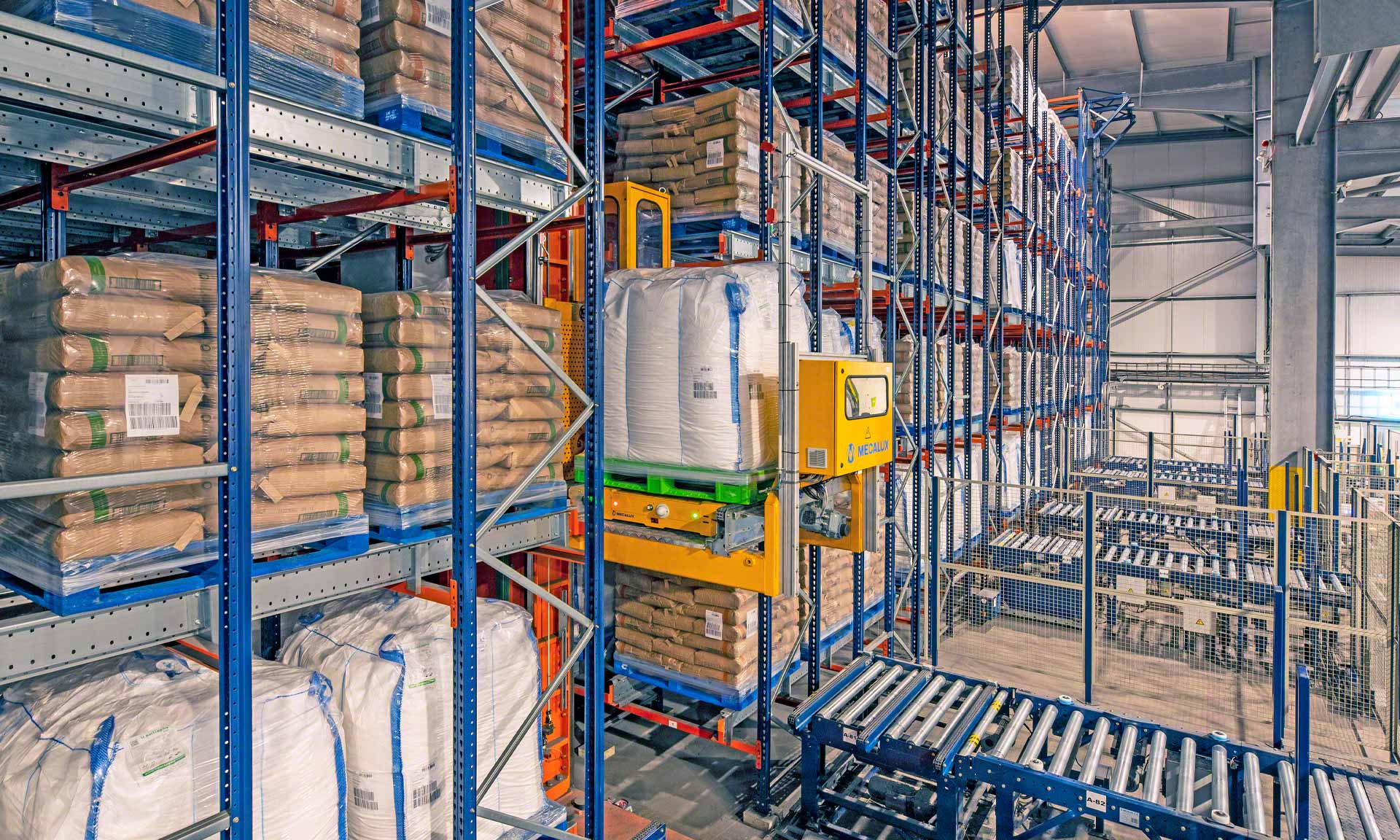
British Sugar reaffirms its commitment to innovation with an AS/RS in Wissington
British Sugar has installed an AS/RS from Mecalux in Europe’s largest sugar processing plant.
British Sugar, the UK’s main sugar producer, has installed an AS/RS (automated storage and retrieval system) from Mecalux in Europe’s largest sugar processing plant, producing over 440,000 tons of sugar and 70,500 tons of ethanol a year.
British Sugar: leader in sugar production
British Sugar is the leading sugar manufacturer in Great Britain and Ireland. The company is continuously growing: in recent years, it has invested over $280 million to double its production capacity. British Sugar is part of AB Sugar, a wholly owned subsidiary of international food, ingredients, and retail group Associated British Foods (ABF).
- Founded in: 1912
- Production centers: 4
- Production capacity: 1.3 million tonnes of sugar
- No. employees: 1,400
CHALLENGES
|
SOLUTIONS
|
BENEFITS
|
---|
How can British Sugar supply around half of the UK's sugar demand? To do this efficiently and manage changes in the market, the company turns to innovation and technology.
In recent years, the business has implemented a modernization plan for four production centers to become more competitive and provide its customers with outstanding service. British Sugar has reached an agreement with broadband service provider Virgin Media O2 to connect four of its factories to 4G. Its aim is to leverage automation and the Internet of Things (IoT) to work in a much more secure digital environment.
