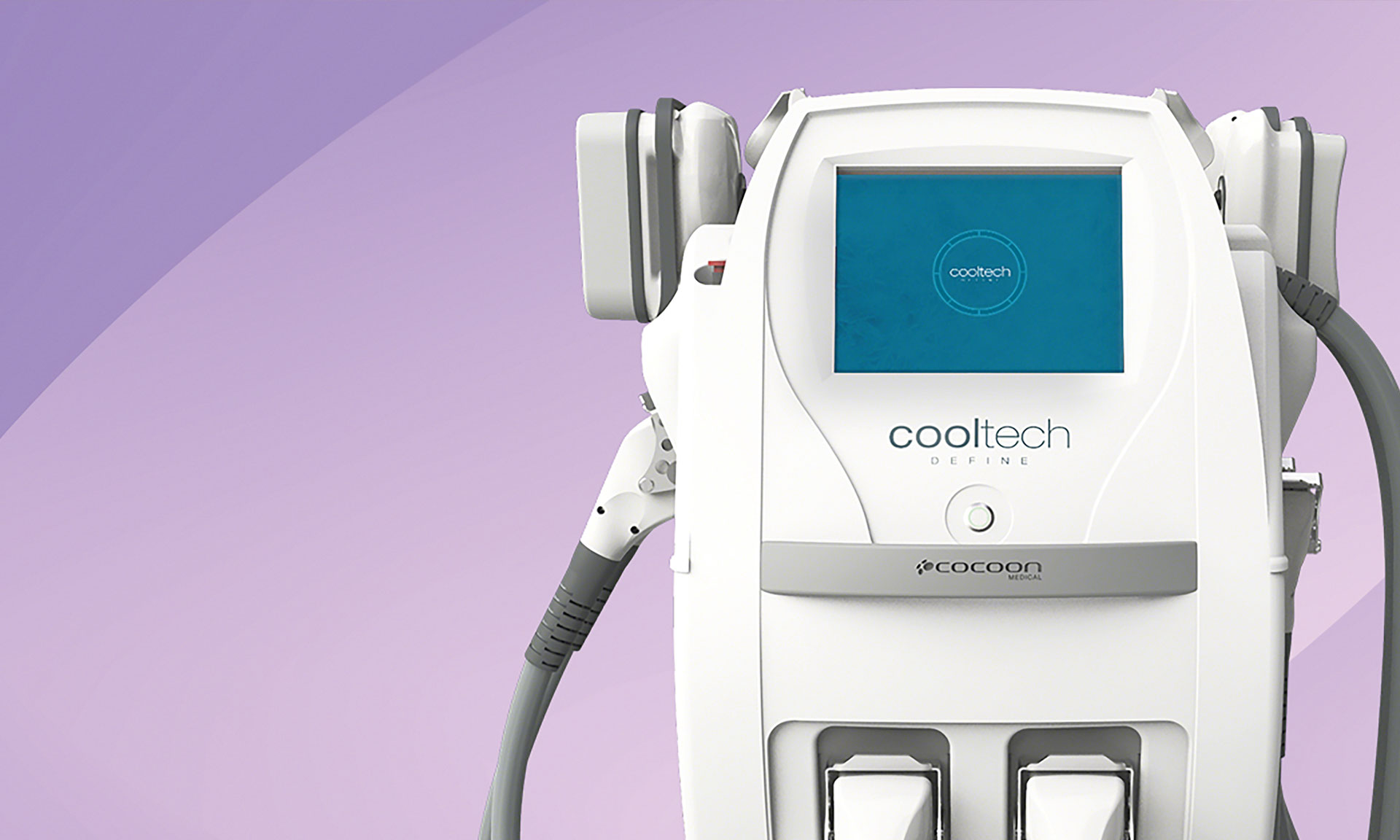
Sinclair Pharma: Easy WMS manages warehouses in Spain and Bulgaria simultaneously
Sinclair Pharma, an aesthetic medical device manufacturer, controls its warehouses in Bulgaria and Spain concurrently with Mecalux’s Easy WMS.
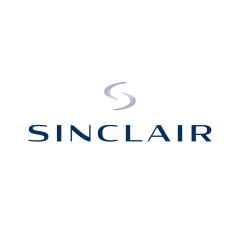
Sinclair Pharma, a technology company specializing in aesthetic medicine, has installed Mecalux’s Easy WMS to manage its warehouses in Spain and Bulgaria. The system ensures the traceability of SKUs, including components sent to the assembly lines and finished goods.
From Cocoon Medical to Sinclair Pharma: innovation and evolution
Founded in 2010 in Barcelona, Cocoon Medical develops cutting-edge technology in the aesthetic medicine field. It has a vast network of distributors in over 60 countries and production plants in Spain and Bulgaria. Since 2021, Cocoon Medical has been part of Sinclair Pharma, a global company operating in the aesthetics market and present in Europe, the US, Mexico, the UAE, Russia, and South Korea. Founded in 2010, the company is present in over 60 countries and has a total storage area of more than two acres.
