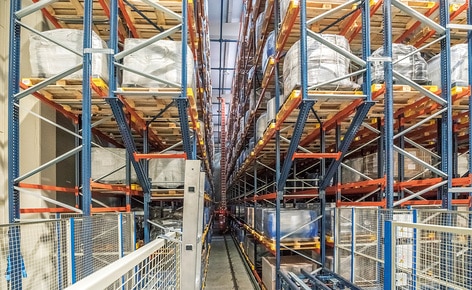
Chemical manufacturer Trumpler builds an automated warehouse with stacker cranes and conveyors next to its factory in Barcelona
Simplicity and productivity in Trumpler’s AS/RS installation
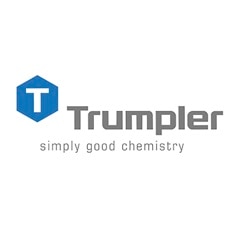
Interlake Mecalux has built an Automated Storage & Retrieval System (AS/RS) for the chemical company Trumpler, consisting of two double aisles with double-depth racks on both sides. Two twin-mast stacker cranes with telescopic forks are in charge of introducing and removing the goods from their corresponding locations. This facility, located in Barcelona, has a 2,512 pallet capacity and the entire operation is supervised by the Easy WMS warehouse management system from Interlake Mecalux.
About Trumpler
Trumpler is a multinational company that focuses on the manufacture of chemicals for all leather making processes. It was founded in 1975 in Barcelona and in the 80s began expanding internationally. Currently, it is present in most of the world, with offices in Mexico, Brazil, China, Germany and Italy.
The company is especially aware of the impact its business has on the environment. For this reason, it offers products and solutions with a low carbon footprint and more than 40% of the raw materials it works with come from renewable sources. Responsible business practices will continue to be a priority.
Needs and the solution
The company did not have enough room to store the more than 500 SKUs in its Barcelona production center. Faced with this situation, it required a high capacity warehouse, which would ensure a continuous flow of products with greater flexibility and at an affordable cost.
After an in-depth analysis of the specifications and needs of the company, Mecalux proposed the construction of a 9,041 ft2 AS/RS inside the Trumpler building. The site’s design was based on the dimensions of the automated warehouse to make full use of the available space, i.e., the racks were designed first and then the building was constructed. Thus, Trumpler obtained a 2,512 pallet storage capacity for raw materials and finished products.
This new warehouse stands out for its simplicity and efficiency. The inputs and outputs of goods are carried out automatically through a circuit of chain and roller conveyors, in addition to a transfer car. Human intervention is not needed, hence logistical errors are avoided. The warehouse layout is as follows:
- Entry point
- Pallet dispenser
- Stretch wrapping machine
- Checkpoint
- Rejected pallet exit point
- Access doors
- Warehouse
- Transfer car
- AS/RS stacker crane
- Exit doors
- Dispatch docks
Warehouse entrance
At the front of the warehouse, the inputs and outputs of goods take place separately to avoid interference. Before introducing the goods from the production center, there are three different processes performed to ensure the pallets are in good condition and meet requirements.
This center operates with 48” x 48” slave pallets. Thus, unit loads can be placed on pallets of different qualities, strengths and sizes. Once products are placed on slave pallets, a stretch wrapper is responsible for grouping and protecting them to ensure load stability.
The pallet transfer car
Once inside the warehouse, a transfer car moves the pallets to the storage aisle assigned by the Easy WMS management system by Mecalux.
These machines move along rails, connecting the input conveyor and the aisles swiftly.
At the end of each aisle, there is a chain conveyor where the pallets are deposited. Stacker cranes collect the goods directly from the conveyor to place them in the appropriate rack locations.
Pallet storage aisles
The warehouse is composed of two aisles with double-deep racks on both sides that measure 125’ long and 50’ high. In this storage system, two pallets of the same SKU (one behind another) are introduced on the same side of the aisle.
