing from the production center is slotted through the loading aisle (next to the docks). These products are later removed from the opposite side, which is used for unloading and coincides with production.
It is a highly systematic way to supply the production center with the required packaging, since the whole process is quick and straightforward. Operators do not drive the forklifts into the lanes to handle the goods. Instead, the shuttle carries out all movements automatically.
Operators, riding reach trucks, place the Pallet Shuttles in a specified channel. Next, they transfer the pallets to the first position in the racks, and the motorized shuttle shoots them straight up to the first free location. The same operation is done but in reverse order to extract the goods through the unloading aisle.
Automated warehouse
A roller conveyor circuit shifts the goods from the production center up to the warehouse automatically. This system requires minimal involvement on the part of workers, thus, eliminating errors that result from manual handling.
Afterward, the stacker crane picks the pallets off the incoming conveyor and deposits them in the allocated channel. This machine operates at speeds of 525'/min and 125'/min when raised, being able to absorb a huge number of deliveries flowing from production and to insert them into the flow racks.
The block of racks stands 33.5' high and 148' long. Comprised of 160 channels, each 74-inch-deep channel can house up to 18 pallets. Overall, the automated warehouse offers a 2,880-pallet storage capacity for 32" x 47" bases.
Racks comprise slightly inclined roller channels so that the merchandise flows via gravity. The stacker crane puts the pallets into the highest part of the roller frames. Gravity does the rest, and at a controlled speed, moving them towards the other end so they are ready to be removed.
This solution speeds up the loading and unloading of pallets, since handling by personnel is minimal (workers only pick pallets from their specific locations). Plus, the distances being covered are nominal, since all SKUs are in the same aisle.
The goods are managed according to the FIFO (first in, first out) storage method. In other words, the first pallet in is the first to leave, making precise product rotation possible.
Easy WMS by Interlake Mecalux
The warehouse management software developed by Interlake Mecalux controls the flows of the automated warehouse. It steps in during different operations and processes, including the entry of pallets on the conveyors, the assignment of specific locations, and the subsequent extraction of the pallets to be sent to dispatch. Likewise, it controls the stock and always knows the exact location and status of the merchandise.
The Easy WMS by Interlake Mecalux is in continuous, bi-directional communication with Pons Químicas’ ERP. Furthermore, it has rolled out the Galileo control module that directs the movements of the electromechanical equipment, such as the conveyors and stacker cranes.
Advantages for Pons Químicas
- Boosted storage capacity: a total of 3,480 pallets can be housed in the Pons Químicas warehouse.
- Agility and density: the two storage systems facilitate the loading and unloading of the products in short order.
- Efficient management: warehouse operations are directed and organized using Easy WMS by Interlake Mecalux.
Flow racks | |
---|---|
Storage capacity: | 2,880 pallets |
Pallet sizes: | 32" x 47" x 59" / 71 |
Max. pallet weight: | 1,653 lb |
Levels high: | 4 |
No. of channels: | 160 |
Racking height: | 33.5' |
Gallery
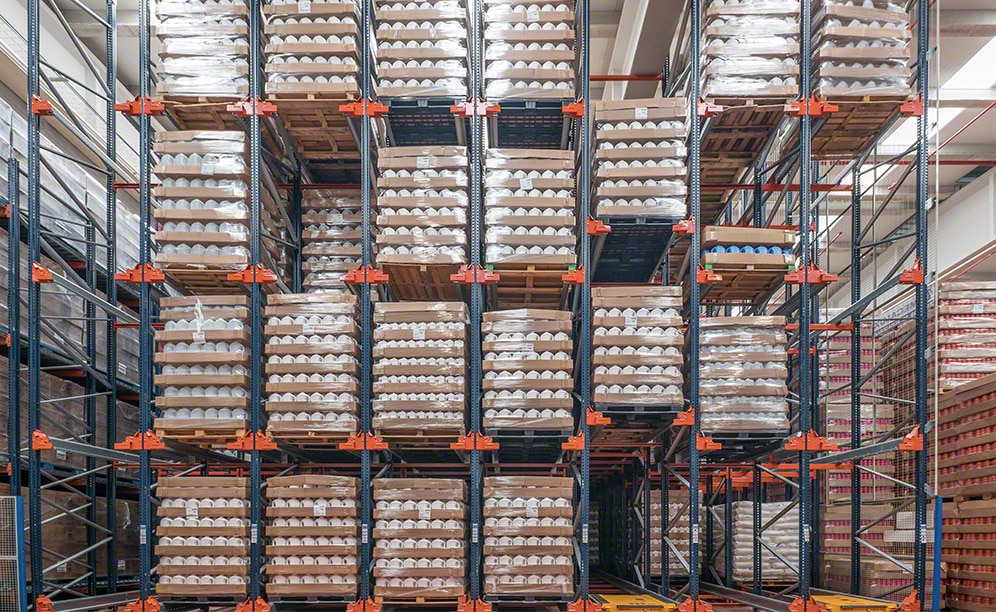
Installation focuses on the storage of Pons Químicas warehouse
Ask an expert