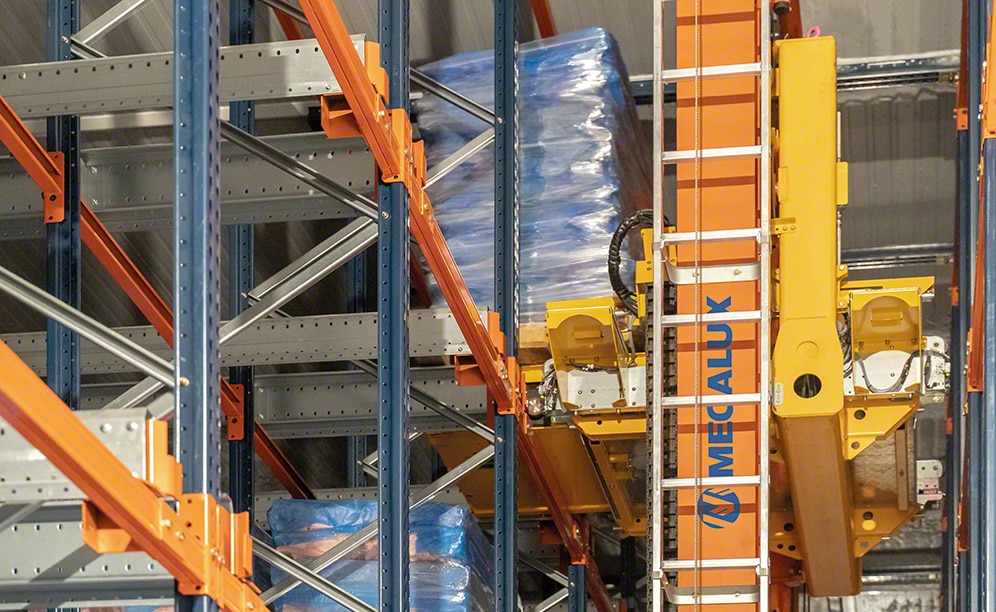
Automated frozen meat storage chamber for Cárnicas Chamberí
The fully-automated frozen-storage installation of Cárnicas Chamberí, where it stores meat products

The Spanish meat company Cárnicas Chamberí has made giant leaps forward in its frozen storage logistics management in Toledo, Spain. Interlake Mecalux recently designed, built and commissioned a new AS/RS that holds close to 1,700 pallets for the business. The Pallet Shuttle was the system of choice —which operates via a stacker crane— because it speeds up the movement of goods and also cuts down on the power needed to create cold conditions.
Dedicated customer service
Cárnicas Chamberí has one of the longest track records in the Spanish meat product business. Established in the 1930s, it first opened a small butcher shop in the Province of Toledo. However, it was not until the 1960s that it opened its first factory.
Thanks to its experience, dependability and its best-in-class attitude, the company has positioned itself as a sector leader in its home country. However, international expansion is on the menu. In the words of Juan Carlos Camacho, Chief Financial Officer at Cárnicas Chamberí, “Things can only get better for our company market-wise, especially in Southeast Asia, something we hope to achieve in less than a year.”
The company already owned a logistics center in the municipality of Toledo and, shortly afterwards, inaugurated another facility a few miles away in the town of Casarrubios del Monte, since, according to the CFO, “we needed more elbow room.”
Both its production plant and its two logistics centers are equipped with cutting-edge technology to keep the business competitive and guarantee maximum product quality. When it came to setting up its second warehouse, Cárnicas Chamberí contacted Interlake Mecalux because, as the customer points out, “we were looking for an automated solutions supplier with a solid reputation.”
According to J.C. Camacho, the company ranked “storage task speed and control over products,” as project priorities.
Building on the idea that automating logistical processes was key for Chamberí Meat, Interlake Mecalux has installed the automatic Pallet Shuttle system. In this solution, the stacker crane is in charge of moving the pallets from the warehouse infeed positions to any storage channel. Once there, a motorized shuttle shifts the pallets and deposits them in each channel at the deepest open position.
Advantages of automated product management
The warehouse, which works at a controlled-temperature of -4 ºF, comprises a single aisle with two blocks of double-deep high-density racks on both sides measuring 23' high.
The racks fill 6,814 ft2 of available surface area, thus providing the maximum storage capacity possible: up to 1,815 pallets with a maximum unit weight of 1.1 t. In parallel, and since it is a high-density system, there is less volume to be cooled and, as a result, reduced power consumption.
On a daily basis, Cárnicas Chamberí receives an average of 120 pallets with finished products and raw materials (primarily pork) and distributes another 150 pallets to its customers in Spain.
