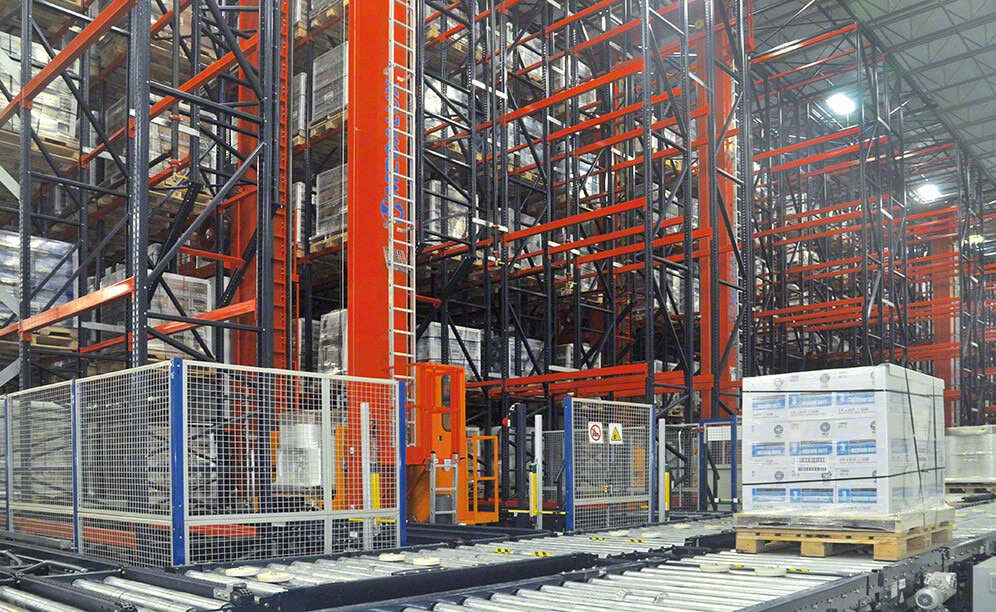
Interlake Mecalux AS/RS helps Charter Next Generation store products of all shapes and sizes
Top capacity at Charter Next Generation with pallet conveyors and 459' long aisles
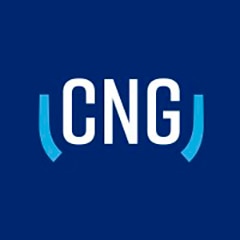
Interlake Mecalux has built a new automated warehouse for Charter Next Generation with a storage capacity for more than 15,400 pallets of different sizes and turnovers. The installation is managed by the efficient Easy WMS warehouse management system by Mecalux, capable of maximizing the productivity of all operations being performed.
About Charter Next Generation
Founded in 1994 by CEO David Frecka, Charter Next Generation is a successful manufacturer of highly engineered food-grade blown films. The company focuses on technology and using the best equipment to make premium products for its customers. It is at the forefront of innovation and technology, making films for packaging applications across many industries, but with a specialization in food-grade film.
Charter Next Generation has experienced exponential growth quite recently, rapidly expanding organically by adding new lines each year to keep that pace moving forward. The company grows by building its own production capacity using proprietary technology and formulas to win new customers and to continue meeting its current customers’ needs.
Needs and the solution presented by Interlake Mecalux
Along with its year-after-year double-digit growth came the need for Charter Next Generation to increase its distribution capacity. “Dave Frecka, our CEO and founder, who is kind of a visionary, really looked at what our situation was for distribution and found that to be a real opportunity for improvement for the company,” said Jason Hildenbrand, director of logistics for Charter Next Generation. The company needed a scalable solution that would allow it to warehouse food-grade products in a very clean and structured environment and to deliver those products to its customers from a single, well-controlled master distribution facility. Charter Next Generation began looking for partners who could make such a distribution center a reality and ultimately decided to bring in Interlake Mecalux to help.
“Charter Next Generation has a number of challenges because we are in so many different industries and really keyed into exactly what our customers in those industries need,” Hildenbrand said. “We have several different packaging configurations and skid sizes that made automation a challenge for some folks. I think that is one place where Interlake Mecalux stepped in and really differentiated themselves from others and that is why they won the opportunity to help us with this project.”
