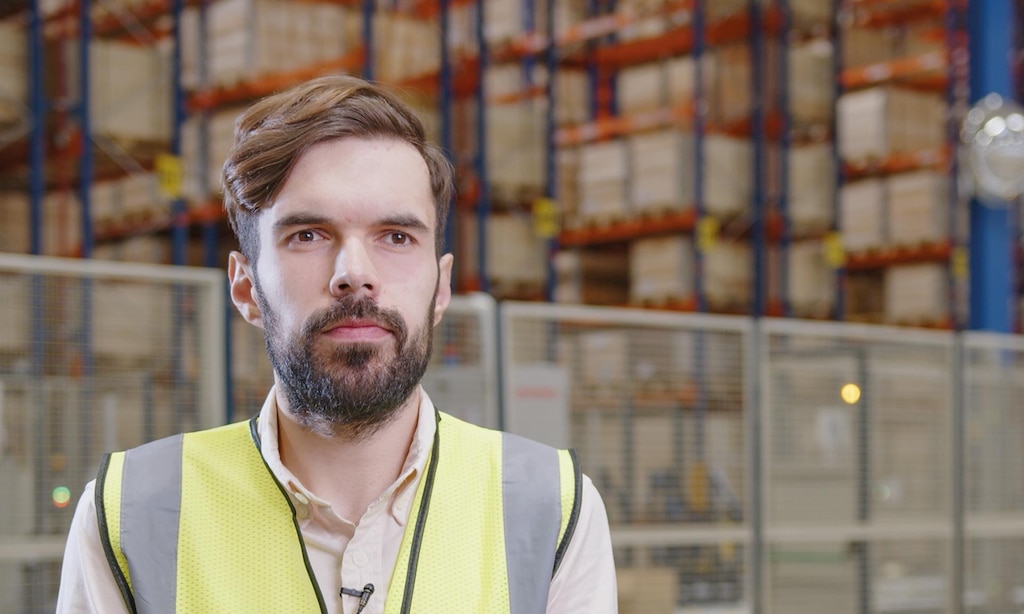
“We automated our warehouse without shutting down operations”
About IKEA Components
IKEA Components, a subsidiary of Swedish multinational IKEA, is responsible for packaging and delivering furniture components and accessories. The company automated its facility in Malacky (Slovakia), installing trilateral stacker cranes without interrupting its ongoing operations. Additionally, it implemented the Easy WMS warehouse management system to enhance its efficiency.
Mecalux interviews Pavol Masarovič, Operations Manager at IKEA Components Slovakia. The subsidiary automated its warehouse in Malacky (Slovakia) without ceasing operations, boosting its order fulfillment capacity.
IKEA is present in 62 markets and has over 450 stores. What were IKEA Components’ logistics processes like prior to automation?
Up to that point, all operations in our outbound area were conventional. That is, operators carried out all pallet movements and transfers using forklifts or in narrow-aisle racking. We would take pallets from the production area and store them on the racks. This working method required more time, more material handling equipment, and more coworkers busy doing the same tasks. So, we decided to automate certain aspects.
Mecalux automated IKEA Components’ Malacky warehouse without disrupting operations. How was that project carried out?
The main requirement we presented to Mecalux was to prepare and design the whole process so that it wouldn’t interfere with ongoing warehouse operations during its implementation. That was something we requested from day one. It wouldn’t have been possible to shut down the area entirely.
The project was split into four phases. In each stage, Mecalux installed three trilateral stacker cranes and extended the conveyor line. By dividing the project into different phases, we managed to complete it while affecting only 25% of capacity during each one. So this work really didn’t impact us; it didn’t affect our daily activity.
Now, we can focus on managing stock while the automated systems take care of moving pallets
What advantages has IKEA Components seen with the automated storage and retrieval system (AS/RS)?
It’s brought us much more flexibility and efficiency, starting with pallet movements. Before, we had to do everything manually. But now, we no longer worry about transporting pallets because automation does it for us. This lets us focus on managing stock. Storing products in an AS/RS has provided us with better inventory visibility. Plus, this way, it’s harder to make mistakes compared to conventional management.
The AS/RS is easy to control because it’s run by the Easy WMS warehouse management system. The software oversees all processes, and when it’s time to ship pallets to our clients, it sends instructions. The pallets them leave the AS/RS autonomously.
We’ve seen the benefits of automated storage systems firsthand, especially during the pandemic. Some people were out on sick leave, but with an AS/RS that pretty much runs on its own, we were able to continue fulfilling our clients’ needs and ship all the pallets they ordered.
-
“We completed the installation over four phases while affecting only 25% of total capacity” What route does a pallet take from its entry in the AS/RS to its exit?
All pallets arriving at this AS/RS for distribution come from our production area. Automated guided vehicles transport them from our pallet finishing line. Next, they’re placed on the conveyor belt and arrive at the pallet checkpoint installed by Mecalux. Then, Easy WMS assigns the goods a location and issues the task to automatically move the pallet to one of the 12 storage aisles. Afterwards, when a pallet needs to be shipped to a client, the entire process is automated, from the time an operator gives the command. Depending on their final destination, pallets leave the AS/RS on a specific conveyor line and head to one of the loading areas via the shortest possible route.
How would you assess this intralogistics transformation?
The Malacky project was a venture that spanned almost three years. We faced several challenges, but we managed to respond to all of them very professionally and without losing sight of our goal: to enhance efficiency. The cooperation with Mecalux was highly professional; we had an excellent working relationship. And in the end, we completed the task successfully. Many people took part in the project, on both Mecalux’s part and ours. All in all, it was a tremendous project for everyone involved. Everybody learned something new. We all gained new skills and experience, which will definitely serve us well in the future.