CHALLENGES
|
SOLUTION
|
BENEFITS
|
---|
Since it started doing business in 1971, Sinclair Pharma has steadily expanded. In 2021, it announced the acquisition of Cocoon Medical, a business dedicated to developing state-of-the-art technology for aesthetic medicine. This new Sinclair Pharma division has two production centers: one in Badalona (Spain) and another in Sofia (Bulgaria). At these facilities, it manufactures medical equipment for pressotherapy, cryolipolysis, and laser hair removal treatments, distributing the devices to clinics in more than 60 countries.
“As manufacturers of medical equipment, we have a highly complex supply chain,” says Santiago Prieto, Operations Manager at Sinclair Pharma. “Managing these types of medical devices presents several logistics challenges, primarily traceability and agility.”
In Sinclair Pharma’s warehouses, items require careful handling. This calls for coordination and strict monitoring of logistics processes to minimize any risk of impact. Added to this difficulty is the need for punctual deliveries. On-time distribution is crucial in the aesthetic medicine industry, as clinics and professionals depend on specific equipment to administer their treatments.
“The demands placed on our logistics operations have increased as the company has grown and entered new markets. Our mission is to provide aesthetic clinics with high-tech, customized solutions,” says Prieto. “We needed a digital tool that would help us oversee our daily activities and give us better control over inventory in our warehouses.”
To optimize its logistics processes, the company installed Mecalux’s Easy WMS warehouse management system. This solution enables Sinclair Pharma to closely track the SKUs distributed across its logistics facilities in Bulgaria and Spain. Its products include parts and components as well as finished goods.
Logistics software integration for Sinclair Pharma’s multi-warehouse management
The Bulgarian plant manufactures most of Sinclair Pharma’s medical devices sold throughout Europe. Its logistics facility — covering almost two acres — houses components and parts sent to production in addition to finished goods ready to be shipped to customers.
At Sinclair Pharma’s warehouse in Spain, medical devices manufactured in Bulgaria are managed and distributed to clinics across the country. The Spanish facility also stores components for technical repairs.
Sinclair Pharma controls the two warehouses simultaneously with Easy WMS. The system is prepared to monitor stock and organize operations in both facilities at once, regardless of their location in different countries.
For this purpose, the company implemented Easy WMS in the software-as-a-service (SaaS) model. “We chose this option because of its compatibility with our SAP ERP system, which also runs in the cloud,” says Prieto. The program is stored on external servers, and users can access its functionalities from any device with an internet connection.
Employing multi-warehouse management software like Easy WMS makes communication between the two logistics facilities much smoother. The system tracks all movements produced, from goods receipt to order processing. “By digitalizing our logistics operations, we’ve standardized them. Now, we can monitor how processes are performed in each warehouse more rigorously,” says Prieto.
For Sinclair Pharma, growth goes hand in hand with territorial expansion and the commissioning of new distribution centers. “Easy WMS is a scalable software program, so it will be able to manage any warehouses we open in the future,” says Prieto.
Benefits gained from implementing Mecalux’s digital logistics solutions
When streamlining logistics operations, stock management is a critical process. The Mecalux software has enabled Sinclair Pharma to organize its processes flawlessly.
Everything starts in the receiving area. As products arrive at the warehouse, Easy WMS organizes them considering several variables: whether they are components to be used on the assembly lines or finished goods, their SKU type, and their demand level.
“Each medical device requires around 2,000 SKUs for its manufacture. With such a large and varied number of parts, the challenge of avoiding any possibility of error was monumental,” says Prieto.
To minimize mistakes, Easy WMS ensures real-time product traceability. Thus, Sinclair Pharma knows the exact location of each item. Additionally, it maintains a detailed record of all goods movements.
“Another hurdle was speed. We need to supply the production lines with the necessary raw materials at the right time, without delay,” says Prieto. Order picking is a key operation for the company. In the warehouse in Bulgaria, for example, operators move through the aisles as directed by the Mecalux software, locating the components required on the assembly lines. “The system guides the operators at every turn. With the instructions from Easy WMS, we’ve noticed a qualitative leap in picking tasks. Our employees are much more efficient, quicker, and they don’t make mistakes,” says Prieto.
Upgrading Sinclair Pharma’s supply chain
The implementation of Mecalux’s Easy WMS software has marked a significant milestone in optimizing Sinclair Pharma’s logistics processes. The medical device manufacturer has surmounted the obstacles associated with managing a complex supply chain and multiple warehouses in different countries. Thanks to Easy WMS’s ability to simultaneously oversee operations in Bulgaria and Spain, Sinclair Pharma has enhanced traceability, agility, and coordination across all processes. This improvement spans from the receipt of components to the delivery of finished goods to the company’s international network of clients.
“Sinclair Pharma has a global presence that extends to both the countries where it has established offices and those where it doesn’t yet have a physical foothold. In regions where we don’t have our own facilities, we work closely with specialized distributors who handle final sales,” says Prieto.
Logistic digitalization has enabled Sinclair Pharma to standardize operations and more accurately monitor the performance of its processes. As a result, it can now provide aesthetic clinics with personalized medical solutions. The integration of cutting-edge technology strengthens the company’s position as a leader in the cosmetic medicine industry, ensuring the satisfaction of its clients’ demands and driving its growth.
With the instructions from Easy WMS, we’ve noticed a qualitative leap in picking tasks. Operators are much quicker, and they don’t make mistakes.
Ask an expert