Before embarking on this project, Charter Next Generation had a warehouse with a 3,000 pallet capacity with the rest of the pallets distributed in leased warehouses off-site. Interlake Mecalux proposed constructing an automated storage and retrieval system (AS/RS) with a capacity for 15,400 pallets.
“Interlake Mecalux did an analysis to help guide us through the process using their experience extensively in Europe with similar situations and customers that had some similar challenges,” Hildenbrand said. “They were able to adapt a solution that really had been tried and true to the specific needs of Next. I think it was really just kind of downloading that understanding of what we needed here by doing the math, crunching the numbers, and applying their experience to come up with a custom solution that was still off the shelf enough that everyone had confidence that it could be done effectively.”
The warehouse
The AS/RS that Interlake Mecalux designed has six working aisles where an equal number of stacker cranes circulate. The aisles feature double-deep racking on both sides that is 39' high and 459' long to achieve maximum capacity without needing to be very tall. In fact, the automated warehouse has the longest aisles the Mecalux Group has ever set up anywhere in the world. The height of the racking levels also offers greater flexibility to locate unit loads of three different heights. Two of the AS/RS’s rows have six levels – two levels for small pallets, two for medium ones, and another two for large pallets. Two additional rows have seven levels, with six of them being for small pallets and one level for medium-sized ones. The next two rows have five beam levels to accommodate taller pallets.
The racking contains 56 bays that can accommodate two pallets per beam level. The lower-rotation, type C products are toward the back of the warehouse, medium-rotation, type B products are in the middle, and higher-rotation type A products are closer to the front. This improves the cycles of the stacker cranes. Interlake Mecalux also had to adapt the width of the aisles and the dimensions of the stacker cranes’ telescopic forks to handle the larger pallets safely. Moreover, the AS/RS features safety access doors that cut the power to the stacker crane when an operator opens them, thereby ensuring the well-being of the workers.
The combined operation of the six stacker cranes can do 108 combined cycles, superior to the 80 combined cycles required by Charter Next Generation. Initially, the design of the automated warehouse called for five stacker cranes, but once the Interlake Mecalux team started looking at the size of the AS/RS, they noticed there was still room for an additional crane. “Charter Next Generation knew that they were going to be growing at a pretty rapid pace and were going to need the additional storage,” said Bob Novak, national accounts manager at Interlake Mecalux. “I suggested that we leave space for a sixth crane. If we had to expand the building that was the time to do it, but we were able to do it within the same footprint. Well, before we even delivered the first crane, we got the order for the sixth crane.”
While the automated system itself is complex, the process for incoming and outgoing pallets is rather simple.
Inputs
The AS/RS has two entry points equipped with pallet dispensers that supply 40" wide by 48" deep slave pallets. These slave pallets allow the warehouse to store various-sized pallets up to 42" wide and up to 60" deep. When entering a load pallet into the system, a forklift driver will place the load pallet on top of the slave pallet where it will then proceed to a pallet checkpoint. The checkpoint inspects the dimensions, weight, and quality of the pallet. The pallets that do not pass inspection go to a rejects conveyor for reconditioning.
If the pallet is in good condition, the checkpoint will read a label, and the Interlake Mecalux Easy WMS warehouse management software will search for the optimum location for the pallet in any of the six aisles, depending on the height of the pallet and the product’s rotation. After passing through the checkpoint, the pallet makes its way along the automatic conveyor circuit toward the stacker cranes. Once in the entry position, a stacker crane will load the pallet and take it to its position in the rack.
Outputs
As for the shipment process, when a customer places an order, Easy WMS will verify the locations in the racking from which the stacker cranes will retrieve the products. These stacker cranes then take the pallets to the conveyor circuit where they travel along a loop toward a transfer shuttle. The warehouse has 10 conveyor lines connected by the pallet transfer shuttle.
Eight outbound conveyor lines are available for preparing shipments. These lines can hold seven pallets each. The other two lines are for returning slave pallet stacks. Forklift drivers then remove the load pallets from their slave pallets and begin loading the trucks waiting at the docks. Once the forklift driver has taken the load pallet to the truck, the slave pallet returns automatically to a slave pallet stacker. When the slave pallet stacker has a stack of seven pallets, the stack will move toward the pallet dispensers near the inbound conveyors. However, if the buffer for the pallet dispensers is full, then the stack of slave pallets will travel along the conveyor circuit toward the racking where the stacker cranes will store them.
