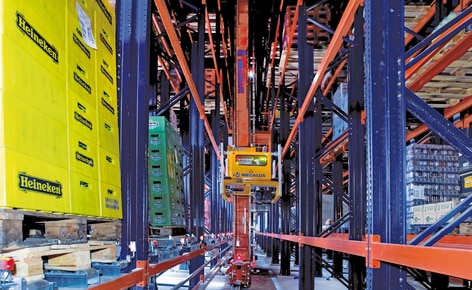
Mecalux increases the storage capacity and picking of a distribution company with the installation of an automated clad-rack warehouse
Amagosa automates the storage and management of its logistics centre in Badajoz (Spain)
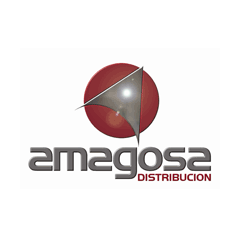
Amagosa, a company specialized in food and beverage distribution, and catering related products, has upgraded their installations in the city of Merida (Badajoz). An automated clad-rack warehouse with conventional pallet racking, pallet flow channels and an annex building which coincides with input and output areas was built for them. They had two Clasimats, pallet racks and a picking station arranged inside the new facility. The Mecalux Easy WMS (warehouse management software), responsible for managing all activities of the center, was also installed.
At first glance
As the years passed by and after experiencing notable growth, the Amagosa installations became too small. It was then that the company opted to improve the performance of its logistics center and, at the same time, reduce work costs.
Mecalux analyzed Amagosa’s needs in detail:
- Automated warehouse
- Annexed building
- Dock, preloading and general warehouse
- Inputs, outputs and control
- Input and output No. 2
- Channels for picking
- Picking station
- Clasimat vertical warehouse
A clad-rack warehouse as a solution
This clad-rack warehouse, measuring 85’ in length and 73’ in height, has two single and double depth aisles that allow for a storage capacity of more than 2,300 pallets. Being ‘clad-rack’ means that the racking forms the building’s structure and that the exterior covering is attached to them.
In each aisle, a stacker crane carries out the movement of the pallets from the conveyor to the location designated by Mecalux Easy WMS. The stacker cranes´ implementation allows for an increase in productivity and at the same time decreases the resources needed for each operation.
Due to the type of goods stored, and for small quantities of products for an item like those Amagosa works with, it was essential for an operator to arrange a picking area swift enough to prepare orders with great speed.
They installed twenty-four pallet flow channels with rollers on the first level of racks where picking of higher consumption ‘A’ type products is done. Each channel, that coincides with the ground floor, can house up to three reserve pallets.
Next to that, a picking station has been set up in the shape of a ‘U’ for products with medium and low turnover (B and C). On both sides of the picking station they have placed two vertical Clasimat warehouses intended to store high value C type products (liquors, high-end wines, cognacs, etc.). Plus, they have raised conventional pallet racks where the most consumed products (B type) are placed.
Preparing orders: steps to follow
- The first operator, assisted by a pallet truck and a computer terminal, takes a pallet and goes along the dynamic channels to do picking of A type products.
- Then, they move toward the conventional pallet racks to take the B type products. Once finished, they leave the pallet in the order fulfillment area, located just behind the picking station and the Clasimats.
- The operator who mans this station prepares waves of five orders at the same time. They are responsible for putting together and finishing the orders by filling the pallet with the picking of all the B and C type products, including those from the Clasimat.
- Once the orders are completed, the operator moves the pallets to the area reserved for replenishment, after passing by the baler machine. This area is located in the old building, situated at the side of the new warehouse.
A Clasimat for all valuable C type products
In the Amagosa warehouse, they have installed two 28’ high Clasimats with 20 trays in each.
These trays, stored in the support structure by a shuttle, are 7.9’ long and are capable of supporting up to 1,102 lb of goods.
Docking areas with light devices
In the old warehouse, which is next door, there are several racks that do not interact with the new warehouse. The only area that is connected is the space reserved for the output docks that are connected via a wide door where the forklifts circulate.
Easy WMS
Amagosa uses the Mecalux Easy WMS to meet all the management needs related to the logistics center.
Easy WMS controls all the entry processes, the location in the warehouse, stocks, location rules, retrieval, the pallets that have to go to picking stations, the picking itself, returns to the warehouse, etc. It is also capable of analyzing the state of distinct parts or areas via query and reporting tools, as well as all the teams that operate in it.
Mecalux Easy WMS (warehouse management software) communicates with the ERP SAP of the customer in a permanent, or bidirectional manner.
Advantages for Amagosa
- Increase in storage capacity: the Amagosa clad-rack warehouse works with single and double-deep racks offering a storage capacity of 3,500 pallets, 31.5” x 47” in size and 6.5’ in height, in a surface area of only 10,764 ft2.
- Efficient picking: the combination of the pallet flow channels, the picking station and the two Clasimats allow them to make efficient preparation of all products (A, B and C).
- Productivity improvement: thanks to the high level of warehouse automatization, the speed of order preparation has increased.
- Perfect stock control: Mecalux Easy WMS manages all the movements, processes and operations that take place inside the warehouse.
Automated clad-rack warehouse. Spain | |
---|---|
Storage capacity: | 2,373 pallets |
Maximum pallet weight: | 1.1 t |
Warehouse height: | 75’ |
Number of stacker cranes: | 7 |
Type of stacker crane: | single-mast |
Picking channels: | 24 |
Construction system: | clad-rack warehouse |
Gallery

Vista de uno de los transelevadores para pallets de la bodega automática de Amagosa
Ask an expert