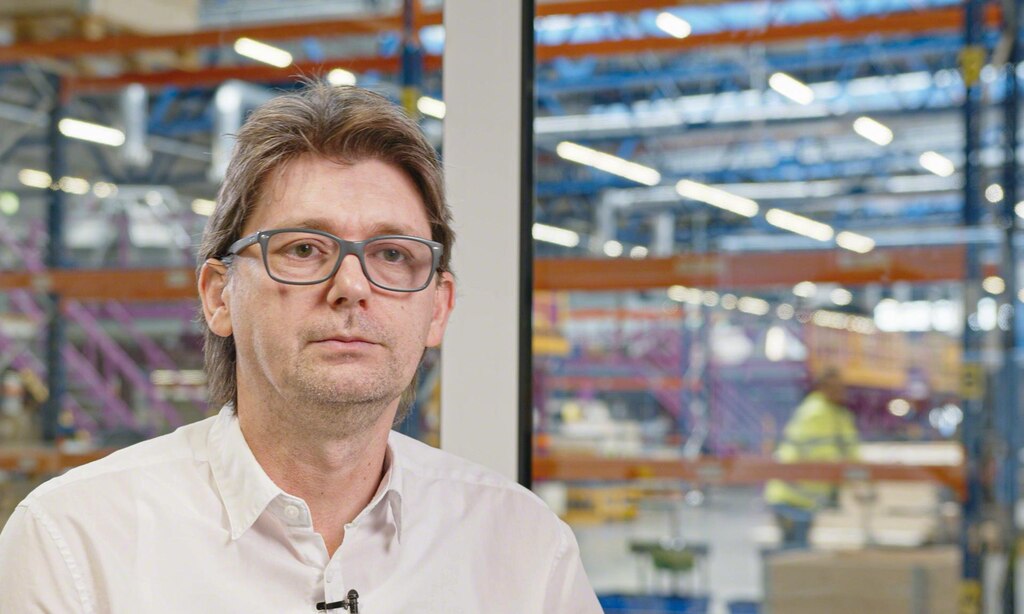
“We’ve reached the goal of maintaining our fill rate at 99%”
About IKEA Components
IKEA Components, a subsidiary of Swedish multinational IKEA, is responsible for packaging and delivering furniture components and accessories. The company automated its facility in Malacky (Slovakia), installing trilateral stacker cranes without interrupting its ongoing operations. Additionally, it implemented the Easy WMS warehouse management system to enhance its efficiency.
Mecalux interviews Frantisek Stora, Managing Director of IKEA Components Slovakia to find out how automating its facility with trilateral stacker cranes has helped the company ensure good internal availability of its products.
How critical are logistics processes for a company such as IKEA?
They’re so vital that you could say that IKEA Components is a logistics company in itself. As the data show, we dedicate more time to distribution than manufacturing. For us, it’s essential to have highly stable intralogistics processes and to work on the development of skills and equipment that support this area.
One of our main KPIs is what we call order access fulfillment or the fill rate. We measure whether orders have been shipped in the correct quantities and within the appropriate time frames. Having extremely efficient operations has had a very positive effect on this KPI.
We automated an existing facility that already had racks
You’ve automated your warehouse in Malacky. Had you ever transformed a manual facility into an automated one?
We had experience with automation in warehousing, but until now, we’d implemented it in greenfield projects, conceived from scratch. With Mecalux, we transformed an existing facility that already had racks. That was slightly more complicated than our previous experiences. Nevertheless, we completed the project side by side, and it’s been very gratifying for us.
What advantages has IKEA Components seen with these changes?
We’d set the goal of maintaining our order access fulfillment rate at 99%, which we’ve achieved. Moreover, intelligent automation has enabled us to ensure good internal availability of our products. As a result, we can complete our orders in line with all deadlines.
-
“We’re determined to continue this work and focus on automating our logistics operations” Does automation improve the way companies work?
I think so, and for us, it’s fundamental. At IKEA Components, the focus in recent years was on automating the production lines. However, now, we’re concentrating on our logistics operations. We’re determined to continue this work, even though it may seem like a lengthy process at first.
We’ve already automated 99% of our pallet storage space, but there’s still room for improvement. That’s why we feel it’s necessary to constantly explore to discover new advancements. We foresee very interesting challenges in two areas. The first is automatic truck loading and unloading, and the second is material handling.
How would you describe IKEA Components’ relationship with Mecalux?
It’s a very professional relationship. We’d worked with Mecalux prior to implementing this project, and once again, they’ve demonstrated their expertise in automating this automated storage and retrieval system (AS/RS) for distribution. Without a doubt, Mecalux is a company highly committed to service. We encountered a few obstacles when installing the trilateral stacker cranes and Easy WMS software, but Mecalux responded quickly and resolved all issues.