Having automated equipment that moves the goods from here to there means the company has lowered the time spent on each operation significantly. Plus, it has streamlined product inputs and outputs and, as such, has heightened its ability to react to fluctuations in demand.
Automation also plays a vital part in maintaining an unbroken cold chain for products. The warehouse is connected to production via a conveyor circuit and, before entering the warehouse, the pallets must go through a staging zone. This comprises an airlock system, with two asynchronous doors. In this way, the chamber is protected from sudden temperature changes caused by the unending stream of unit loads.
Operational control
A fully-automated distribution center like the one Cárnicas Chamberí runs requires a warehouse management software (WMS) that spearheads all merchandise flows: incoming, storage tasks and outgoing. For this reason, Interlake Interlake Mecalux’s Easy WMS was deployed, a system that has helped make the meat company’s supply chain much more efficient.
The large majority of products are high rotation goods, i.e., constant inputs and outputs (although some remain in stock for a while). The WMS is responsible for differentiating between items from the moment they arrive in-warehouse and for assigning them a storage slot. Thus, those with the highest rotation are deposited at the more accessible aisle ends, to speed up their entry and exit. Meanwhile, other products are located elsewhere.
Easy WMS also tracks all merchandise and provides real-time information on stock status. Warehouse managers can consult this information on-the-go and, consequently, make decisions to improve service.
Two rack channels are set aside as storage to distribute urgently needed goods. Each night, at around 2 a.m., Easy WMS orders the stacker crane to send pallets to those channels. So, the next morning, orders are ready to leave the warehouse quicker and be distributed to its customers.
Juan Carlos Camacho Hernández - CFO at Cárnicas Chamberí
“In order to speed up the distribution and delivery of our customers’ orders, we knew we had to get better organized and run fully-automated logistics. We are very satisfied with the warehouse set up by Interlake Mecalux because its commissioning went without a hitch and it has given us solid results.”
Advantages for Cárnicas Chamberí
- Preserving the cold chain: automation ensures products are kept at low temperatures, guaranteeing their freshness and quality.
- Storage slotting speeds: each day the automatic Pallet Shuttle inserts 120 pallets and extracts another 150 from their locations.
- User experience first: the warehouse’s distribution is designed to make storage tasks easier. Easy WMS also organizes nightly order picking for faster daytime distribution and delivery.
Automated frozen chamber | |
---|---|
Storage capacity: | 1,815 pallets |
Pallet size: | 32" x 48" |
Max. pallet weight: | 1.1 t |
Rack height: | 23' |
Gallery
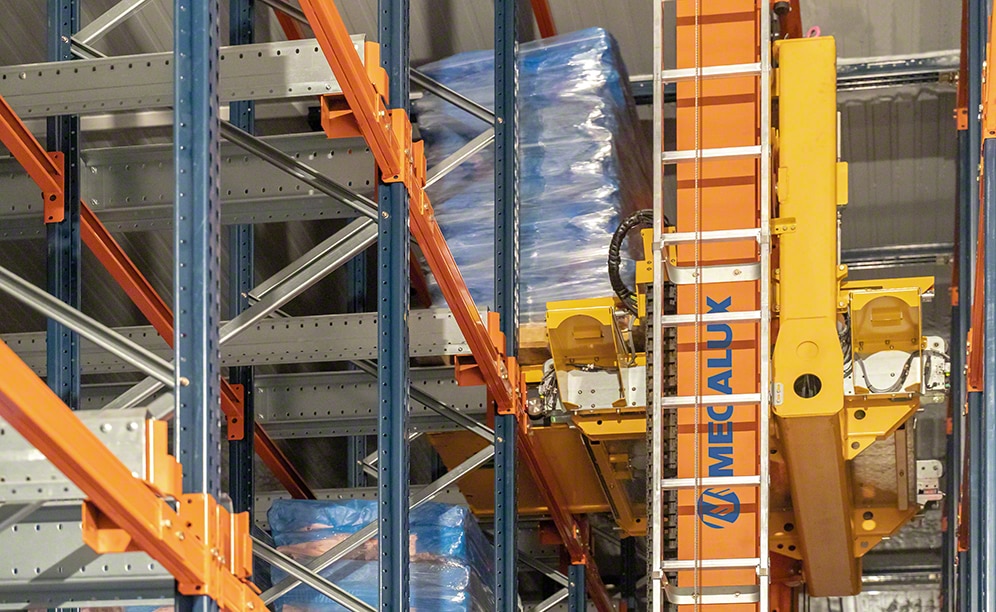
Pallet Shuttle system with stacker crane of Cárnicas Chamberí
Ask an expert