British Sugar’s processing plant in Wissington (UK) is the largest of its kind in the country as well as in Europe. Since it opened its doors in 1925, the facility has been transformed year after year to become the first bioethanol production plant in the country. “Today, the plant converts over 3.3 million tons of sugar beet per year into over 440,000 tons of quality sugar and 70,500 tons of ethanol (used for motive or electric power),” says Samuel Chapman, Purchasing Manager at British Sugar.
With this production rate and very promising future growth prospects, the company was looking for a storage system to accommodate the 1,500 pallets of finished goods that leave production every day. Previously, British Sugar deposited all its products on pallet racks, which came up short in terms of the necessary storage capacity. “Plus, all operations were manual, so operators spent a lot of time loading and unloading pallets from the racks,” says Chapman.
After weighing several options, British Sugar decided on automation. The company chose to install the Pallet Shuttle with stacker cranes from Mecalux, a storage system that makes the most of all the available surface area to house as many products as possible. “All movements of goods are automated, which really speeds up product inflows and outflows. Thanks to the automated movement of the stacker cranes, conveyors, and motorized shuttles, we’re able to complete the cycles required to serve our customers,” says Chapman.
Michael Burton, Customer Supply Lead at the Wissington Factory, explains why British Sugar decided to invest in new technologies: “Innovation is at the heart of everything we do and is crucial to our factories of the future. And so we're continuously looking to improve our operations. Part of this is optimizing our warehouse, which, in turn, is vital for meeting the needs of our customers and becoming their supplier of choice.”
Moreover, Burton says: “I think a single provider such as Mecalux — who were able to supply both automation and software solutions — not only provided benefits during the design and commissioning phase, but also proved invaluable now that the system is operational.”
Characteristics of the AS/RS for boxes
“Logistics operations are key to British Sugar's business strategy. We're committed to being supplier of choice for our customers, and this involves optimizing our supply chain, in which logistics are a critical part,” says Burton.
The new storage system is automatically connected to production via a pallet conveyor. It receives 1,500 pallets a day containing finished product. All pallets must go through a checkpoint where the dimensions and weight of the goods are verified.
The conveyor circuit, which connects the output of the production lines with the storage area, runs along the side of the racking until it reaches the front of the AS/RS. “The automatic connection between the two facilities is essential when it comes to streamlining the flow of goods,” says Burton.
The Pallet Shuttle is a fully automated compact storage system. It comprises a motorized shuttle that moves pallets inside the storage channels with total autonomy. In each of the six aisles, stacker cranes for pallets transport the goods from the AS/RS entry point to any storage channel. This is done in line with instructions from Mecalux’s Easy WMS warehouse management software.
“Automation's provided a number of benefits, most notably the improvements in safety and health as a result of the reduction of forklift movements within the warehouse,” says Burton.
The racks make the best use of the storage system’s surface area to provide the greatest possible storage capacity. In the case of British Sugar, the AS/RS accommodates 4,500 pallets in just over one acre.
Automation ensures that the pace of work at British Sugar is where it needs to be. To enable the company to ship 1,500 pallets a day of finished product to customers in the UK and Europe, Mecalux has installed four outbound goods stations. These consist of automatic conveyors that join the AS/RS with the docking area, located just in front of the racks to expedite the distribution of goods.
The automated handling equipment in British Sugar’s warehouse — conveyors, stacker cranes, and shuttles — ensures the efficient, error-free putaway and dispatch of 3,000 pallets a day (1,500 inbound and 1,500 outbound).
Warehouse under digital control
Considering the wide variety of SKUs and number of goods movements made on a daily basis, the company also chose to implement the Easy WMS warehouse management system from Mecalux. “Being a supplier of choice, it is extremely important that we have full traceability of our product. Easy WMS allows in-depth analysis, if needed, to understand the full history and origin of any pallet within the warehouse,” says Burton.
The software incorporates rules and algorithms to organize the products based on their particular characteristics and demand level. Each aisle is divided into three sections according to product turnover: type A, B, or C. Thus, for example, type A items (higher demand level) are placed at the front of the racks to streamline entries and exits, while B and C items are slotted towards the back.
To improve goods control, the warehouse management software communicates with British Sugar’s ERP system. The ERP system notifies Easy WMS in advance of the items that will arrive at the AS/RS from production so that the WMS can assign them locations more quickly.
Logistics 4.0
“British Sugar is an agile business, and it's crucial that we've got the flexibility between our systems and plant to manage fluctuations within our production demand effortlessly and seamlessly,” says Burton.
British Sugar is an innovative company that, from the outset, has been committed to technology with the aim of fostering change and the constant improvement of its processes. The opening of this new AS/RS in its plant in Wissington is a testament to the promising future that lies ahead for this business.
Automation and digitization guide British Sugar in achieving all the goals it sets for itself. With technology, it can closely track its products and optimize all its operations. British Sugar does all of this with one clear objective in mind: to offer a quality product.
The implementation of a new AS/RS forms part of our supply chain optimization strategy. Through technology and automation, we want to more accurately monitor our products and speed up storage and order dispatch tasks.
The automated storage systems from Mecalux have provided us with a number of logistics benefits, especially when it comes to operators’ health and safety. Digitization with Easy WMS has given us complete traceability of our stock, which is vital in our business
Gallery

The stacker crane moves the pallets in the storage aisles
Ask an expert