Two twin-mast stacker cranes, one in each aisle, move pallets between the racking locations and the input and output conveyors. They move at a travel speed of 394 ft/min and 125 ft/min when raised, enabling 50 combined cycles/hour (50 input and 50 output pallets).
The goods leaving the warehouse repeat the same operation as when they enter, but in reverse. The pallet transfer car collects the pallets directly from the conveyor at the end of each aisle and moves them to the exit.
At the exit point, a monitor provides useful information for operators, such as the order corresponding to the pallet, the characteristics of each order or what docks are assigned the loads.
Personnel, using counterbalanced forklifts, remove the pallets from the output conveyors and feed them directly into the transport vehicle.
An intelligent WMS
The installation is also furnished with the Easy WMS warehouse management system by Mecalux. It is the brain of the warehouse, whose mission is to direct all internal operations (including the receipt, storage and dispatch of products). This WMS is very versatile and can meticulously control stock levels, knowing at all times the location and status of the goods.
The Easy WMS by Mecalux is in constant two-way communication with the Trumpler ERP. Both programs transfer data and critical information to achieve maximum profitability and warehouse throughput.
Advantages for Trumpler
- Small space, top capacity: in just 9,041 ft2, the company achieves a storage capacity for 2,512 pallets of raw materials and finished products.
- Boosted productivity: simplicity in warehouse organization and operations ensures high throughput and agility in the run times of all processes.
- Efficient management: the warehouse is directed and organized using the Easy WMS by Mecalux and the Galileo control software.
Trumpler’s AS/RS installation | |
---|---|
Storage capacity: | 2,512 pallets |
Pallet sizes: | 48" x 48" |
Racking height: | 50' |
Racking length: | 125' |
No. of aisles: | 2 |
Gallery
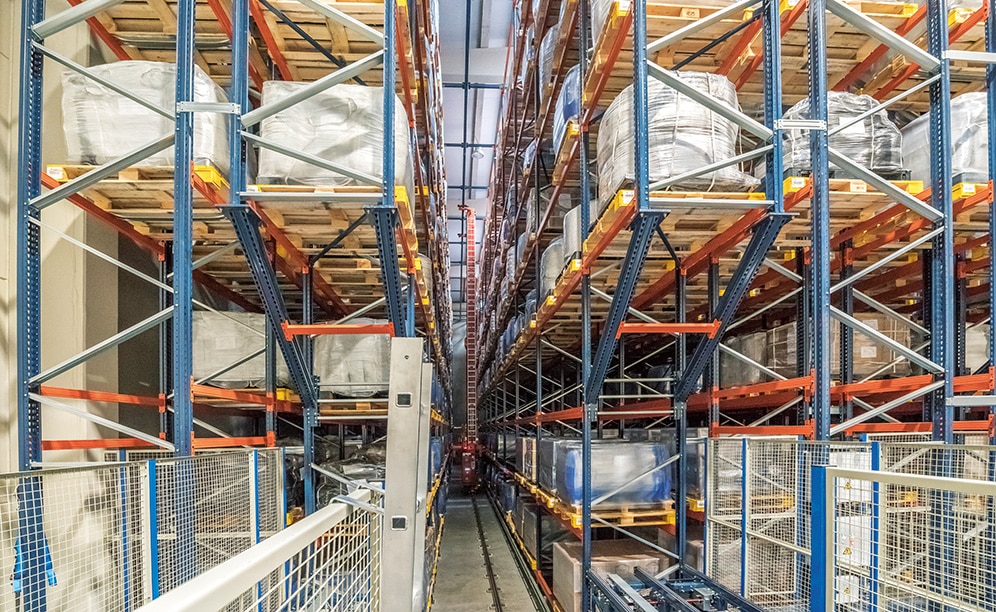
Mecalux has built an automated warehouse for the chemical company Trumpler, consisting of two double aisles with double-depth racks on both sides
Ask an expert