Interlake Mecalux Easy WMS and Galileo
Charter Next Generation is able to achieve full warehouse management by using the Interlake Mecalux Easy WMS warehouse management software. This software enables Charter Next Generation to optimize the physical management and tracking of the flow of goods, from entry into the warehouse to shipping, guaranteeing traceability. It is in constant communication with the ERP of Charter Next Generation, to control, coordinate, and report on all logistics processes and operations that are taking place in the warehouse.
The Easy WMS warehouse management system improves the management of fundamental operations in all areas of the Charter Next Generation automated warehouse: receipt of goods, storage and inventory, order preparation, and shipping. The automated warehouse also features the Galileo control software, tasked with controlling and monitoring all actions performed by various mechanical components. Interlake Mecalux also provided Charter Next Generation with a multi-view visualization system that allows warehouse operators to see what is taking place within the automated warehouse at any given time, all on one 40" monitor.
Advantages for Charter Next Generation
Choosing to automate its main distribution facility has allowed Charter Next Generation to scale its operation without needing to constantly add new team members so that the company can ensure that its workers have the training and experience to really get to know its customers. The company also will achieve freight savings by being able to get full trucks of product to its customers when they need it. “We should experience savings based on really being able to deliver a kind of service that we need so there are fewer multiple shipments and fewer disruptions in the supply chain for our customers,” Hildenbrand said.
- A significant capacity increase: the AS/RS can store 15,400 pallets.
- Boosted productivity: the six stacker cranes can handle a total of 108 combined cycles per hour, guaranteeing fast and error-free shipments.
- High flexibility: any pallet can go to any location within the AS/RS.
- Increased safety: this investment allows Charter Next Generation to fulfill its customers’ orders with the highest product safety levels and the best service currently available in the sector.
Charter Next Generation automated warehouse | |
---|---|
Rack Length: | 459’ |
Rack Height: | 39’ |
Number of Aisles: | 6 |
Number of Load Levels: | Various |
Number of Stacker Cranes: | 6 |
Number of Bays: | 56 |
Pallets per Beam Level: | 2 |
Total Capacity: | 15,400 pallets |
Gallery
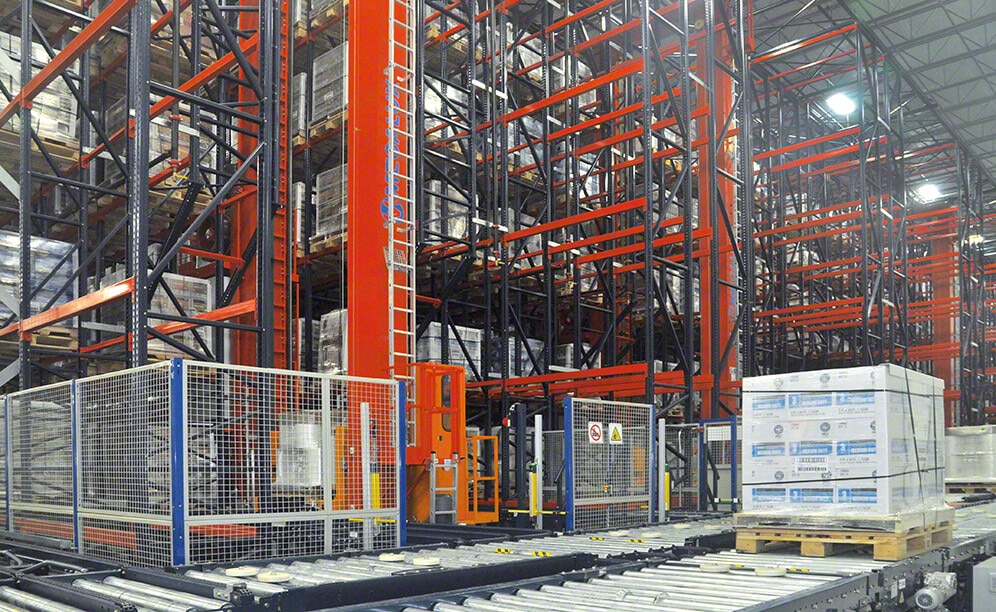
Interlake Mecalux has built a new automated warehouse for Next Generation Films with a storage capacity for more than 15,400 pallets
Ask an expert